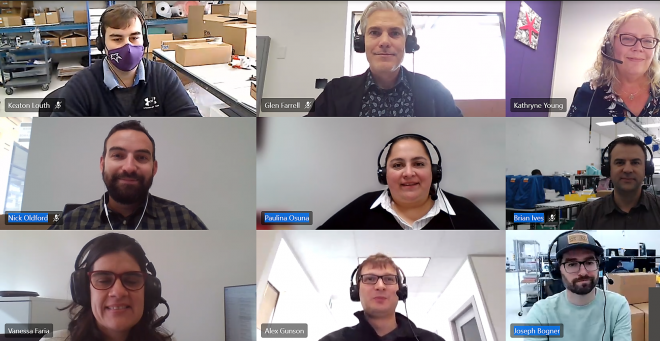
Manufacturing safety and efficiency during COVID-19
Our manufacturing leaders recently convened on Zoom to identify changes we’ve made for manufacturing safety and efficiency during COVID-19 and offer tips for delivering a healthy, productive manufacturing operation.
Director of Manufacturing Kathy Young prefaced the discussion, “In manufacturing, we need people in the office and on the manufacturing floor to continue our work. Since COVID-19, we’ve had a mix of people who work in the office, work remotely, or a combination of remote and on site. Our manufacturing floor has risen to the challenge to ensure that we’re keeping our work place healthy and safe.”
Use online tools: After safety, the biggest thing to consider when working remotely is efficiency and effectiveness. We used to have in-person check-ins for impromptu and standard manufacturing meetings. Now, Zoom, Microsoft Teams, and collaborative environments for documentation are great additions to normal email communication.
Don’t forget human collaboration and teamwork: We have a team on site and another that is supporting them remotely (purchasing, for example) as a result of social distancing requirements and space restrictions. Collaboration and patience are invaluable. When manufacturing employees are working remotely, they still have very quick, easy contact with the onsite team. For example, purchasing may need to ask an on-site colleague to check a received part for mistakes because they are not physically present.
Don’t assume everyone will see messages at the same frequency. As a company, we’ve gotten better at keeping in contact with everybody and found new ways to always have an open line of communication to keep the business moving forward. One thing to remember when using online tools for communication is the manufacturing floor might check computers less frequently than non-manufacturing employees.
Upgrade tools on the floor: With remote staff, it is helpful to have a good data assessor onsite or high quality images to share and quickly diagnose issues to move things along. A new microscopic device for inspecting PCBAs helps us obtain higher resolution images. Sharing them virtually when there are issues or questions around PCBAs has made inspection easier.
Daily Huddles are important: Our huddles have become more effective. Each morning everyone knows who’s going to be on site and the daily tasks of onsite team members. Even when we’re on site, we participate in huddles virtually to keep each other safe.
E-signatures are a powerful tool: Before we release equipment, we must complete a QA sign-off form. COVID forced us to do everything electronically, which sped up the process around releasing equipment or products in manufacturing. We now use email releases with signatures signed electronically by the team in a way that protects everybody.
E-signatures are not just for releasing product, but also for maintaining our QMS system. We update our work instructions and standard operating procedures remotely.
Prior to COVID we used a hybrid system in manufacturing. We adapted our paperwork into an electronic process as quickly as possible. That drove a bigger focus throughout the entire company to use online systems for signatures and reviews in order to avoid in-person contact. This work will remain beyond COVID. It is much more efficient than running around trying to get physical signatures.
Phones are still important: Have a call list of everyone’s phone numbers so you can contact them easily. We shared staff phone numbers internally and with key external contacts. “I don’t mind even though it means getting phone calls at any hour of the day. It’s very meaningful to keep business going.”
Virtual phones allow people to phone your office number and, if you’re not in the office, the call shows up on your computer. This is really handy. Email voice messages from your office phone are really helpful for keeping in contact with callers trying to reach you.
Increase lead times and convert to a contactless delivery system: COVID has increased lead times on all of our incoming deliveries. We prepared for longer transit times, and for a while we cleaned packages when they were coming in. We now use a contactless delivery system.
Plan ahead for shipments and deliveries: COVID affected a lot of our suppliers, their capacity and their lead times. Logistics throughout the Supply Chain take longer because of COVID. What used to take two weeks, now takes three or four weeks. Internal and external logistic teams now plan shipments farther out in advance and notify the shipper and the receiver so we can track goods all of the way.
The way we plan materials and execute purchasing is more adaptable and flexible. New resources and tighter management of inbound materials helps us keep our schedule. A review of the manufacturing lead time for raw material identifies high risk materials. We bring them in earlier than needed to ensure on time deliveries for our clients.
Make deliveries safer: Add a sign-in sheet and a temperature taker at the manufacturing door. Initially we asked suppliers to drop goods off outside the building. Now they can deliver up to a specified point in the building. We keep track of who is coming and going in the building beyond dropping off shipments. Visitors sign declarations that they are free from symptoms, and we take their temperature if they enter the building. Our health and safety team define and implement the program. It benefits manufacturing the most because we have the highest number of external contacts coming into the building.
Adjust daily routines and environment: Beyond cleaning, social distancing, and having Zoom meetings instead of in-person gatherings, day to day activities are not that different than before COVID. Manufacturing personnel still come to the office, we still do our work, and everything that we were doing before the pandemic. A few minor changes like staggered break times and barriers in the lunch room, provide employees a safe place to eat their lunch while work and materials go on around them.
We have been busier than ever this year, despite the challenges of COVID-19. Our experiences and tips for manufacturing safety and efficiency during COVID-19 are offered to help others keep a safe and productive work place. These tips from PWC offer additional issues and ideas. Please share your tips and suggestions with our readers.
Astero StarFish is the attributed author of StarFish Medical team blogs. We value teamwork and collaborate on all of our medical device development projects.
Read how StarFish Medical led a consortium that created a Ventilator 2.0 therapy device in record time.