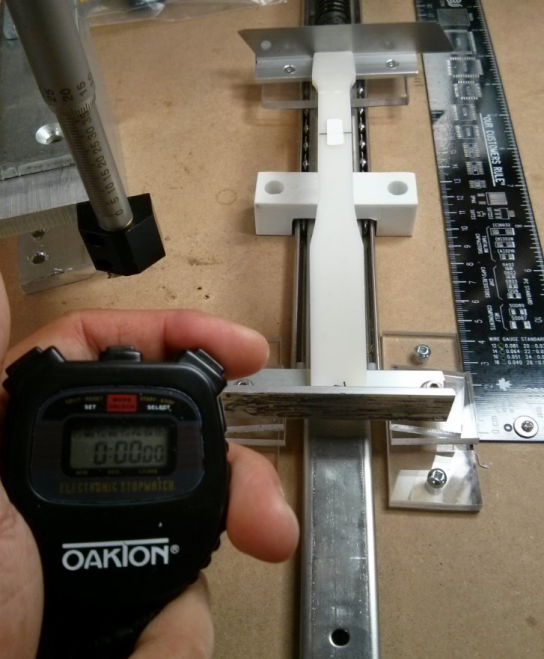
Quickly Verify Environmental Stress Cracking (ESC)
The ability to quickly verify Environmental stress cracking (ESC) is important because it is one of the most common failure mechanisms in parts made of polymeric materials. Proper selection of polymers is crucial to the successful design, production and longevity of any product, but it is particularly vital to the purpose and usage of medical devices. In addition to standard mechanical and thermal properties, sensitivity to environmental stress cracking should be a major consideration, especially when dealing with polycarbonate.
ESC is the result of a chemical reaction between a chemical agent present in the environment and the material from which the part is made. It is dramatically accelerated by the presence of residual stresses in the part, and may lead to failure of the part due to crack propagation. These residual stresses are a result of the processing and thermal history of the part (molded in stress).
These stresses can result from a combination of part design and processing quality, and can be important in applications where the part will be subjected to continuous stress over a long period of time.
For example, combining polycarbonate material, residual stresses, and machine oil in self-tapping screws or inserts would almost certainly create cracks in plastic parts.
The chemical agent does not cause a direct chemical attack or molecular degradation. Instead, the chemical penetrates into the molecular structure and interferes with the intermolecular forces binding the polymer chains, leading to accelerated molecular disentanglement.
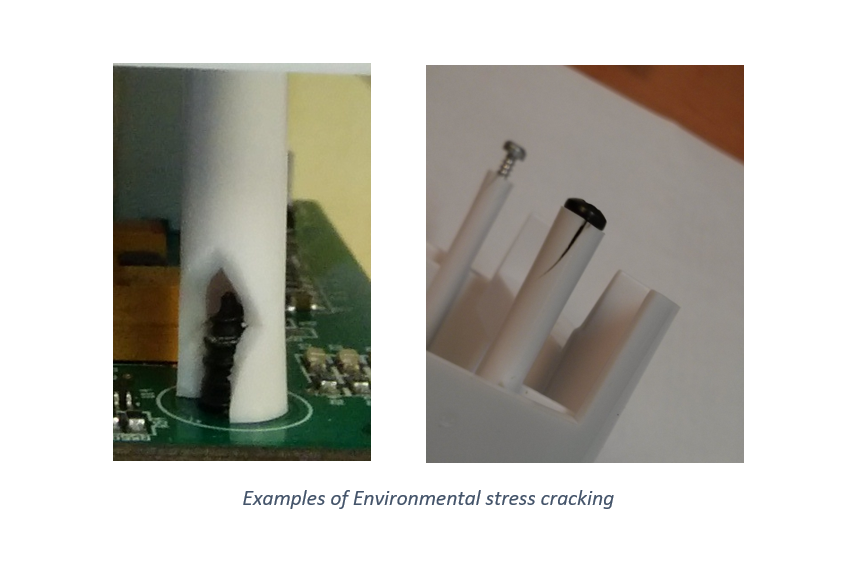
The effects of ESC are not detectable during product assembly because the cracking process takes a long time to develop. The first crack can appear long after device is in the field, sometimes as long as six months to a year after production.
