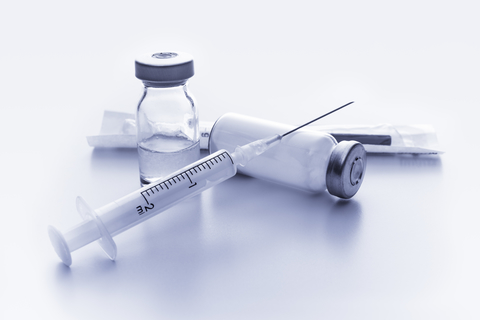
Medical applications and early stage design – silicone material selection
We often design elastomeric components that will be used in contact with the human body, and silicone is usually our “go-to” material. Attractive for many reasons, silicone can be used from early stage prototyping through to production.
The two key variables in rapid silicone prototyping are material selection and moulding strategy. Both must work together to achieve the desired results. Silicone material selection will be discussed here, and moulding strategy in part two of this blog.
Medical Applications and Early Stage Design
Silicone materials have been used in medical applications since soon after their commercial availability. In the mid-1940s, silicone based compounds were discovered to prevent blood coagulation, thus making them the ideal coating substrate for syringes, needles and other glassware in medical equipment. Silicone has been used in a wide variety of medical devices due to its bio-compatibility and bio-durability, which can also be expressed in terms of hydrophobicity, low surface tension, and chemical and thermal stability.
What makes silicone an even more interesting material from a design stand point is its mouldability characteristics. Room Temperature Vulcanization (RTV) silicones allow the easy production of elastomeric customized prototypes, which is really useful during the early design phase of a product. High performance RTV silicones are often presented as a two part material: raw silicone rubber (base) and the curing or vulcanizing agent (catalyst). When these two products are mixed, the vulcanization (or curing) process starts, bringing the initial viscous material to its final (and harder) state. Final products can then be obtained by processes like casting, compression or injection (not to be confused with rigid-plastic injection moulding).
Material Selection
There are two main groups of RTV Silicone, depending on the catalyst agent used for the curing process. Tin silicones, also called condensation-cured silicones, are the most economical. Tin silicones are commonly used in mould production for casting other materials such as urethanes or low temperature melt metal alloys. Platinum silicones, also known as addition-cured silicones, have better properties than the Tin silicones: they present low shrinkage rate, long shelf life and can be easily found bio-compatible and “food safe”. The downside of platinum cured silicones is their higher price. Either tin or platinum silicones can be used for casting, however, what is really going to influence the material are other specifications the final prototype must comply with. The following are the most important specifications to consider:
Durometer: Most vendors classify their silicones depending on the durometer, which is a measure of the hardness of a material. Confusingly, there are three shore scales for soft, medium, and hard (shore O, shore A, and shore D), each of which are sub-divided by number. Although RTV silicones can be found at the range of 10 shore 00 (extra soft) to around 70 shore A (medium/hard) durometer, the most common ones range from 10 to 40 shore A durometer.
Colors: It can be difficult to find the silicone you want with the right color and durometer. Silicone compatible colorants together with a transparent or translucent base are a common strategy to colorize silicone (you don’t want to find yourself fighting against the color spectrum … been there done that). The downside of this is repeatability, which can be difficult if the dye is not carefully measured in.
RoHS, REACH and bio-compatibility: Nigel kindly reminded us how critical the RoHS directive could be during product design. Polymers are very susceptible to restricted additives, so making sure the silicone we chose is RoHS, REACH and bio-compatible silicone can help us avoid important problems down the road, especially if the prototype is used in Europe or in clinical trials.
Production Compatibility
At this point we should have the perfect silicone to produce the prototype we want. However, is this silicone going to be compatible with “how” we produce the part? The main properties to consider are viscosity, curing time and pot life. Viscosity will play an important role on how the material flows within the moulds. If the mould contains narrow paths or areas of difficult access, a viscous silicone will probably leave imperfections on the final parts. Trapped air bubbles and incomplete filling are the most common issues.
Curing time refers to the amount of time that a certain silicone takes to fully cure. Most of the silicones take around 16 to 24 hours, however, some others can cure in less than 1 hour. Pot life refers to the amount of time allowed for manipulation after base and catalyst have been mixed, and before the silicone begins its curing process.
Pot life could be critical when several steps (e.g. degassing) must be followed before the silicone is poured into the mould.
Now that we understand material properties, I will talk about silicone moulding strategies in my next blog.
Joan Hereter Gregori M.Eng. is a former StarFish Medical Mechanical Engineer. He helps develop criteria for materials selection as part of his work in product development. A native of Catalonia, Joan includes salsa as a hobby– “Salsa, it’s always to spice up things!”
Image: 26142679 © Alexander Raths | Dreamstime.com