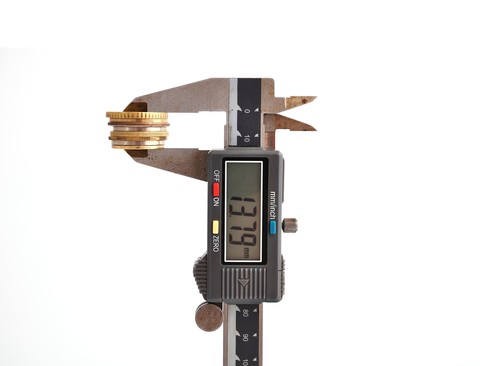
Calculating Medical Device manufacturing costs
CAUTION: Overhead ahead
One of the biggest mistakes start-up companies can make is underestimating manufacturing costs. The tendency is to focus on the cost of the components, i.e. Bill of Materials (BoM) costs. They’re important, but costs don’t stop at the BoM. Depending on the nature of the device, other/overhead charges can overshadow the costs of parts themselves.
Manufacturing a medical device isn’t that different from other forms of manufacture, with a few notable exceptions. As with manufacture in other fields, the non-BoM manufacturing costs of producing devices can add up surprisingly quickly. Medical regulatory and stringent quality requirements generally increase the steps and costs involved for a medical device.
- Let’s take a look at typical manufacture process. Manufacturing needs to:
- Create the device master record [DMR] (how to build the device)
- Set-up the manufacturing area
- Validate the process of building the device (validate the DMR)
- Buy the parts
- Ensure the parts meet specification
- Store the parts
- Receive orders, and translate that into a demand for production
- Retrieve the parts (picking)
- Assemble the device
- Ensure the device is good
- Pack and ship
- Invoice and manage Accounts Receivables (A/R)
- Set up customer feedback: Service and Warranty, returned goods authorizations (RMA)
When prototyping a device, and working out the technology, we really only touch on a few of these processes. We work on more of them areas in development. That’s often why the final sum is a shock – just how did it become so much larger than the BoM cost? However, looking at the list above, it’s perhaps not surprising at all. Each one of the steps can be broken down further, and each of these steps take labour to make happen.
Designers and developers execute a lot of the above. It’s just part of the job. But often we forget to calculate labour for ourselves. These are real costs, and costs that need to be taken into account in the final analysis. So don’t forget – you are worth it!
“Buy the parts” sounds simple, right? But with medical device manufacturing, vendors need to be approved and qualified. This may require site visits, or diving into the vendor’s quality system. Quoting can take some time, as can working out supply agreements for lot releases, vendor Quality Control (QC) checks, labelling, ordering, and shipping. Paying vendors via accounts payable needs to occur promptly.
Let’s look at another step – “ensure the parts meet specification”. One can do this by understanding and mapping the parts’ manufacturing process; if you know that process well enough, you can be confident that whatever is received meets specification. But with low volume manufacturing (and often even medium to high volume), it isn’t always feasible to map that process well enough.
Inspecting the parts is an option, but requires calibrated equipment. Inspection plans need to be developed. Even Vernier callipers need routine maintenance and calibration. A system of non-conformance control, monitoring, and root cause analysis must be in place. What was a simple step, has blossomed into many controls, all of which need to be in place for medical device manufacture. These controls take overhead to implement and maintain.
So what’s a good estimate? A quick rule of thumb is to double the assembly labour in order to estimate the overhead. If you don’t have the assembly labour, just take the BoM cost and double it, and that should be the total cost of ownership. Obviously, these are really rough estimates. If the device has some high priced components, or a highly complicated assembly, it’s going to throw off this back-off-the-envelope calculation. But when you’re working on a business case, it’s better than just looking at the BoM cost alone.
Making one of something work can be difficult. Making a thousand work equally well is equally challenging. Manufacturing medical devices makes that process even more difficult. It can be done and done well, but it adds costs. Don’t forget them! They need to be accounted for in order for your company to be successful. So don’t forget to pay yourself!
Dana Trousil is a StarFish Medical Mechanical Engineer. He has successfully launched many products, from small volume production up to moderate volumes (up to 1 million parts per year). When estimating manufacturing costs, he always remembers to pay himself.
Image: 20303888 © Vetkit / Dreamstime.com