During material selection, it is wise to engage material vendors early. Most polymer manufacturers have testing data and may provide suggestions for the selection of an adequate material with respect to design requirements.
In cases where cracks do appear, experimental methods can be used to confirm ESC as a root cause. The procedure summarized below is one such method that evaluates residual part stress vs. a material characteristic “critical” stress.
Testing
ISO 22088 describes various testing methods which are designed to find a material’s critical stress (the stress under which ESC will not occur) when exposed to a given chemical environment. This enables one to quantitatively evaluate the residual stresses present within a part, and – by applying the appropriate mitigations – minimize the risk of failure in this mode during its service life.
This is essentially a ranking test and is not intended to provide data used for design or performance prediction.
Step 1: Anneal “dog-bone” material samples and then allow them to sit (condition) under standard ambient laboratory conditions. This removes any residual stress in the material. In this example, the material is Polycarbonate, annealing was carried out at a temperature of 65° Celsius for approximately 30 minutes (see Figure 1), and then the samples conditioned for a minimum of 40 hours prior to testing.
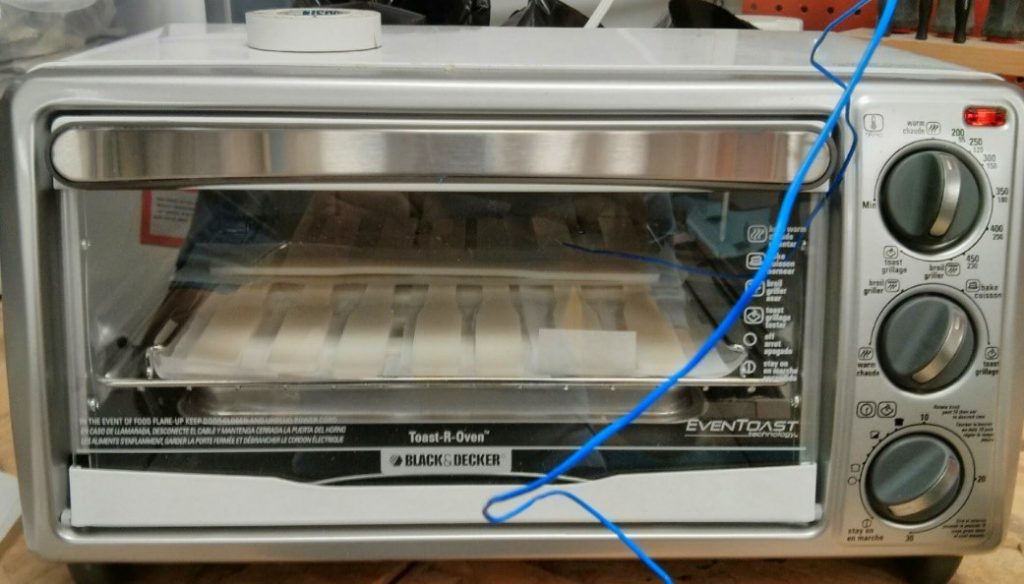
Step 2: Install the material samples into a variable span mount (see Figure 2); this applies a known, constant stress to the part. To calculate the stress (σc): record the free length of the sample (L0), the span between the supports (L), and the resulting deflection at the middle of the sample (h) (see Figure 3). The applied stress can then be calculated as:
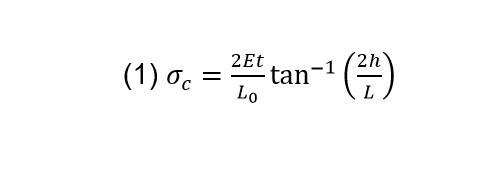
Where t is the material thickness, E is the material’s Young’s modulus in Mpa.
