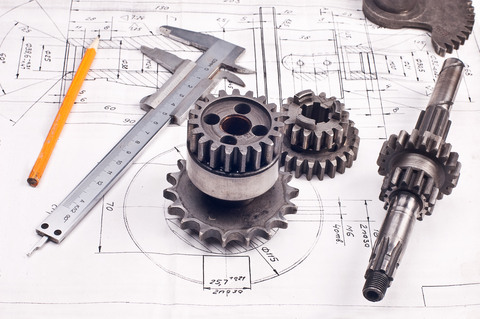
When Tolerance Studies Add Value in Medical Device Development
Coming from a high volume and high precision electronics manufacturing background, I lived in a world where every design required a tolerance study. Entering the low volume world of biomedical entrepreneurship, I’ve been surprised by clients telling me that tolerance studies are too expensive and that they are happy to proceed without them. This led me to consider when a tolerance study actually adds value to a medical device design.
Balancing Costs
Tolerance studies are not always a big scary job. Even a quick look at the fit between two parts can save thousands in non-conformances, production delays, and supplier issues. That being said, not all parts and assemblies have issues. Checking every part would add unnecessary costs to the project. The trick is balancing these costs throughout a product’s life to maximize its earnings.
Early Prototyping and Alpha Build Phases
During early prototyping and alpha build phases, designs are usually too fluid to warrant an in-depth tolerance analysis. Rapid prototyping and quick rework can compensate for any unforeseen part variations allowing the project to continue moving forward. Unless a specific tolerance output is known and required as part of the design functionality, a tolerance study would not add value at this stage. The exception of course would be in support of verification testing.
Verification Testing
Most verification testing focuses on confidence intervals but they typically only provide the range of values that are likely to contain the mean value. In some cases, a tolerance interval, which provides the range of values that likely contain X% of all values, is required to confirm that the test passes. The problem is tolerance intervals are much harder to calculate and require dedicated statistical software.
Tolerance studies, using the root sum square method, can be used as an alternative to calculate the theoretical distributions beforehand. When combined with the mean confidence interval, they can provide a Process Capability Index (CpK) which will provide a more in-depth understanding of the design capabilities.
Beta Phase
The beta phase focuses on maturing a design for manufacturing, so this is the prime opportunity to apply design for manufacturing principals including tolerance studies. The first step is to identify the critical design features that may require investigation. In high volume production there are large amounts of data to help identify critical features and processes, but during alpha builds the data can be very limited. Therefore, extra care should be taken to document findings during the alpha build to identify action items for the beta design updates. In particular, any parts that had to be modified or screened for fitment / functionality should be investigated.
Compliance
It’s easy to assume that in order to achieve precision all parts must have tight tolerances. The truth is, compliance can also be used to achieve precision. Tolerance studies rely on a closed vector loop of interacting parts to calculate total variation. These loops can be elongated or simplified through the choice of design features. Datums, biasing, or fiducial features are great ways to reduce the number of tolerances while achieving the required precision.
For example, consider the fitment between two acutely angled parts (∠) where they mate at the inner angle and have a screws locking their position through the bottom surface. The standard loop of controlling each tolerance step would result in a total of eight stacked tolerances. This method would result in a high risk for fitment issues unless all dimensions were controlled with tighter tolerances, thus increasing the part cost significantly.
Alternatively, allowing one part to comply to the other through use of screw slots would eliminate the need for increased tolerances and ensure that all parts can be assembled together. A tolerance study to calculate the required slot length for the worst case stack would be recommended in this case as the cost savings of adding the slot will more than pay for itself.
Transfer and Manufacturing Production
Finally, during transfer and manufacturing production, tolerance studies can be utilized to help investigate recurring issues for both the physical device and assembly process as well as to identify cost saving opportunities.
On the device level, a tolerance study will help to reveal if the issue originated from the design or from the supplier. This information is critical when determining the required corrective action to resolve the issue. For the assembly process, a tolerance study can help to identify the expected yields allowing for more accurate cost models and production forecasts. Alternatively, tolerance studies can be used to re-evaluate drawing tolerances to determine which items can be relaxed for part cost reduction
Proactive Thinking
This overview provides just a few examples of how to apply tolerances to add value to bio-medical start-ups. Proactively thinking about tolerance impacts from design features will help build the experience needed to dictate when tolerance studies are required.
Image: 25361162 © Igor Skryagin | Dreamstime.com
Alexander Gunson is a Manufacturing Engineer at StarFish Medical with 6 years of experience in the electronics manufacturing industry. He works on New Product Introduction transfers and sustaining activities to help drive down costs and improve product efficiencies.
Discover Startup & Founder Benefits of Working With StarFish