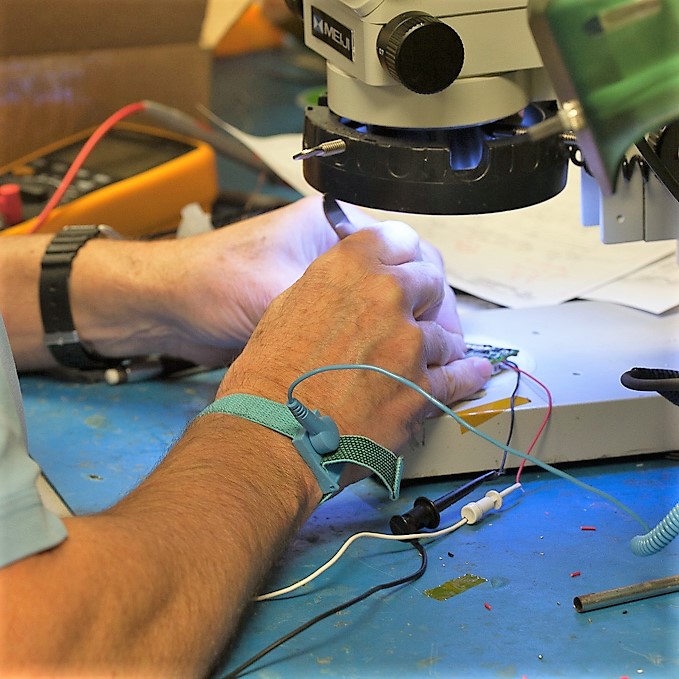
Advantages and Disadvantages of Designing a Custom PCB
When designing an electrical or electronic system, product designers may find themselves asking “Should we be spinning a custom PCB (Printed Circuit Board), or hand-wiring on a perfboard or breadboard?” This article discusses some of the advantages and disadvantages of Designing a Custom PCB identified during a group discussion of StarFish Medical electronic engineers.
There are three reasons people often shy away from spinning a custom PCB:
- Flexibility: “We can’t commit to a particular design yet.”
- Cost: “It will be too expensive.”
- Timeline: “We need this sooner than that.”
Flexibility
A custom PCB is not an inherently reconfigurable thing. When a product is in its prototype phase, the appeal of soldering something up on a work bench that can easily be changed later can be very enticing. For example, you realize that there is a feature needed that you didn’t include, or you discover a hardware bug. A hand-built electronics assembly isn’t locked into a design that takes a few weeks from the moment gerber files go out the door until a fully assembled board is on your bench. Concerns around flexibility fall into two basic categories: “What if the requirements for the board change?” and “What if we discover a hardware bug?”
“What if the requirements for this board change?”
If you ask yourself this question, then subsequently ask yourself: “Have I fully thought through my system architecture?” and “Have I consulted with the mechanical teams, ID team, etc. and fully determined the requirements of this board?”
The fact that a PCB locks you into a design is not always a bug, but often a feature. It forces you to plan out the system architecture, which often results in details getting fleshed out that would become an afterthought if you approached the design in a way that didn’t require commitments.
In some cases, the reason that you’re concerned about requirements changing may be because the project is expected to change. Some projects need significant requirement flexibility for prototypes. This can mean that custom electrical components normally designed as custom PCBs may need to be built in other ways.
“What if we discover a hardware bug?”
Changing requirements can be relatively easy on a designer’s nerves compared to that exciting-but-also-uncomfortable period of time when you’ve designed your board, the fab house has your gerber files, the assembly house has your bill of materials and your pick and place files, and you’re waiting awkward weeks to get your board so you can test it and confirm that it actually works.
The first spin of a PCB for a prototype usually needs some tweaks. If you design the PCB recognizing it will likely need at least minor modifications, then altering a custom PCB with an X-Acto knife and a soldering iron is often no more difficult than modifying a perfboard.
All this being said, building some circuits on a breadboard ahead of time is a great way to de-risk a design. Ideally, this will quickly morph into a custom PCB moving forward.
Cost
The cost of a PCB varies hugely on the size of the board, number of layers, how many components are on it, and many other factors. The material cost of a breadboard or perfboard is clearly significantly less than the design time. Focus on how to reduce cost by reducing the time that it takes to develop the product. Do not worry too much about material costs. Experience has taught me that when project budgets balloon out of control, it happens primarily due to labour costs and not to material costs.
This invites the question: Is the labour involved in designing a PCB less than building something on a perfboard or breadboard? In the short run, it often isn’t. But in the long run, it often is. This is related to a few factors:
- Custom PCBs often require less re-work than an electronics assembly that’s been built by hand due to their inherent superior reliability.
- Once a PCB has been designed and built, the schematics, gerber files, and bill of materials can be re-used to cheaply build a second PCB. This is handy if a second prototype is needed but wasn’t originally expected. This happens all the time.
- Schematics can be recycled for future iterations of the same device. Once you’ve designed a PCB for a prototype, you can save design time when designing your alpha.
Timeline
A tight timeline is always intimidating. The need to meet a tight timeline often means parts of your system that could be custom PCBs will need to be hand-wired in some way or will need to be off-the-shelf components.
One option for shortening the timeline for a PCB is to order a bare PCB and assemble the PCB in-house. Fab + shipping time required to get a bare PCB in the door can easily be just a week.
Short timelines will mean that you may have to build custom wiring harnesses that you’d prefer to be absorbed into a custom board. They may also mean that you’ll have to hand-modify some off-the-shelf components or modify custom boards you designed instead of re-spinning them.
Advantages of Designing a Custom PCB
Technical Advantages
When you design a custom PCB, you have control of the location of every piece of copper down to a few thousandths of an inch. This control allows you to more easily mitigate parasitic properties of your circuits. This is enhanced by the fact that you are not limited to through-hole components, which have higher inherent parasitic inductance than their surface-mount equivalents usually do.
Appearance and Perception of Your Device
Technical advantages aside, a PCB simply looks more professional. Some engineers believe that the way something looks is irrelevant. How well it works is ultimately all that matters. However, a custom PCB will significantly affect the perception of your product in the eyes of clients and investors. Appearance and Perception matter.
Conclusion
Custom PCBs cost money, require a commitment to a particular design, and take time. These disadvantages are often not as significant as one may think. After the cost of re-work, the ability to recycle a PCB design, the inherent robustness, and other advantages should be carefully considered before choosing between spinning a custom PCB (Printed Circuit Board), or hand-wiring on a perfboard or breadboard.
Kris Dolberg is a StarFish Medical Electrical Engineer. He often writes on designing PCBs. Kris is a graduate of the University of Victoria where he was part of the ECOSat team that won first place in the Canadian Satellite Design Challenge.
Images: StarFish Medical