Most engineers use computational methods to simulate engineering phenomena when developing medical devices. Computational modelling and simulation (CM&S) has been used for decades as an assistive tool for medical device design and development.
Our analysis group uses Ansys CM&S software to investigate fluid dynamics, structural, thermal, electro-magnetic, fluid-structure interactions, and other multiphysics problems. In many instances, evidence has also been gathered for submission to regulatory bodies, assessing portions of the design and providing evidence to confirm its safety and efficacy. This blog shares real-world examples from engineers using the analysis group CM&S to improve their medical device development.
Computational fluid dynamics (CFD) analysis
One device used CFD analysis to determine areas in the flow path that were likely to experience high fluid shear. There was concern with shear rates in the flow path causing damage to molecules within the fluid. CFD analysis was able to highlight the areas of high shear and help us adapt our design to lessen these impacted areas.
A second device used CFD analysis for similar shear analysis coupled with residence time analysis to determine the impact of channel geometry on the flow of blood going through the device.
Analysis and consultation with the CM&S analysis team provided quick iterations to determine sensitivities to changes we could implement without doing a full-scale design. Utilizing CFD analysis was effective in helping illustrate the challenges and reasons why we selected a particular design direction.
Vibrational and Thermal Analysis in Opto-Mechanical Subsystems
Traditionally optical design projects either model opto-mechanical subsystems ahead of time, or once they’re designed, characterize their vibrational modes and frequencies to understand how they wiggle due to excitation, mechanical excitation on board, or coupling of environmental vibrations into the subsystem. That’s long been a valued part of opto-mechanical design. It’s simpler than building and testing,
The optics are the critical aspect, especially how they move with respect to each other. This affects critical aspects of the optical system, including end effector position, overall precision, power levels, etc. There is also a thermal aspect due to heat from subcomponents, like motors, actuators, amplifiers, or, in high-powered cases from the absorption of light by the optical elements themselves, the lenses, mirrors and gratings. This can be incorporated into the analysis within an in silico study.
The benefit pf CM&S is getting believable information about changes in the optical alignment due to vibrations or temperature changes without having to add an extremely large number of motion and temperature sensors to a design that you’ve already put time and effort of building. When done right, it can save between 20 and 100 hours of effort in the lab. It also reduces the risk of a design spin to address defects only found out after the prototype is built.
Neurosurgery Stereotactic Device Simulations
We’ve used simulations for three different stages of a stereotactic device for neurosurgery that guides instruments into the brain. Predictive modeling helped inform the selection of test conditions and design geometries at multiple stages in the project. Our CM&S team provided valuable insights that derisked and directed key aspects of design.
Using CM&S instead of traditional methodology delivered benefits in data quality, reduced time and reduced cost.
- Saved time through reduced manual effort and duration in designing, ordering, assembling, and testing prototypes.
- Helped narrow down the options and reduced the number of test condition/part geometry variants needing to be physically tested. Additionally, many of the tests for this project were destructive, so CM&S reduced material costs as well.
- Lowered risk by reducing the influence of experimental error. Simulation results were ‘validated’ by physical testing a subset to confirm the trends instead of relying entirely on experimental or theoretical results. This is optimal because full verification and validation of the model would be far more rigorous than using the subset of physical testing to confirm the trends. Full V&V was not required because the outputs were being used for comparison rather than relying on the numerical results.
CM&S and Regulatory
With CM&S we can get an idea of the risk profile so we’ll be able to understand what documents we need and be able to anticipate the sort of questions that regulatory bodies might ask. So when writing a pre-submission (Pre-Sub) to FDA and asking questions, we can make them more specific and not super vague. That saves up to 60 days when the FDA must respond. We can give focused questions and get more specific answers.
Results from simulation can also build confidence with examiners as well, because they can see what we’ve considered (e.g., parametric studies). With the new standards for CM&S submissions, regulatory bodies expect to see more around the CM&S model and how it works – what the risks of the model are, and including the certainty for evidence obtained from it.
The FDA and their industry partners have been proactive in generating standards to streamline how quality in CM&S submissions is assessed and compiled. Primary amongst these is the ASME V&V 40 (2018). The standard outlines assessments of computational models used for gathering evidence of medical devices’ safety and efficacy. For the submission of those reports and the evidence they provide, the FDA’s recent guidance that emphasizes example cases and how deep to go in terms of validating and verifying your model. Read my colleague’s summary of the FDA Guidance Document “Assessing the Credibility of Computational Modeling and Simulation in Medical Device Submissions (17th November 2023)” for her insights on the guidance.
