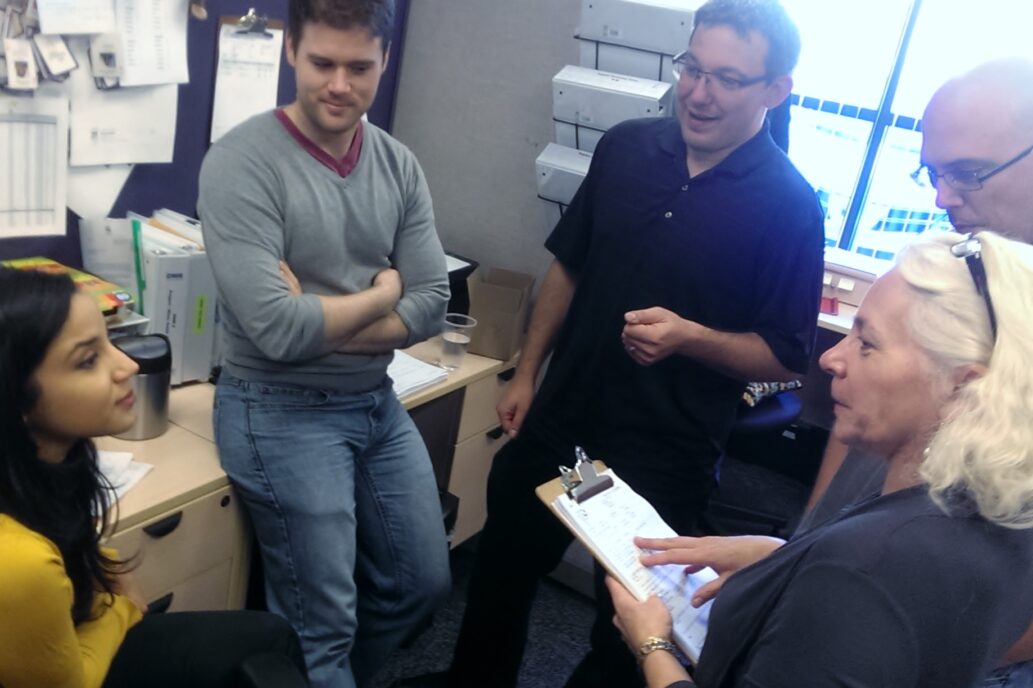
12 Design and Engineering benefits of co-locating medical device manufacturing
Most boutique medical device design and development companies do not have an FDA registered, ISO 13485 compliant medical device manufacturing facility co-located with designers and engineers. StarFish Medical Founder and President, Scott Phillips, believes this investment helps StarFish Medical uniquely tackle challenges and deliver innovation while providing fixed prices to clients.
I gathered 20 designers, engineers, and manufacturing team members to learn what impact on-site manufacturing has made on their projects and to see if Scott’s vision is delivering on the front lines. Here are some of their responses:
Direct Feedback on Design for Manufacture (DFM): I don’t have to guess which option will work best in manufacturing, I can ask the experts or test the options as part of my development process. For example, in one project I was able to obtain feedback on optimizing a gauge system that was not intuitive, but saved money and improved the device.
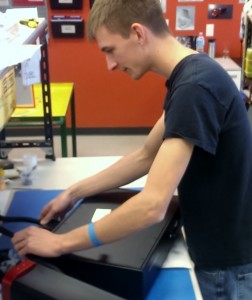
Materials on hand for Proof of Concept (POC): Working with the actual manufacturing materials during the development of a POC prototype saves time and money while reducing risk. Many times materials are already in inventory or suppliers are lined up from previous projects. Supply chain is already set-up, and can leverage lower costs and lead times by having more volume. This is one of the ways manufacturing in-house reduces lead times.
See how other things are being built: It’s incredibly instructive to see a variety of non-related devices being manufactured. I learn new techniques without spending a lot time to experiment with different materials and constructions. For example, the thermal bond on another industry standard, non-novel project, worked well for a new device I was designing. The client gained time, leveraged prior learning, and ensured manufacturability with a proven product and process.
Design to best suit manufacturing capabilities: For early and small runs of highly complex medical devices, the ability to design with deep understanding of the manufacturing team’s capabilities removes lots of uncertainties and speeds time to market.
Designing for Assembly: Building one of something is not the same as building thousands. A lot of expertise is required in developing a product for manufacture. With manufacturing expertise in-house, we are able to design risk mitigations early in the process, saving time and problems later on. We can reduce assemble time as part of the design process.
Engineers get to test design ideas and options with manufacturing experts: Access to manufacturing professionals with immediate feedback on my choices and options adds insight and gives me confidence that my designs will turn into manufacturable products. I appreciate the direct access for design engineers compared to waiting for prototypes or parts to arrive. That helps me catch mistakes faster.
Young companies have a “get to market” focus, mature companies recognize “costs must be right.” Integrating the design team with manufacturing lets me speed the development process in a QMS environment. It also helps us refine the design for cost savings that will support the right business case by working directly with supply chain and manufacturing teams who will source and build the products.
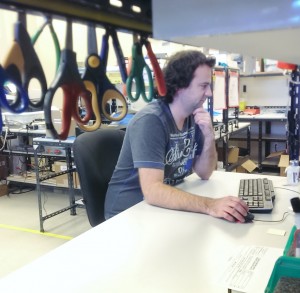
Complete control early on with prototype–structured supply chain, production, quality vendors, pedigree on parts: Having manufacturing and supply chain in-house means complete control for parts coming in, quality inspections, and a full manufacturing process for prototypes. This is a huge advantage for the Design History File (DHF) and regulatory approval process. Device history records can be maintained within a production system. It results in better end of line, better Quality Control (QC), and better final product.
Engineers don’t have to assemble prototypes: I’m grateful to have professionals in manufacturing assemble small prototype runs. Clients are grateful that we use lower manufacturer labor costs where possible. My time is freed up to work on other challenges, the manufacturing team gains familiarity and can offer feedback, vendors are managed by a professional supply chain.
Audits span manufacturing and design – no silos: A real benefit to clients may happen post market launch. Should they be audited, the entire design, development and manufacturing chain is in one organization. This greatly reduces the coordination, preparation, and costs of an audit.
More important for complex devices: The more complex a device is, the more important it is to keep great records from the start, design with manufacturing in mind, and build a quality, reliable supply chain and manufacturing team. This intimate connection allows us to reliably quote all the way to a transfer to get to market.
Tested documentation: The manufacture documentation is created and used from the very beginning of design and development.
Early runs benefit from proximity to design team: As the project goes from building one of something to hundreds of units, variances may come during manufacturing. This is where have the design engineers on hand can speed trouble shooting and cut time and costs. Similarly, co-location allows the team to more efficiently manage supply chain design obsolescence—common with low volume, high complex devices.
The team enjoyed sharing and comparing notes with each other. Now it’s your turn. What benefits have you reaped from working with design and development firms that co-locate medical device manufacturing?
Jason Dolynny is a former Director of Manufacturing at Starfish Medical. Please visit our Services page for more information on Medical Device Design, Development and Manufacturing at StarFish Medical.
Images: StarFish Medical