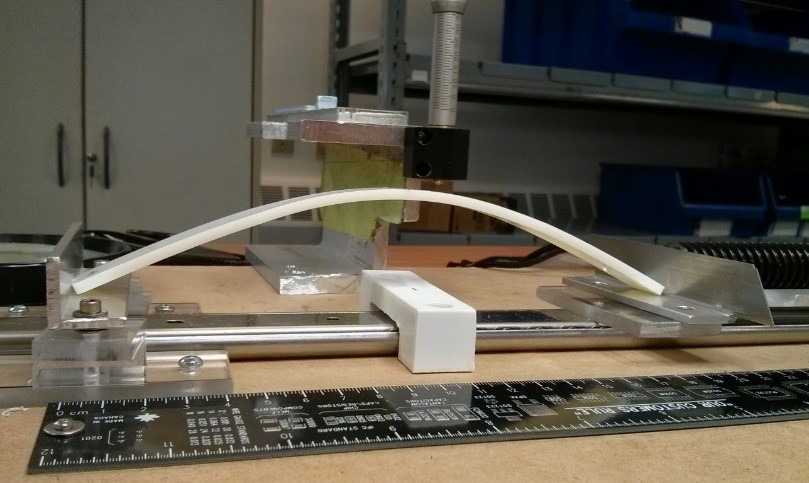
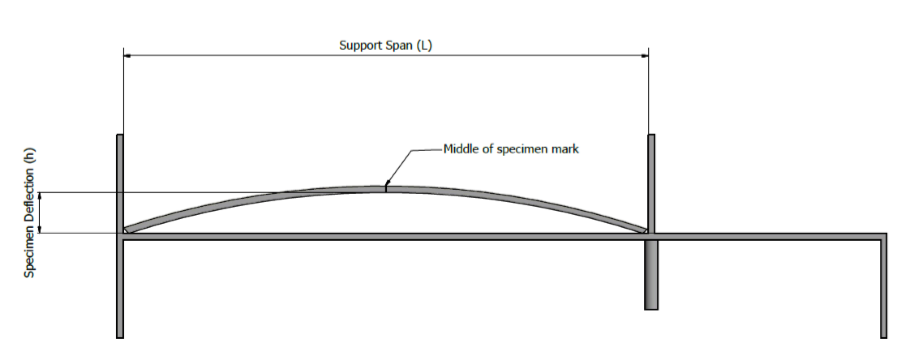
Step 3: Place a strip of laboratory filter paper over the middle mark of the sample. Apply an accelerating compound over the filter paper (In this example: Esso Premium Gasoline was used as gasoline accelerates ESC in Polycarbonates) and record the time required for cracks in the surface to appear (See Figure 4 and Figure 5). Repeat for multiple stress levels.
