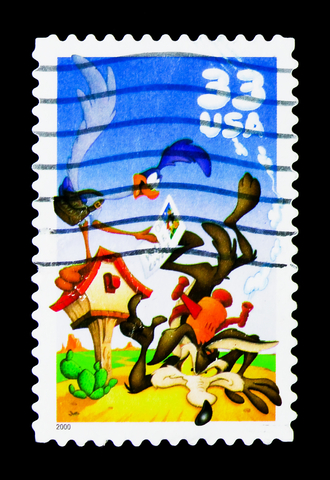
Invisible EMC Testing Problems in Medical Device Design
Like Wile E. Coyote’s persistent attempts at catching the Roadrunner, sometimes it takes multiple attempts to get a product through EMC testing due to invisible EMC testing problems. Why? And what can we do to increase the likelihood of passing on the first or second iteration?
To avoid having devices behave as unpredictably as those from Acme Products Inc., one designs them to meet a specified level of Electromagnetic Compatibility (EMC). A product meeting EMC standards will exhibit immunity – the ability to resist external EMI, and will also have low emissions – that is, it will not create its own EMI and interfere with other products.
Possible EMI paths are: conductive (e.g. cables penetrating the device enclosure); radiated (e.g. through plastic enclosures and holes in metal enclosures); and near-field capacitive and inductive (e.g. proximity to large power lines). Another way of looking at EMC Testing Problems and EMC compliance is that interfering signals are prevented from entering or leaving the product.
Experience and training aid an engineer’s efforts at EMC compliance, both in the design and the testing phases. There are hundreds of references on the topic; many introductory treatments are found on semiconductor company websites. Two good examples are Analog Devices’ RFI and Shielding Concepts and National Semiconductor’s Understanding and Eliminating EMI in Microcontroller Applications.
Designing a product to meet EMC requirements is challenging, but we and other successful design companies have processes in place to make this smoother. Design reviews for circuit boards, for example, involve checking for good ground planes, controlled-impedance traces, power supply bypassing, absence of stub traces and minimizing the area of high-current loops.
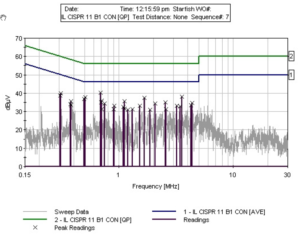
Because you can’t see EMI, you need to measure it with instruments for an objective assessment of the design. A complete EMC test to the IEC-61000 family of standards can take several days or longer, but it is foolish to wait until the product design is complete before performing EMC testing to avoid EMC Testing Problems; deficiencies might be uncovered that require extensive redesign. A better approach is to conduct smaller assessments early in the design cycle to catch problems when they are easier and less expensive to fix. A typical pre-scan will look only at the device’s emissions, since usually a device that fails emissions also has poor immunity.
These pre-scans usually take a day and involve identifying the areas of the spectrum that are out-of-limits, making temporary changes to the prototype, and then re-testing to check their effectiveness. Some typical changes that affect EMC performance include: putting the device into different operational modes; depowering hardware sections or depopulating parts; re-routing internal cabling; and closing gaps with copper tape. Multiple iterations of this measure – change – remeasure cycle are done to ensure one change does not invalidate another.
By following a process that includes good EMC design practices, takes advantage of engineers’ experiences from previous projects, and encourages frequent testing, one increases the likelihood of avoiding EMC Testing Problems and launching a successful EMC-compliant product on time.
Bjarne Hansen, MESc. is a former StarFish Medical Senior Electrical and Biomedical Engineer. An avid sailor, he is also author of our most read blog for many years: Inexpensive prescreening strategies for medical device EMC compliance.
Image: 108653199 © Alexander Mirt | Dreamstime.com