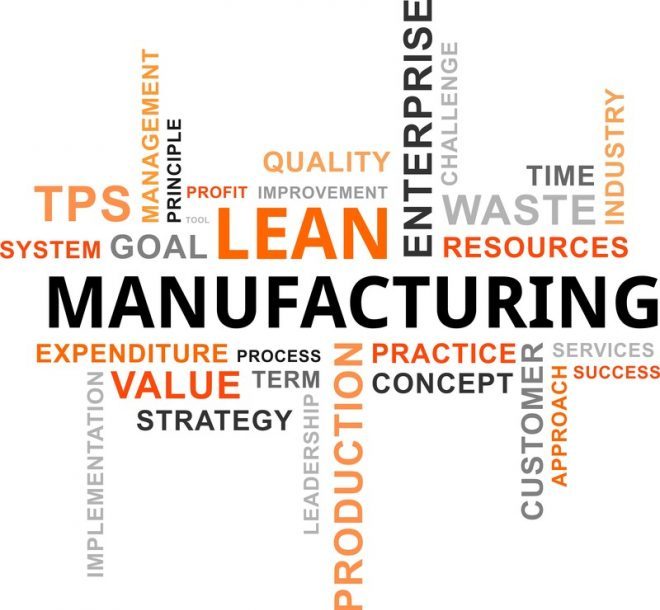
5 LEAN Manufacturing Techniques for Medical Device NPI
Waste in manufacturing drives up product costs affecting both short term profitability and the long-term adoption curve. LEAN Principles that reduce waste are widely adopted to improve high volume manufacturing, but how can they be applied to New Product Introduction (NPI) for medical devices?
This blog shows how applying these 5 LEAN Manufacturing Techniques for Medical Device NPI can help to ensure a smooth and successful product launch.
Everyone can agree that NPI is a difficult and critical phase in a product’s lifecycle. Processes are immature, data is limited, and designs may not be fully realized. Tools such as Design/Process Failure Modes & Effects Analysis and Kanbans help prevent failures, but we can dig deeper and apply the following additional LEAN Techniques.
1. Define Value
Typical strategies to minimize non-value added activities are often overcritical of the inherent design / improvement cycle of Plan, Do, Check, Act. Allowing for additional time to consider the 8 LEAN wastes: Transport, Inventory, Motion, Waiting, Overproduction, Over-Processing, Defects and Knowledge, earlier in the project’s development can provide more value added in the long run since the relative cost multipliers for product changes are 1x in development, 10x in transfer, and 100x in manufacturing.
2. Map Value Streams
Value stream maps help to identify bottlenecks within a given system. But creating a value stream map during NPI is particularity difficult because the 3 types of flow: Material, Information and Time, do not always concretely align to the definitions. The addition of a fourth type of flow, Knowledge, can help to distinguish and track lessons learned which will deliver better communication during transfer.
3. Create Flow
The use of project milestone and performance review gates is an established tool to help control the flow of NPI transfer from design to manufacturing. But Gates alone cannot guarantee a smooth transfer as they do not fully consider the flow of resources. Creating small inter-disciplinary teams early in the design process helps to ensure effective transfer of knowledge from components up to the system level. Visibility of each team member’s workload and availability is critical to ensure that the right person is working on the right job, especially when critical issues arise. Without the proper management of time and knowledge, projects can easily get bogged down in repetitive inefficient cycles.
4. Establish Pull
A common error during NPI is to base planning on an infinite capacity model which ignores resource constraints and works backwards from a due date. This type of planning wastes time and resources and increases the risk of errors. Proper planning using a finite capacity model to produce units based on customer demand and available resources should be implemented instead. It will emphasize the importance of effective communication between the supplier and customer to ensure that key project milestones are met efficiently.
5. Optimize
The main hurdle to improving NPI processes is a lack of Key Performance Indicators (KPIs). Typically, only the bill of materials (BOM) cost or budget is tracked. In order to make improvements, measureable metrics need to be established first. Some examples of KPIs for NPI are lead time between gates, workload balancing, and the number of design changes in progress. Another useful tool could be to apply Overall Equipment Effectiveness (OEE) metrics to track team performance such as engineer working time, design outputs and design issues.
Application of these 5 LEAN Manufacturing Techniques for Medical Device NPI will help ease your medical device NPI transfers and generate value. Feel free to inquire for more information as well as discuss how these tips can be implemented for your medical device NPI.
Alexander Gunson is a Manufacturing Engineer at StarFish Medical with 6 years of experience in the electronics manufacturing industry. He works on NPI transfers and sustaining activities to help drive down costs and improve product efficiencies.