Also available is a formatting and content guide for submissions with the FDA’s guidance on reporting CM&S evidence. These both give industry a good guidance for how information should be gathered and formatted. The FDA has gotten ahead of the curve on that side.
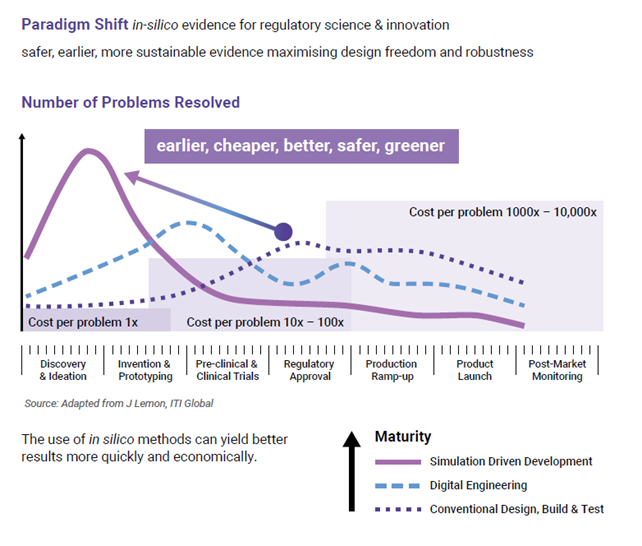
This figure compares the cost of making changes at the initial stage between different approaches to assessing technological readiness and robustness. Simulation driven development shows the highest value in the earlier stages of development, also resolving tech readiness questions with the lowest costs. As you move further downstream in the development process and make changes, the cost can be very high. There are also key portions of robustness that can be assessed ahead of full transfer to manufacturing, such as drop/impact testing, fatigue life, etc. Based on different reports, the savings can be up to 100x, though varies from project to project and application.
Added Overhead of Simulation
There is work involved to ensure the model represents reality well enough to tell trends and help guide design. That is usually around 2x to 10x less effort than a test would be in terms of setup effort, while providing more information than a physical test. Timelines compress for CM&S too, usually being 5x to 10x less than a physical prototype test. This is because the process of designing, procuring, building, assessing, and analyzing after testing is compressed to shorter iterations within the computational model.
Headset CM&S Robustness Assessment
A headset device was originally too tight on the sides of users’ heads. Our analysis team investigated the material, headband stress, and the force response. To increase confidence in the initial results, we validated the model with a bench test, showing a result that was within 2% accuracy.
In addition, we conducted studies that revealed areas of worrying stress and fatigue over the expected life of the device, which could result in premature failure of the band. Geometric adjustments were suggested to mitigate these regions for the refined, manufacturable version of the device. All these studies resulted in a confident outcome to reduce the force on users, increasing comfort and extending the headset’s life during typical use.
A device worn on users’ heads will inevitably fall. When it falls, where is the damage expected to happen, and what is the risk for safety and efficacy of the device? Critical areas such as the PCBA, battery, mechanical and electrical connections were noted, and stress on these regions was tracked during simulated drop tests. This was conducted over several high risk orientations.
If this testing was conducted with prototypes, each would cost $20k due to low volume fabrication methods early in this phase of the program. We used simulation to reduce costs and make adjustments before locking the design into higher volume, high cost-to-change processes.
One round of drop testing showed us areas of improvement in the existing geometry for the next design spin.
Conclusion
CM&S has been used for decades when evidence for safety and efficacy in medical device development is submitted to regulatory bodies. The FDA is a leader in defining standards for assessment quality, submission content, and formatting. Examples from our engineers, regulatory experts and CM&S analysis team show how we use CM&S to improve medical device development to save clients time, money and improve results.
[1] A. F. Frangi, “Unlocking the power of computational modelling and simulation across the product lifecycle in life sciences – A UK Landscape Report: Sounder, safer, faster and more sustainable innovation and regulatory evidence of medicines and healthcare products,” INSILICO UK, Sept 2023.
Astero StarFish is the attributed author of StarFish Medical team blogs. We value teamwork and collaborate on all of our medical device development projects.
Images: StarFish Medical
ELLA is a free AI-powered FDA regulatory research tool that uses advanced natural language processing to extract key insights from FDA databases, guidance documents, and adverse event reports.