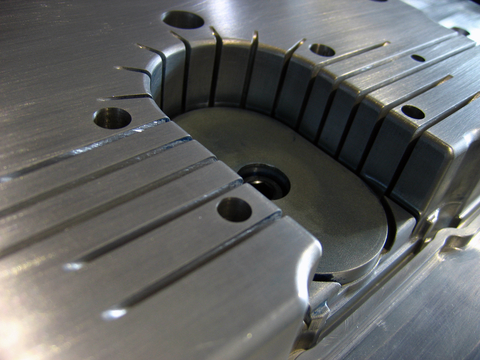
5 cost-associated boxes to check before engaging in injection moulding
Who is your best toolmaker?
I’m not reinventing the wheel to say all decisions in life are based on the balance of quality vs cost.
Is good and expensive better than “only ok” and inexpensive? Or is difficult and time-consuming better than easy and quick? It’s important to have a good understanding of the quality we want and its associated cost.
Our medical device clients undergo this exercise when choosing a toolmaker for their plastic parts. Usually they focus first on cost and then try to optimize quality as much as they can within that cost. Tooling cost represents a large, initial capital expense, so their focus tends to be on this value, rather than on other factors. However, tooling cost can change considerably depending on assumptions that moulders make when quoting on your parts.
It is necessary to have an extensive conversation with potential moulders to make sure they are aware of your parts complexity, materials they are made of, and how the parts will generally interact in the final product. This includes what tooling life you are expecting, whether multi-part or multi-cavity tools are desired or allowed, what sliders and lifters are needed, and the type of surface finishing, etc. Discuss these items with each injection moulding company you submit to for quotation as it is essential to perform a comparison between them. Otherwise you won’t be comparing the same thing, and you’ll waste time getting the right data.
But wait, is this all you need to know to make an accurate comparison? The answer is no.
These are some other basic cost-associated parameters you should consider before contracting with a specific injection moulding company: cost per part, tool replacement, tooling adjustments, design for manufacturing, and of course, time.
Cost per part
The cost per part is the price associated with each part being produced (i.e. out of the mould). Injection moulders have different costs per part depending on the number of samples required. Having a final Bill of Materials and well defined sales volume estimates can help determinie how many parts are going to be ordered at once and result in a more accurate final cost estimate. If you have a good business strategy, raw part cost should be one of the first things to be considered since it will define the final price of your product. (See Scott Phillips’ blog: Margin Matters.)
Tool replacement
Toolmakers use aluminum or steel tooling depending on their expertise and the project they are facing. Both technologies have advantages and disadvantages. For example, aluminum tooling is easier to create, but cooling rates are harder to control. Steel tooling works fine with almost all kind of plastics and has high life expectancy. With aluminum tooling you can expect a maximum of 100,000 shots (i.e., a lifetime of 100,000 uses). Steel tooling will easily give you 250K, and potentially much higher. Tooling can be repaired, but eventually, the quality of the parts and repair costs justify a new tool. Before engaging to a specific injection moulder, consider the benefits of using aluminum or steel tooling, you don’t want to be replacing tooling every 6 months!
Tweaking of the tool
Anything that can go wrong, will go wrong. As odd as it seems, Murphy’s law should always be considered in injection moulding. The job of making real what we see in the computer is not easy. Toolmakers deal with a large number of variables (backpressure, clamp pressure, injection pressure, injection speed, mould temperature, size of gate, etc.) All of these can have a critical impact in the final product, particularly when small tolerances are in place.
Setting up injection moulding machines can take a few runs to dial all of the parameters. Other times, design changes must be implemented to achieve the desired functionality as the injection moulding process has inherent variability (tolerance) and it may be larger than expected (thank you, Murphy.) These changes on the tool (tweaks) have an associated cost that some toolmakers might include (to some extent) in their initial quotation.
Design for manufacturing
Imagine this: you just chose who you thought was the perfect toolmaker. Good quality at a good price. Your parts are beautiful and ready-to-be-moulded. Coherent parting line, perfect drafting, nice wall thickness ratio in all your ribs, thickness consistency and thin tool condition have been analyzed. Then you get an email from your toolmaker showing all issues that must be addressed in order for them to be able to start cutting steel… You pause and wonder… Why? Didn’t I have the perfect part on my hands?
Not all toolmakers have the same capabilities and experience, and might not want to initiate a project they think could entrain certain risk. Even if you have a ready-to-produce part for some toolmakers, you might be dealing with a part that is too complicated for others. Before engaging, make sure you are on the same page and no major changes must be required to the parts that will be moulded. These changes take time that usually translates into money.
Time
Last but not least, time is probably the most important factor. Each minute your product is in the injection moulding machine instead of on the market is a minute that you are losing money. Toolmakers have lead times that average 8 weeks. However, depending on the number of parts and their complexity, this time could be notably increased.
Nowadays, most of the companies in North America choose Asian facilities to develop their businesses. Communication is often delayed. For example, during the stage of tweaking the tool, each change you request is sent via North America to Asia. Asia approves it and talks to North America, which then talks to you. If you have a question, the loop starts again. This is definitely something that will add cost and should be considered.
In summary
Make sure when you are comparing different toolmakers that you are doing it with a meaningful cost in hand estimate– a cost that considers Cost per part, Tool replacement, Tweaking of the tool, Design for manufacturing, and Time.
Joan Hereter Gregori M.Eng. is a former StarFish Medical Mechanical Engineer. He helped develop criteria for vendor comparison as part of his work in product development. This is his first blog for StarFish.
Image: 639236 © Bogdan Lazar / Dreamstime.com