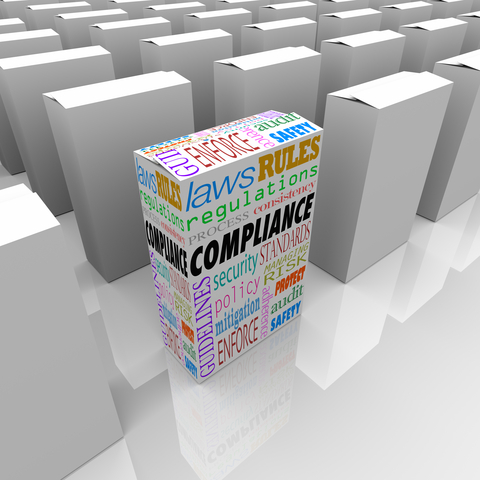
Use standard methods innovatively to secure regulatory approval for medical devices
A project manager’s tale of thinking creatively inside the box
In the highly regulated field (as it should be) of medical device design and manufacture, sometimes the best way to secure regulatory approval needs more than thinking outside the box. It requires the project manager to build a different box.
In the mid 2000’s I was a project manager for a Contract Research Organization (CRO) specializing in evaluating anti-microbial products and medical devices. I was routinely approached by medical device manufacturers seeking 510(k) clearance for catheters with a broad anti-microbial claim.
Straightforward enough, however these claims were complicated by the fact that the manufacturers were seeking anti-adherence claims (meaning that the proposed device prevented adherence of the microorganisms to the catheter). This is complicated in that (at the time) there was no standard test method or ISO standard to follow. This posed a significant problem for the FDA reviewers in that there was no validated method with which to support the claim.
To be fair, since the pioneering work of the late Bill Costerton, there were a good number of publications specifying test methods and protocols with which to evaluate biofilm formation and the prevention of it forming on any number of surfaces. The trouble with this approach is that, the methods varied widely in complexity, end-point, and reproducibility (affectionately referred to as the three pillars of non-viability in the regulatory community).
Without a standard method or gold standard with which to support the claim, the reviewers were required to painstakingly sift through reams of supporting documentation and various versions of specific laboratory developed test methods to support the data. Most of the data package was geared towards proving the test method, rather than the more important data supporting the label claim. As one can imagine, this often led to long delays in the review process, increased cost to the sponsor, and further burdened an already complex process.
In the absence of a standard method, I became creative in my process going to such lengths as developing complex animal models to support our in vitro bench data and publishing supporting data in peer reviewed journals. I even hosted workshops where the FDA and competing product developers were invited to review and participate in performing the test methods we were proposing in order to demonstrate the accuracy and validity of our lab test methods!
I continued like Sisyphus for many years until a fortuitous collaboration with the Center for Biofilm Engineering led to the submission of our anti-biofilm test method to the American Society of the International Association for Testing and Materials (or ASTM) for development into a standard test method: ASTM E2799-11, which is now used around the world to support claims of this nature.
The point of my story is not to encourage CROs or project managers to curtail the development of novel test methods and experimental systems. So called ‘out of the box’ thinking is routinely required to appropriately evaluate the claims of novel medical devices. The point is that, in the highly regulated field (as it should be) of medical device design and manufacture, sometimes the best way to think outside the box is to build a different box.
Nick Allan is the StarFish Medical Bio Services Manager. He applies creative thinking and innovation to medical device projects ranging from product definition through sustaining engineering.
Image: 38361468 © Iqoncept / Dreamstime.com