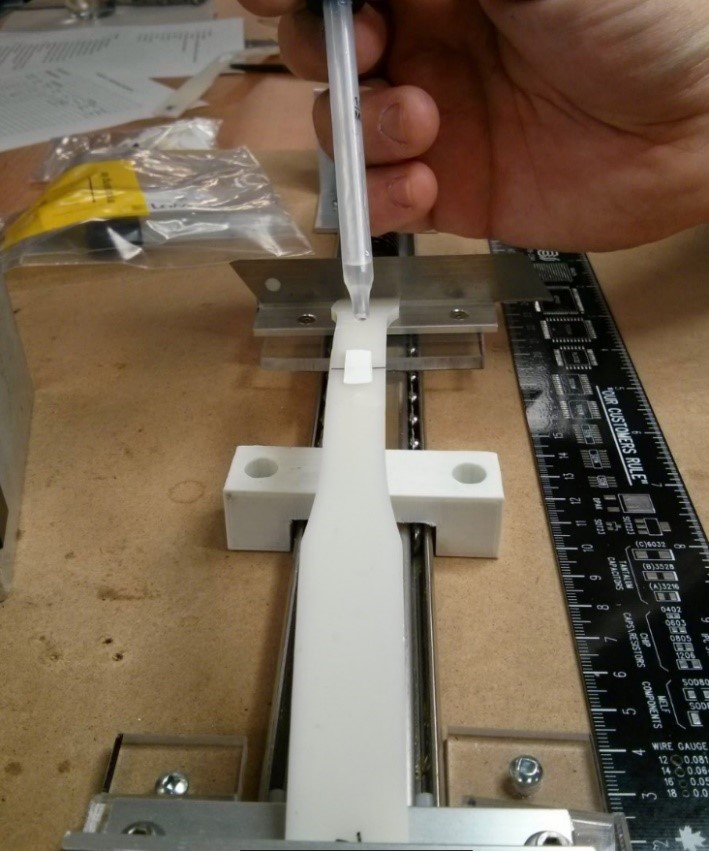
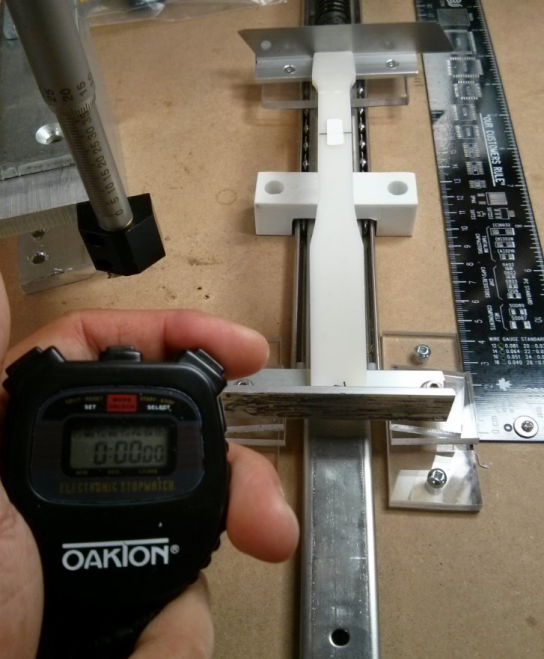
Step 4: Plot the applied stress vs. time for cracks to appear. Based on the trend shown, it was determined that the critical stress of Polycarbonate when exposed to gasoline was 7.5±1.0 MPa. In order to ensure that failure did not occur in our polycarbonate part verification that the residual stress level within the part was less than 7.5MPa was required.
The same chemical agent (gasoline) could be applied on the designed part, and the time until cracking observed (measured). If the time until first crack appearance is less than 50 seconds, the residual stress is higher than critical stress.
Time of cracking vs applied stress
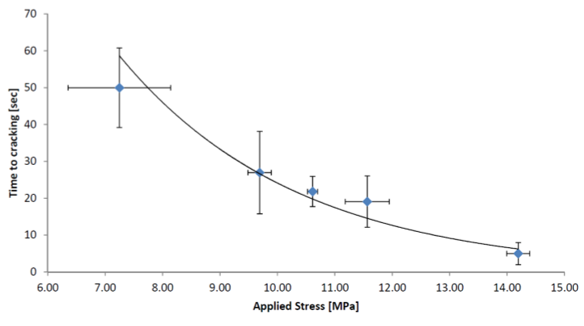
Conclusion
It is crucial to start the polymer selection process early on in the product design & development process, working closely not just with the injection molding vendor, but also with the polymer manufacturer. In particular, understanding and mitigating ESC can be important. The example test above to verify environmental stress cracking (ESC) doesn’t require any specialized or expensive equipment, but can generate valuable data to greatly inform decisions on thermoplastic or guide design choices, and evaluate residual stresses in the presence of accelerants.
Rade Gadzic is a senior mechanical engineer. This is his first blog. Rade’s patents include a Magnetic Homogenizer Apparatus.
Images: StarFish Medical