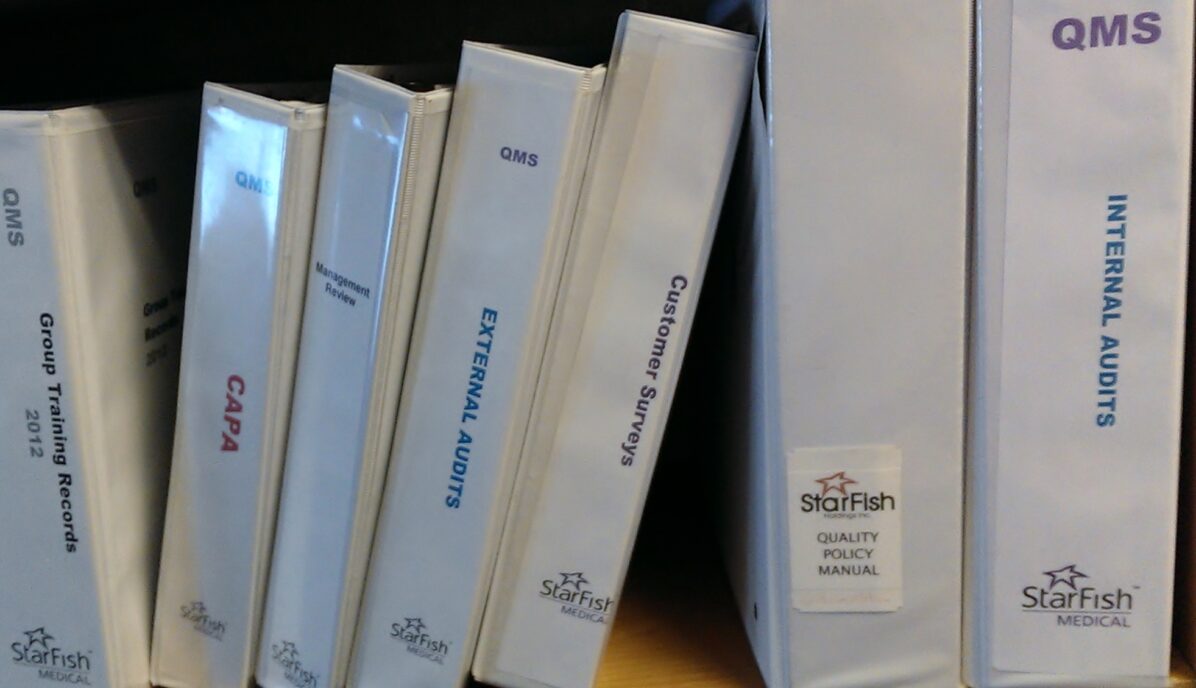
How to write a Medical Device Quality Manual (3 simple rules)
My first experience with a Medical Device Quality Manual was not a good one. The manual for an ISO 9000 certified company consisted of the standard with the words “the company will” inserted before each clause. A slight exaggeration, but you get the point.
After reading the manual one had very little idea of how the company intended to do anything.
Quality systems, like everything in the regulatory world, have a structure. This structure is defined in the quality manual. Everything starts with the manual. How it is written will have a big impact on how successful the system will be.
A good quality medical device quality manual should give the reader a clear picture of how the organization addresses the requirements of the standard. ISO defines quality as the ability to meet requirements. The standard is the requirement, and the policy manual is the plan for meeting that requirement.
The standard is process driven so identify the main processes and how they interact. For most companies the processes are some variation on:
- Accepting customer orders (who accepts the order and who do they tell about it?)
- Evaluating the orders (is it from a customer in a jurisdiction where we have clearance to distribute the device?)
- Fulfilling the orders (this usually involves manufacturing the product and making sure the right customer gets the right product at the right time)
- Handling any feedback (is the product meeting the customer’s needs? Is the product as safe and effective as we estimated during development?)
Each of these processes will require documents, generate records, require training and resources, and need monitoring to ensure everything is working as planned.
Keep it simple. Address only how the standard relates to your organization and not the general case. There are only 20 pages in the ISO 9000 standard, but in some cases a single sentence can have big consequences. An example is clause 6.2.2 a, which reads, “The organization shall determine the necessary competence for personnel performing work affecting product quality”. Working backwards, what is product quality, whose work affects product quality and what training/qualifications are needed to make sure that work is done correctly?
Avoid the inclusion of good intentions. Writing a medical device quality manual that describes who you want to be may seem like a good motivational tool, but the continuous audit findings and sense of failure usually has the opposite effect. Use something else such as a vision statement and quality objectives to motivate the company, write the manual to accurately reflect what is current.
Medical device quality manual summary
- Identify your specific processes and how they interact
- Keep it simple, the medical device quality manual is a strategic document, tactics go in the procedures and work instructions
- Describe what is being done, not what you wish was being done
Rob Keur is a former regulatory affairs expert at Starfish Medical. He follows his own advice when providing Regulatory Support and Quality Management services.
Images: StarFish Medical