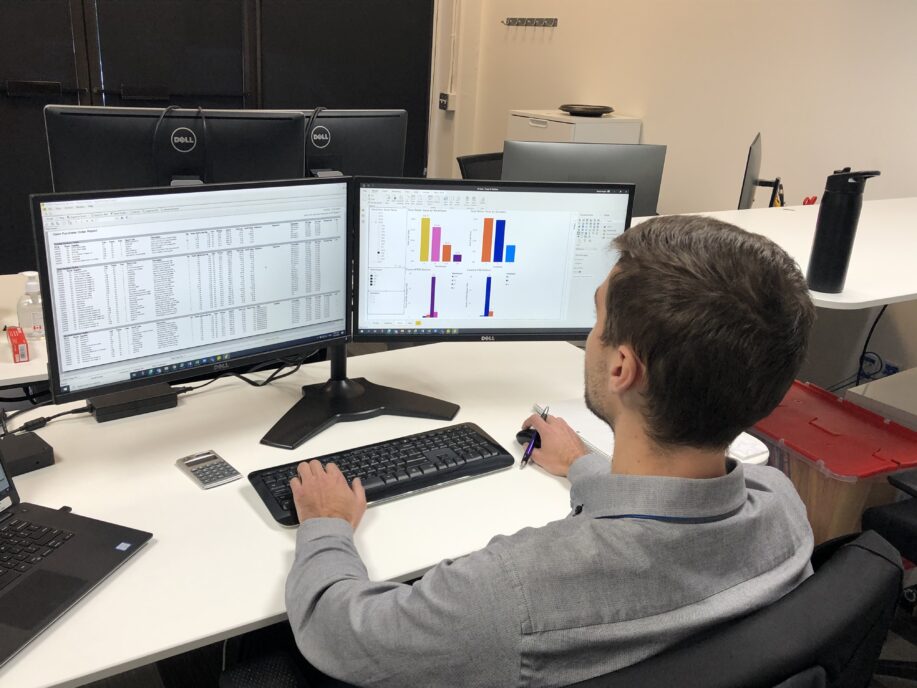
Supply Chain Reports that keep your eye on the ball
Having overcome the challenges of transferring a product design into manufacturing, it is time to enter a new process cycle. At this stage, Supply Chain Reports are essential to assess and monitor costs, processing and material flow.
Supply Chain Reports can be a great source of data, providing insight into how processes are going, and enabling decision makers to find the right way to increase operational efficiency while remaining competitive.
Here are useful reports to keep Supply Chain links connected.
Purchasing:
Open order: This report provides information about orders during the fulfillment cycle. It is grouped mainly by supplier, purchase order number, part number, quantity, costs and estimated arrival date. This offers a quick and easy way to track order status and financial exposure.
PPV Analysis: Purchase price variance (PPV) is used to show the difference between estimated and actual costs. Keeping a regular report for PPV is an important tool to avoid any surprises. It raises a flag when a material price has changed from plan, and also that all finished goods which include the material will have a variance in the gross margin when sold.
Supplier Scorecard: The scorecard monitors key performance indicators, such as on-time delivery, quality performance, reliability, and average lead-time across multiple suppliers. They can be used to analyze current status and trends compared to previous periods. They can also identify strategic suppliers, optimize suppliers across materials, and help negotiate better payment terms.
Quality:
First time Yield: First Time Yield is the number of good units divided by the number of total units going into process. By understanding the percent of defect-free units produced, it is possible to identify bottlenecks, reduce rework and improve production efficiency.
Non Conformance Records: A non-conformance report addresses specification deviation or work that fails to meet quality standards. The report is used as part of quality control processes to detail the root cause of a deviation, how it occurred and how to prevent it from happening again.
Scrap: This report includes detailed scrap information, such as reason, quantity and dollar amount.
SCAR: Use a Supplier Corrective Action (SCAR) to investigate the non-conformance with the supplier process. By documenting serious issues on a SCAR report, suppliers can conduct root cause assessment and corrective actions to address the situation.
RMA: A Return Merchandise Authorization (RMA) is an authorization from the manufacturer for their customer to return products that do not meet required specifications. The report helps identify non-conformances, prevent recalls and identify areas for improving the production process.
Inventory:
Current Inventory Valuation: An inventory valuation is the monetary amount associated with the goods in the inventory. It is based on the costs incurred to acquire the inventory. The valuation can be segregated by Raw Material Inventory (RMI), Work in Progress (WIP) and Finished Goods (FGI).
Material Management Report: Use this report to manage inventory at optimal levels by identifying usage and coverage trends. This visibility helps reduce excessive or unnecessary carrying costs and inventory write-downs, enabling organizations to free up working capital and boost profitability.
Inventory Forecasting: This report facilitates determination of optimal future inventory levels based on sales projections. It can include time intervals that continue through to the project end.
Excess and Obsolete: Data from these reports expose the quantity and dollar amount of obsolete material. Quick access to these numbers speeds work on a solution to reduce or remove the problem through actions including promotion, write off, or sale of outdated inventory.
Delivery:
Shipments Actual to Plan and Projected Shipments: This tracking report for all planned, actual and future shipments makes it possible to create an on time delivery metric. It shows the organization’s capability to meet customers’ requested delivery dates.
Distribution Reports: A Distribution Report provides in-depth information for all shipments, like serial number, invoice number, final destination delivery, etc.
Visibility is the key to successful improvement initiatives. These standard reports will help you see what`s happening in the Supply Chain at any given point. The report data can be transformed into metrics that measure Supply Chain performance against key indicators.
Vanessa Del Castillo Faria is a Project Buyer at StarFish Medical. Vanessa has extensive experience working in the electronics industry and in a retail non-profit cooperative. She holds a Master`s degree in Global Management.
Images: StarFish Medical