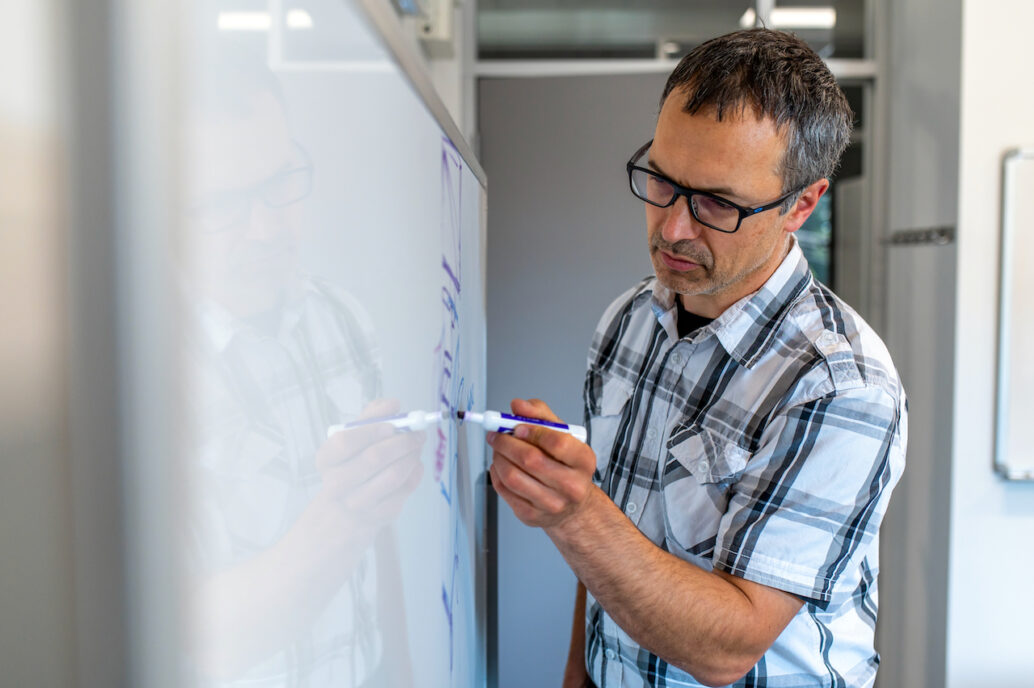
Medical Device Commercialization Resolutions for 2023
Have you made your medical device commercialization resolutions for 2023? We polled our quality, regulatory, project management, manufacturing, and engineering experts for their New Year resolutions. De-risking early, communicating often, testing, and managing pivots were top themes for 2023.
Read their medical device commercialization resolutions below:
Pay more attention to early de-risking and exploring uncertainty and technical in developing a medical device. Really focus on prototypes and experimentation that tackle the big risks first. Try not to add extra fluff that may eventually be required but will likely delay getting resolution on the big risks.
We are successful when a smaller team works on the hard problems, and then bring more people on to make a product. Every project is slightly different, but they all have a lot of commonalities. Take the thing that you’ve de-risked and then turn it into a product.
Have a clear business strategy on how to get to market. Part of that is a regulation strategy. Regulatory landscape monitoring is crucial to understand which markets are going to be easy or difficult to enter and what’s changing in those markets from a regulatory perspective, Just before Christmas, the EU announced some possible significant changes to implementation dates of the MDR, We are all waiting with bated breath to see how that plays out.
Plan for an iterative approach early. Always plan for multiple iterations. This means planning for some success in every iteration, but also planning for some failure in some iterations. Add iterations into the schedule to leave space to re-spin things that don’t quite work out as expected.
Spot pivots in fundamental requirements earlier on, like the intended user or the intended use. That’s super common because as we learn more about the clinical need, the technology and what’s possible, we sometimes must scramble up our lofty original goals and figure out a new way to make a business successful. Always pay attention to the changing landscape sooner than later to end up somewhere successful.
Apply product management in addition to project management. A device may originally be designed for surgeons, but after iteration and development it is no longer intended for surgeons. Instead, some other entity is going to use it. The business case is technically modified and needs product management validation so that ultimate success is ensured.
Consider simulation for failure modes, design questions and pre physical tests. You can use a simulation for analysis of a broad range of things. There are huge time savings. Physical testing requires a longer timeline to build and break things. Many of the 60601 tests, even formal or confidence tests, can be simulated ahead of time with CAD and material details to expedite changes that harden design before informal and formal testing.
Create a repository of previous projects to speed testing. Leveraging previous work makes your process more efficient. Be proactive and think beyond the immediate goal that you’re working on and make it even more powerful by thinking about all the ways that the work could be used elsewhere. You’ll end up with an output that is applicable to more things. Use a bit of strategy when doing work so that it becomes more useful for reference designs that can be reused and applied.
Run a ton of data through core technology development early on to confirm it is doing what you expect and want it to do. Come up with an easy way to test your device early and keep applying that test as you change. Tons of findings don’t really pop out until you try things at scale or with a large amount of data to figure out how it will translate to a manufacturing test. Make your core technology more viable with verification and validation. Have a standard way of retesting the device through all stages of development, monitoring, and manufacturing.
Be a user-centric designer. Historically when initially approaching a problem, one tends to engineer functionality and that can be unattractive or too complex, A device should be like simple enough that the user can easily operate it in the field.
Listen to and understand the real need. Don’t jump to a conclusion based upon building toward a final device. There may be investor criteria, milestones or timelines that are a higher priority. Truly understand the project need and adapt development to that situation.
Encourage and maintain effective communication and collaboration with all stakeholders to allow for quick adjustments to the project plan as needed to meet changing needs and circumstances. I plan to do this by having regularly scheduled check-ins, leveraging collaboration tools, and using active listening skills.
Involve manufacturing and supply chain early. They can tend to be an afterthought. There are a lot of deviations on the fly currently because parts aren’t available. You may not be able to execute a design you love because the parts aren’t available now. Start thinking of manufacturing and supply chain quite a bit earlier than pre-Covid days.
Inform everybody in the manufacturing supply chain project management upstream and downstream of design changes that may impact the BOM. With small builds, taking on stock and then making a BOM change, means getting stuck with unneeded stock or sending it back.
As you design, especially prototypes that are nearer to products as opposed to proof of concepts, think about design for manufacture. Consider both capabilities and subcontractors or suppliers that will be engaged along the way.
Really understand each other’s issues and build a collaborative approach. Put some of the emphasis that we see engineering put into testing and system testing for Pro builds into a prebuild. In the automotive world, we would do a paper build. Manufacturing and engineering teams build the product in our minds and walk through every stage asking, “Do we have everything we need?”. A lot of stuff can be flushed out, almost like doing a trial run.
Create more opportunities for cultural growth at StarFish and beyond by creating safe, experiential spaces, both communal and personal, for people to be able to do their best work ever.
A Closing Thought
Every year on January 1 my family gets together and we come up with a family theme for the year instead of a resolution. Last year’s theme was “Hard work will make dreams come true”, this year’s theme is “Finish what you Start”. In my work life, I am excited to work with my clients and colleagues to enable the successful completion of a number of exciting projects we are working on!
You’ve read our choices, now we’d enjoy hearing your medical device commercialization resolutions for 2023.
Astero StarFish is the attributed author of StarFish Medical team blogs. We value teamwork and collaborate on all of our medical device development projects.
Images: StarFish Medical