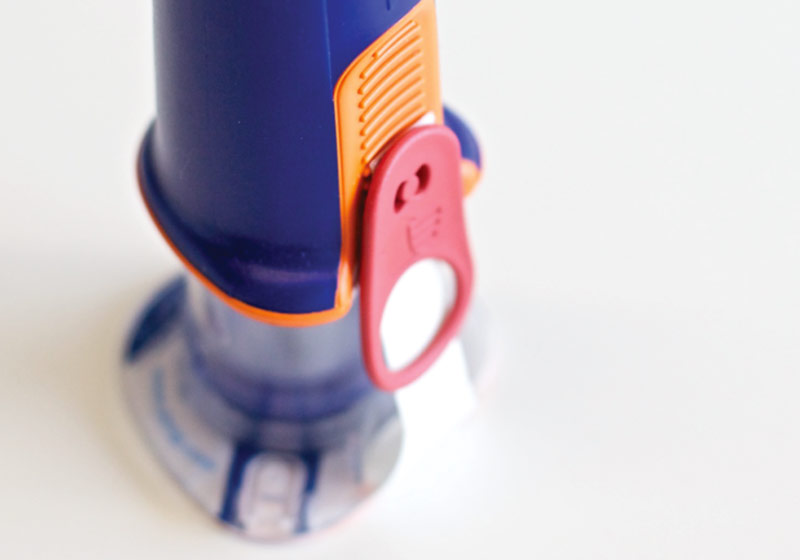
9 ways good ID impacts medical devices
Recently a group including engineers, project managers, manufacturing, and QA colleagues discussed the impact of Industrial Design (ID) and Human Factors on medical devices. Although no one from the ID team was able to make the discussion, their cause was well supported. The conversation identified 9 ways good ID impacts medical devices and lots of ideas for future blogs.
Usable and useful
We’re not in it to win awards. Some companies design devices to look nice. We design the form and skin to be usable and useful. Our industrial designers do more than package technology up and make something look nice. Great things happen to a device by going through work flow and human factors analysis by industrial designers– like safety and efficacy.
Clinical reality check
It’s often like pulling teeth to get a device to clinic, but almost always, there’s this “a-ha moment” which totally changes the project. Just about every project changes due to Human Factors. Here are 3 examples:
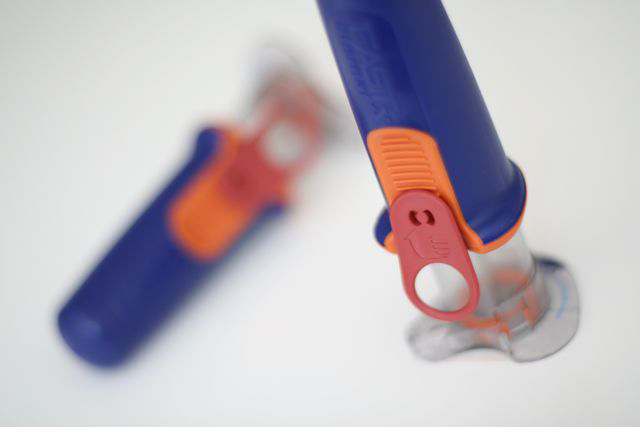
- A blood lab device changed when we realized how packed all the benches were. It required a deep and skinny device rather than the original shape so it would fit with everything else in the lab.
- Recently we planned a surgical device to be a couple inches in size. During a site visit one of the doctors had a microscope just a few inches from the patient’s head. Our device and additional tools were supposed to fit into the space in-between the microscope and patient. Human Factors pointed out, “Did anyone notice the fact that this device is too big?” This will affect the shape, architecture, and design of that product.
- For a digital health product, the doctor described how he faces patients when using the device. We designed a two-sided device allowing both doctor and patient to see the screen. During an observation visit with an actual patient, it turned out the doctor and patients actually sit side by side. That was an “a-ha moment” that required product redesign.
IEC 62366
What designers are addressing is the human factors of a design. We’re blessed in this world of regulated medical devices that IEC 62366 is an expected standard or usability errors need to be demonstrated and mitigated, or all the other human factors pieces that are required as well, sometimes what we address with designers, others address on more of a risk analysis basis. Putting a battery and PCB together is not a high risk. It’s the usability of a medical device that is the make or break thing.
