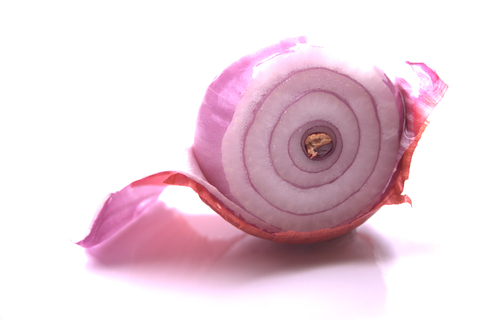
The secret to closing open CAPAs by 50%
To check our compliance with US regulations, StarFish engaged Larry Spears, retired Deputy Director of CDRH to conduct an FDA mock inspection of our Quality Management System. The inspection was a great experience for all of us and gave us a good overview of where the FDA investigators would be focused. Not surprisingly Corrective and Preventive Actions (CAPA) were the major focus. That’s when we discovered the secret to closing CAPAs by 50%.
Before I elaborate more, I should explain how our CAPA system is set up, as it is somewhat unusual. As a contract manufacturer, in order to protect confidentiality of our clients, we handle product CAPAs via the complaint and Returned Material Authorization (RMA) and Engineering Request (ECR) processes that are auditable by our clients on a per product basis. StarFish is a registered contract manufacturer with the FDA for several products that are marketed in the US. In order to meet the 3 major markets’ requirements (US, EU and Canada), our Quality Management System (QMS) is based on ISO 13485, 21 CFR part 820, the EU Medical Device Directive (MDD) and the Canadian Medical Device Regulations (CMDR).
Our overall CAPA system covers our internal systemic issues, process improvements and QMS updates. Therefore, the FDA would probably be more interested in our complaints RMA, and ECR issues than our internal CAPAs. I am very pleased to say that there were no observations noted regarding product related CAPAs but we did have an observation regarding internal CAPAs – mainly that after we identify an issue we take a long time to close it. Naturally, this prompted our QA/RA team to jump into action and see what we can do to improve the situation.
We reviewed all open CAPAs and found that we get ‘stuck’ after the investigation has been assigned. Determining a root cause was a common stumbling block and having a small focused team was more effective than leaving this to a single assignee. Further follow up on issues uncovered that many of the identified issues were not specific enough and the personnel assigned to resolve them were not clear on how to handle it. In some other cases, corrective actions were clearly identified but were overwhelming for a single assignee to handle. In cases of QMS updates, some CAPAs were assigned to personnel who had other conflicting priorities so there was lack of prioritization and delegation within the department.
In June and July, QA/RA personnel started to follow up with the Management Team as well as with the individual CAPA assignees. We have reviewed each CAPA, investigated root causes, updated action items, set up clear expectations for verification of the effectiveness of each issue and agreed on due dates. The result is we were able to reduce the number of CAPAs by approximately 50% – that’s what I would call QA heaven as it is a pure joy to successfully resolve and verify that there are no more issues in a particular area of our operations.
The key to a successful CAPA system is having Management support and consistent follow up (and more follow up, follow up…) so that issues don’t slip through the cracks. The QA/RA team plays a main role in providing guidance to both the Management Team and to personnel working on CAPAs. We can never give up!
Vesna Janic is a Director of Quality/Regulatory at StarFish Medical. She uses her expertise in quality systems and regulatory compliance to guide our QA/RA team and help clients avoid wasting time on their path to the market.
Photo credit: 10812718 © Andesign101 | Dreamstime.com