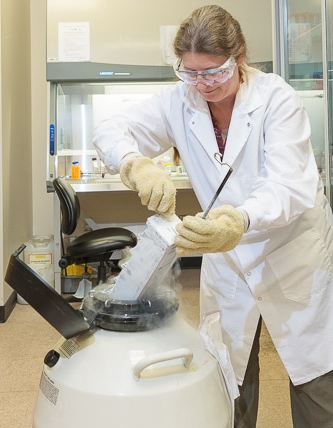
Consider these 3 areas carefully when testing medical devices in a Biolab
Keep your project on time, within budget
Testing medical devices in a Biolab often requires changing locations from an engineering lab to a Biosecurity Level 2 (BSL2) BioLab that can facilitate specialized tests involving potentially dangerous microorganisms, tissues and biological fluids. Careful pre-planning is required for timely experiments to take place in BSL2 BioLabs. Poorly designed devices or tests can delay obtaining critical results, and create unnecessarily large bills.
The BioLab and its equipment may be contained within a third party contract research organization (CRO). Resources are often shared with numerous clientele, and the space may lack standard equipment that engineers rely on (i.e. oscilloscopes). Additionally, BioLab staff may not be engineers.
To help make the transition smoother, I have summarized three areas for top consideration when planning a move to the BioLab.
- Physical Considerations
The following questions help verify that the BioLab meets appropriate physical requirements prior to the arrival of your device and test protocol.
- What are the electrical requirements needed to run your device?
- Is there access to sufficient electrical outlets?
- Will your device fit into the required specialized equipment?
- Will you be able to access all key parts of your device during testing?
- Will you need special light or dark environments?
- Are your required temperature and humidity conditions present?
- Will you need stationary or moving platforms?
- Will you need an internet connection?
- What engineering equipment required for your device set up or testing is not in the BioLab?
- Can your device be decontaminated?
- If so, how?
- Will any physical conditions interfere with your device or the tests to be performed?
The following is a list of helpful items that you may need to bring with you:
- Pliers, screwdrivers, wire cutters, allen keys and other general tools
- Extension cords, electrical tape, Teflon tape, painter’s tape
- Lighting, supports
- Temperature tracking devices
- Syringe pumps, pressure gauges
- Photography and recording equipment
I highly recommend that you perform a mock set up of your device and test protocol while you are still at the engineering lab. This process will help tailor the above list, and increase the efficiency and effectiveness of any assays performed.
- Safety considerations
Situations that are non-hazardous in an engineering lab may become hazardous in the presence of dangerous microorganisms. This series of questions help ensure that the safety requirements are investigated prior to testing medical devices in a Biolab:
- Are there puncture hazards such as pointed parts, sharp edges, moving components, needles or blades?
- What modifications or precautions can be used to lower the hazard?
- Can the device pose an electrical shock hazard?
- Will your device be functioning near water?
- Is there a risk of injury from electrical parts during testing or sanitizing?
- Are there any precautions that must be taken if your device contains batteries?
- Does testing generate aerosols?
- What is the nature of these aerosols (i.e. biological, chemical or both)?
- Are there ways of containing the aerosols and/or minimizing their generation or dispersal?
- Does your device testing generate excessive sound levels that may require hearing protection?
- Is your device handled under high pressure or high vacuum conditions?
- Are safety measures in place to prevent injury or equipment damage?
- What disinfection agents are compatible with your device or its important components?
- Are the correct waste containers in-house for disposing of your devices and test materials?
- Are chemicals involved in the testing?
- What are their hazards?
- Is the BioLab staff familiar with the relevant safety data sheets?
- Are the chemicals compatible with the disinfection protocols and chemicals being used?
- Have instructions for disassembling your device for disinfection been provided to the BioLab staff?
- Have the BioLab staff been trained on the safe handling of your device?
- Human Factors Considerations
The BioLab can be a challenging work environment. Lab coats, safety glasses or goggles and gloves can result in difficulties when performing dexterous activities, and overheating when working in warm conditions.
Handling any device that will be in contact with either microbial cultures or biological samples/fluids requires technicians to:
- Frequently change gloves
- Sometime wear double layers of gloves
- Immediately clean up any drips, spills, leaks
- Continuously sanitize equipment and work spaces
- Undergo pre-testing setup
- Undergo post-testing take down, disinfection, wash up and sterility verification
An uncomfortable testing environment is much more likely to contribute to mistakes or accidents. Ask the following questions in order to make working in the BioLab more pleasant:
- What footwear and personal protective equipment will the technician need to wear?
- What temperature is the room that the testing will take place in?
- Is the technician dressed to work in an overly warm or cold environment?
- Is there time during testing for the technician to take breaks and rehydrate?
- Can your device, and critical parts be accessed and manipulated comfortably during testing?
- Do space constraints cause risks of physical strain?
- Does testing require repetitive motions or holding the body in a static position for long time periods?
- Can a better way of accessing the device be engineered to prevent strain?
- If a heavy or clumsy device must be continuously moved, are there ways minimize the physical exertion required?
- Is there sufficient lighting to perform the required tasks?
- Can the technician manipulate and take apart your device while wearing the appropriate personal protective equipment?
- Can your device design include larger parts (e.g. nuts, bolts, Allen keys) that are less difficult to handle?
- Has the additional handling time required for setup, cleanup, and continuous sanitizing been factored into your device test plan?
- Can testing and cleanup be performed in a regular work day, or are extra resources required to make the work load manageable?
In addition to addressing these many considerations, another important step is to talk with the BioLab staff. They are highly trained and knowledgeable in their work space, equipment, and safety protocols. They can provide critical feedback on device design, implementation, safety and timing within their specialized environment.
Although it may seem like a daunting task, testing medical devices in a Biolab does not have to be overwhelming. Pro-active planning will facilitate a seamless transition while keeping you on time, within budget and free of unpleasant surprises.
Sue Bantroch is a Biomedical Engineering Technician at StarFish Medical. She works on a variety of biotech medical projects splitting her time fluidly between our main facility and our BSL2 facilities at the University of Victoria.
Images: StarFish Medical