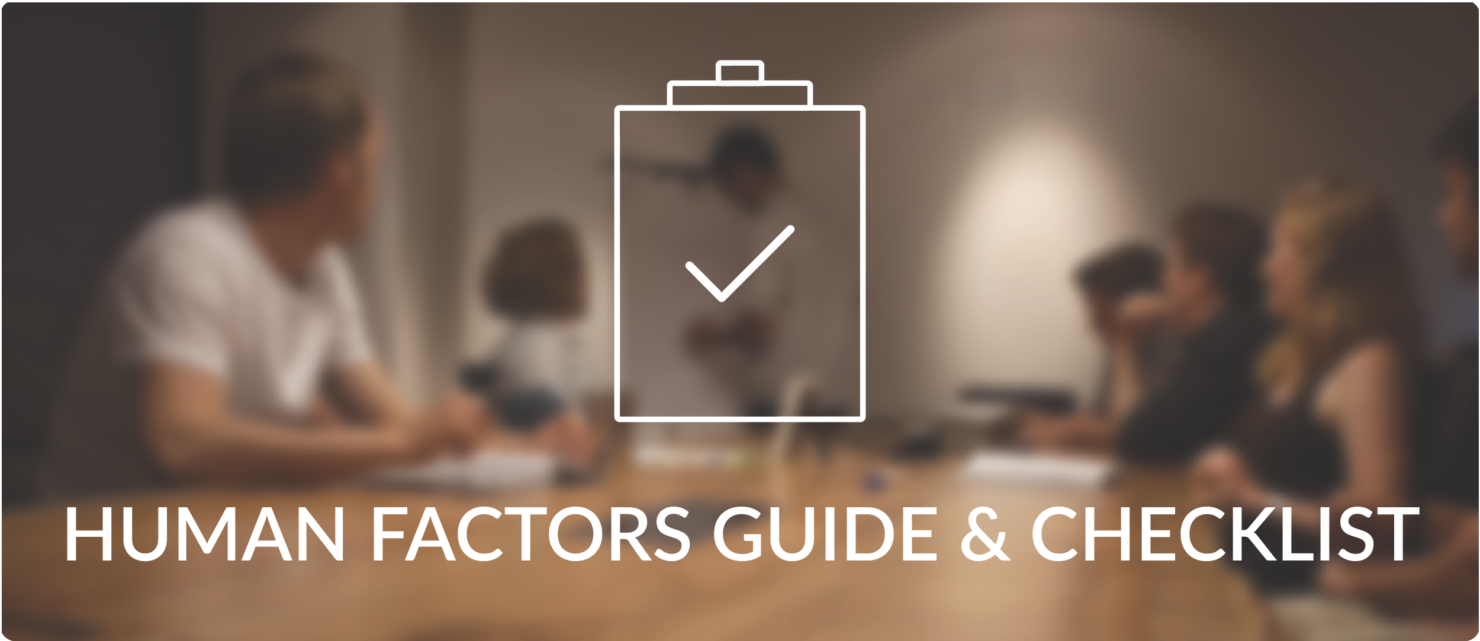
Prototyping medical devices on a budget
We prototype to learn, but also to communicate ideas and concepts. While undoubtedly 3D printing is an exceedingly useful tool, there are a number of low fidelity prototyping methods that can help launch a successful product.
As medical device developers, we are often faced with making design decisions under tight budgetary constraints. Prototyping medical devices should not be skipped due to cost. The look, feel, and perception of the product not only can be critical to its success, but can also greatly impact the project even before a product reaches the market.
Having an attractive design can influence investment in the device. Industrial design is not just about looks, but how the device may function, how it may be used, and how the device will be manufactured. Sketching is a great first step. It’s fast and can bring concepts to life, but often design decisions are made obvious by having something in hand.
We can create virtual models (CAD), but it’s not quite the same as touching and working with something tangible. What would have been nearly impossible to see in CAD can become immediately obvious the first time you pick up a prototype.
The question is, how do we prototype quickly and efficiently? Fortunately, there are a number of methods of prototyping beyond cutting chips.
2D can answer some questions surprisingly well. CAD and motion analysis tools can be used effectively to determine how a part will move – but this can take quite some time. Using a couple of acrylic pieces cut to shape and pinned together can demonstrate concepts and motions quickly. Or, as an alternative, use cardboard cut-outs; these are rough, but can also be effective.
3D is often where the rubber hits the road, and there are a number of options here. 3D printing is becoming more and more prevalent, and the materials choices are expanding quickly.
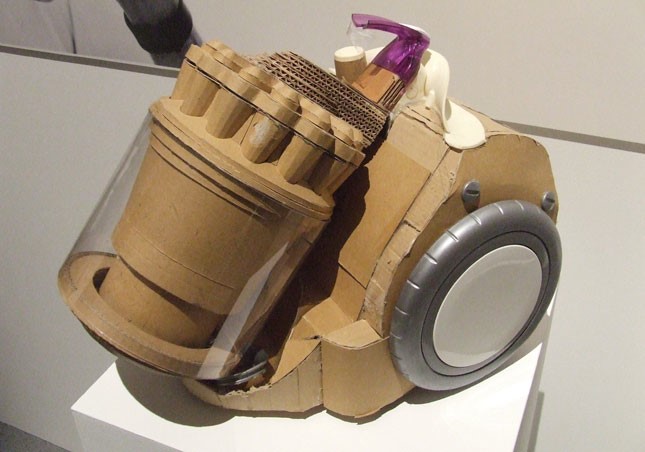
Stereolithography (SLA), or fused deposition modelling (FDM) are fast methods of generating 3D parts quickly by building parts layer by layer. Each type has its own strength. FDM desktop printers can be had for under $1000, and can create small parts quickly. The desktop printers can’t match the larger, more expensive SLA machines for resolution, however. Either way, if you just need something quickly, the parts can be ordered from growing number of companies and you can have something in hand in less than 24hrs.
If you need metal parts, selective laser sintering can create metal parts that can’t be made any other way, barring investment (aka lost wax) casting. The wax models can also be simulated with stereolithographed parts through quick casts (honeycombed stereolithographed parts), although the process is a little longer and more expensive.
For larger parts, some fantastic models can be made from cardboard, surprisingly. With a little skill, some amazing models can be demonstrated (not counting the Google VR glasses). Searching for “cardboard prototyping” will show everything from Dyson’s vacuum (above) to bicycles to microscopes.
There are specialty foams that are also used for prototyping, but even hard foam insulation can be carved to create effective prototypes and communicate ideas.
Sometimes, machined parts or cast urethane parts are required, no question. But often fundamental questions can be answered with simple tools and a day in the workshop.
Dana Trousil is a StarFish Medical Mechanical Engineer. He has successfully launched many products. He champions prototyping medical devices for all his StarFish projects.
Images: StarFish Medical