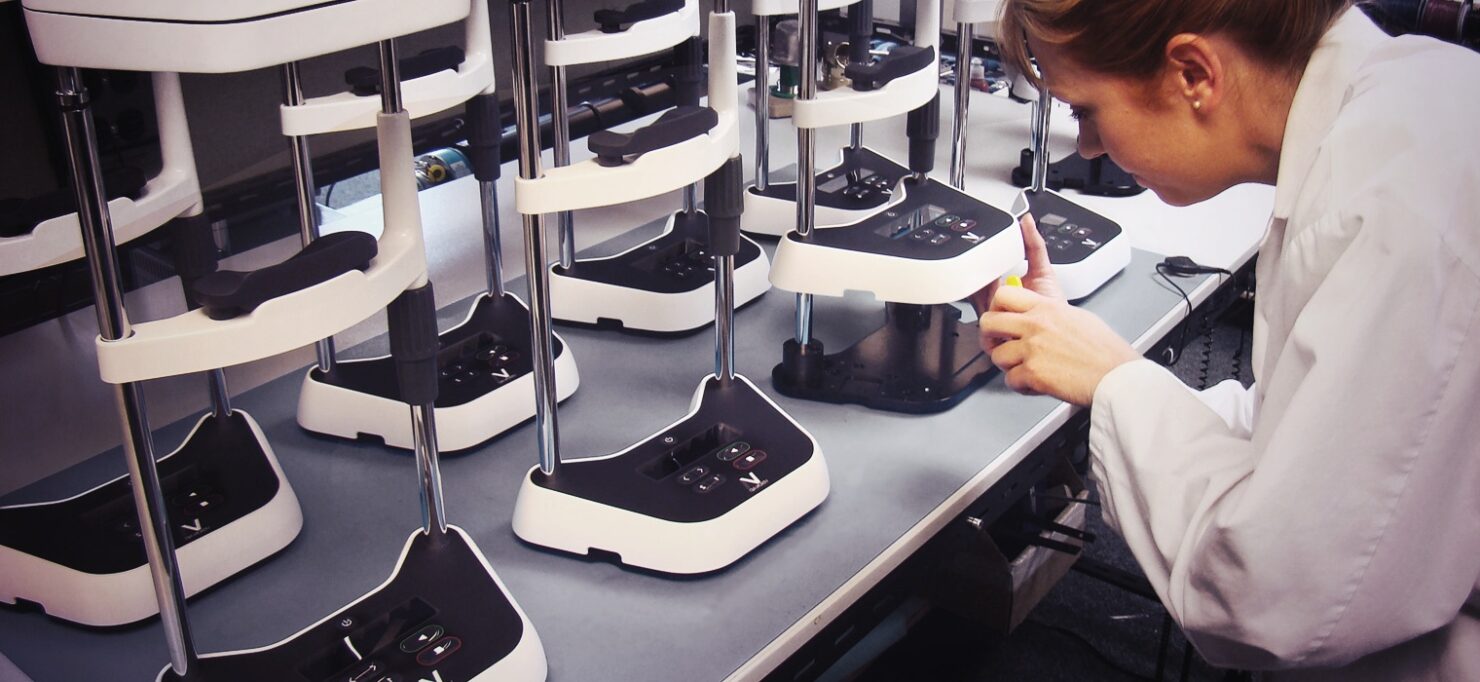
Is Your Medical Device Ready for Manufacturing?
Once in a while cutting corners can add huge costs. In one memorable case, an electro-mechanical device was transferred to us for manufacture with a number of design for manufacturing elements unverified. Not surprisingly, there were field issues.
For example, the coatings hadn’t been tested in the use environment sufficiently and did not hold up. Plastic fibres were embrittled by outgassing of custom extruded tubes and failed. There was even a major strength feature in a welded assembly which was not documented which later failed in use.
We had to provide service technicians on an emergency basis to do field refits all over the world. The repair and design costs were easily ten times what it would have been to do better verification testing up front and resolve the issues. Their reputation cost was much larger.
Every startup medical device company is challenged with how to allocate its limited cash. Cutting out the development of the beta prototype and doing thorough verification often look like convenient budget items to axe. After all, the alpha prototype often looks so good. It’s so tempting to push it into manufacturing.
In truth, the alpha prototyping stage is where the major R&D risk items are proved out. It’s too early to do detailed optimizing for manufacturing at that stage. Beta is the right time to get manufacturability issues resolved at a deep level. Getting your manufacturing and supply chain teams involved at that time will save you a lot of money and risk later on.
Some key questions to keep in mind to help identify what is still required before transferring a device to Manufacturing:
- Can your manufacturing process hold acceptable tolerances to seal reliably?
- How will you know if a critical part is misaligned?
- How much operator skill will be required?
- When a unit goes down in the field can it be diagnosed remotely?
- Can all electronic and visual test points be accessed at appropriate points in the assembly sequence?
- Can critical tolerances and functional elements be easily measured?
- Are there appearance elements which will be expensive to produce reliably?
- What is the risk that an expensive tool will have to be reworked?
- Are there new and high risk vendors involved?
Medical Device Ready Manufacturing Conclusion
Moving through a transfer too quickly without sufficient Manufacturing input could lead to costly engineering changes, rework, warranty and product recalls. On the other hand, moving too slowly could cause undesired and unacceptable product launch delays. Making sure your well planned Product Development Process includes early Manufacturing input will help lead to a smooth Manufacturing transfer.
Jason Dolynny is a former StarFish Medical Director of Manufacturing. Jason was responsible for our New Product Introduction and manufacturing operations including service, inventory and supply chain management.
Images: StarFish Medical