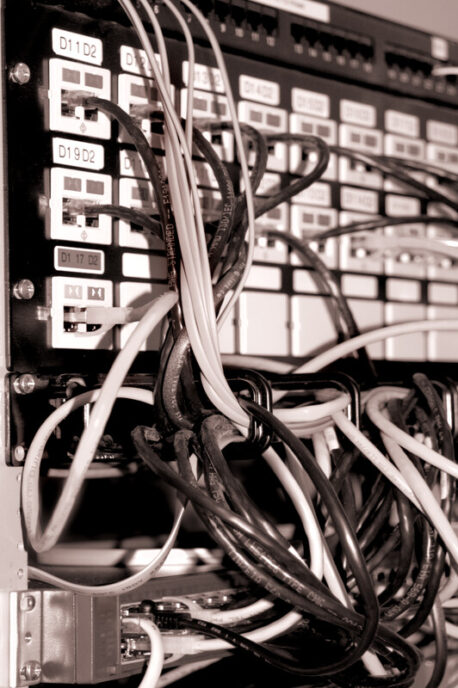
I Hate Wires
Does this conversation sound familiar?
KM: How’s the product design going?
EE: The PCB designs are done.
KM: How do the boards connect to the motor, heater, laser, each other, etc.?
EE: I put connectors on the board. We’ll wire them up.
KM: When will you do that?
EE: When the boards arrive.
I have learned not to be too subtle while having this conversation because others often don’t get that shiver of fear rattling down the back of their necks like I do. There are very few things more frustrating than spending a day or more in the lab wiring up a new system when missing your deadline is already imminent for other reasons.
Fortunately, I’ve found a very pleasant solution which I now brutally evangelize: avoid wires. I ‘m not pushing RF or IR: I mean wireless in the “less wires” sense. Even before a product is a twinkle in anyone’s eye I’m lobbying to remove wires. I know that’s maybe a bit unreasonable but if you don’t have lofty goals then you’re doomed to mediocrity.
So how do we do it? We use those very PCBs that required the wires in the first place. Instead of choosing connectors which must mate with wires, we choose board-to-board ones. Instead of making boring, rectangular PCBs, we make cool, odd-shaped ones that fit intimately with the other hardware bits. Connectors to the outside world are put on the same plain; controls, switches and indicators are chosen and located so they are board-mounted. Finally, we do all of this in a way that doesn’t make the Industrial Designers hate us.
I can picture the unbelievers in the room shaking their heads: “How can all of that be ‘simpler’ than just wiring things together with a good, old-fashioned wiring harnesses?” Well, the simple answer is that it’s not, but often only by a tiny little bit. Even wiring harnesses must be designed, wire lengths specified, connector housings and crimps chosen, BOMs built and procedures written. Of course this assumes that we’re going to document the wiring properly. We are, aren’t we?
If the effort is a wash, what’s the real advantage? Timeline. Back in the early stages of the detailed design of the product, the interconnection strategy can be worked out through collaboration between the electrical and mechanical engineers. The boards and mechanical parts are designed pretty early in the process and so the interconnection is too. This is in contrast to the week before the first prototype ships if you defer it all to a complex wiring harness.
Let’s not fool ourselves though, there will always be wires. How do we prevent even the small amount left from causing grief at the last moment? We design it as best we can up front. Wire lengths and routing can be estimated early during design; components can be chosen back then too. It all can then be built early, even subcontracted. When the boards are in and the initial power-up and debugging took longer than expected, you can at least take comfort in knowing that you won’t waste that day or two mucking around with crimpers and things when you should be tackling the deeper problems that you haven’t even discovered yet.
Let’s not leave it down to the wire.
The simulation tools I’m talking about is the use of computers to numerically model the behaviour of a system, particularly an electronic or electromechanical one. Typically this is done using a simulation tool like Spice, although often MATLAB, FreeMat or even a spreadsheet can be used effectively. This method allows detailed exploration of system performance over a wide range of conditions prior to building a prototype. It is especially useful to test conditions that occur infrequently or ones you can’t easily replicate with the available test equipment.
The problem comes when you forget about the real world and assume the simulation is absolutely correct. Simulation models are frequently wrong, incomplete or inappropriate for your particular purpose, whether you made them yourself or got them from your part library or even a manufacturer’s website or datasheet. For instance, the models rarely take into account actual physical limitations: you can get valid looking simulation results from a situation which would vaporize parts in a microsecond. Similarly, the system you modeled might ignore some part’s non-ideality or a parasitic signal path that occurs in reality that critically affects performance. I simulated a circuit recently and toyed with what I thought could be a tremendous improvement, only to realize that it required completely impractical matching of two components.
The trick is to always think like you’re breadboarding. Imagine what you would do in the lab and what you might see. Pay special attention to the operating parameters that you simulate and how the parts would behave in those conditions, especially with respect to their absolute maximums. Simulation complements real lab experimentation: model it, make it and repeat as necessary.
A situation I always simulate is to validate the choice of switchmode power supply inductors. If the inductor is poorly chosen the circuit will smoke. I find that the typical equation-based methods for determining the peak current requirements often are optimistic. A quick simulation regularly shows that under certain conditions the current will go just a bit higher. Simulation is also very useful in developing feedback systems. Even in medical devices it’s not unusual for a control system to have hundreds of Watts at its disposal. To rush to experimentation in such a system is likely to result in damaged parts or even injuries.
The key though is to always go to the lab and build stuff. Even if you have simulated a system and think you’ve cracked a particularly tricky nut, you will still learn more when you really do power it up. I find frequently that I missed some key part or characteristic of a system once I actually solder it together and start scoping. In that case I go back to the simulation, make the change and then return to the lab. Simulation allows me to quickly test out a ton of circumstances to ensure the system will behave and then I double check these in the lab with real testing.
With a careful balance of simulation and hands-on lab work, I save a bunch of time and prototyping cost and end up with much more confidence in my designs.
Kenneth MacCallum, PEng, is a former Principal Engineering Physicist at StarFish Medical. He works on Medical Device Development and loves motors, engines and trains as well as the batteries that power them. View his work in our Case Studies.
Image: © Can Stock Photo / lsmirnov