Augmenting Key Opinion Leaders
Like non-medical device technology companies, some clients think of their marketing person as being the expert in human factors and usability. Marketing thinks of their Key Opinion Leader (KOL) as the expert— especially one that’s on their board.
KOLs are by no means a proxy for the rest of the market. We’re not tearing down the role of a KOL, but you need to augment their information. That’s why we push for site visits where you meet 7-8 different people that interact with the device and see them in action. KOLS are wired differently than regular doctors who are swamped under their patient load and then going home trying to remember their kids’ names and do their paper work.
Any time you come up with a new technology, you have a lot of KOLs who tell you how you should be using it or what everyone feels. When you actually go and spend time with the device and everyone who interacts with it, you learn an enormous amount about the requirements. It’s a pretty easy investment trade off to make. You can spend a day doing a visit and then a year developing with confidence.
Workflow diagrams
When we observe procedures in action, part of what we look for is how humans interact with the devices. Medical devices are different than other devices in that there is usually more than one user. The person who is applying it and the person it is being used on–plus others analysing the data, biotechs, and even the cleaner.
What’s often comes out of a visit are workflow diagrams and documents that find unknown unknowns for clients. These become the “A-ha moments.” They can be across the board details including things like “How do I install it?” From a product lifecycle perspective, Human Factors pull things out upfront that need to be known. This “find High Risks” approach fits really well for most clients even though they may not know that they need it.
Product evolution
Usually a technical and ID person go together on a site visit. The design is done in conjunction. It works well because the technical person can be the constraints lead always thinking from the inside out and the ID person can be thinking from the outside in. That keeps the two trains of thought together.
The design evolves because of the site visit. That can be said all the way through the process including verification and validation tests. Ideally we don’t have an “A-ha moment” massive change of concept, but more of a change of course. We learn every visit– whether it is going to make the product successful, or work, or something in between. Often it’s a usability concept where you go, “Huh, I didn’t think of that. Now we have to change the design or incorporate that.”
Looks vs. usability
Use constraint has to come first. In the end you will make it look good. It’ll look good because it will meet their user’s need and match their expectations. If you need to reconcile any discrepancies with known guts of an instrument and known outside element, that is mostly handled through exploration within the team.
(Editor’s note: During our internal review process, Industrial Designer, Christine Park added the following perspective: “I don’t always agree. This is talking about does “form ever follow function”? This phrase became popular after 1930s by architects who advocated minimalist design that are efficient to build over buildings with decorative ornamental elements. However since then, we discovered that consumers don’t always buy products that perform best or most efficiently but often times they buy what looks good. Form does not always follow function. Form sometimes must follow what is socially acceptable instead of function. What the market wants it to look like. Also, if form always followed function, you would not have differentiation between brands. This holds true in medical device industry as well. First and foremost, we must mitigate use error risks through design. After all the risks have been addressed there are situations where form should lead function. By designing the look of a device you can help patients feel more comfortable or at easy. That can outweigh the benefit of having the device perform most efficiently but look intimating or discomforting to the patient.”)
Technical Trade-offs
In early development, design houses often make a thing that looks great and then hand it over to engineering. Drawing something pretty based upon nothing gets people excited. It gets investors talking. We try to put some reality into it by having engineering involved in the ID early on so a design looks very plausible from the get-go rather than like Star Trek.
Verisante’s ‘Aura’ is a good example of this issue. The early outer design was a nice flat, disc shape. It turns out that when you put everything into it, the shape was inefficient for the components and had to be expanded in height. Changes in form like this can be time and resource costly and are best identified early on.
Manufacturing Trade-offs
A client was having problems with color matching. With ID, you can draw something and make it look pretty, but manufacturing reproducibility is a big problem. Especially in small volumes. One unit will look good, then the next batch will look a bit off– noticeably different. Often it’s like a second order effect of the first. There wasn’t enough reality put into the concept. The reality in this case is understanding manufacturing techniques. And design specifications. Certain colors and finishes are chosen because they are much easier to reproduce. Part of the solution is to pick different colors for different materials.
Bottom Line
Good medical device design is creating something that everyone can use. Something that meets all the requirements. It looks good. Users are intuitively able to employ it. There are no confusing areas. The user is never hesitant. Not only is it safe and effective, people enjoy using it.
Astero StarFish is the attributed author of StarFish Medical team blogs. We value teamwork and collaborate on all of our medical device development projects.
Images: StarFish Medical