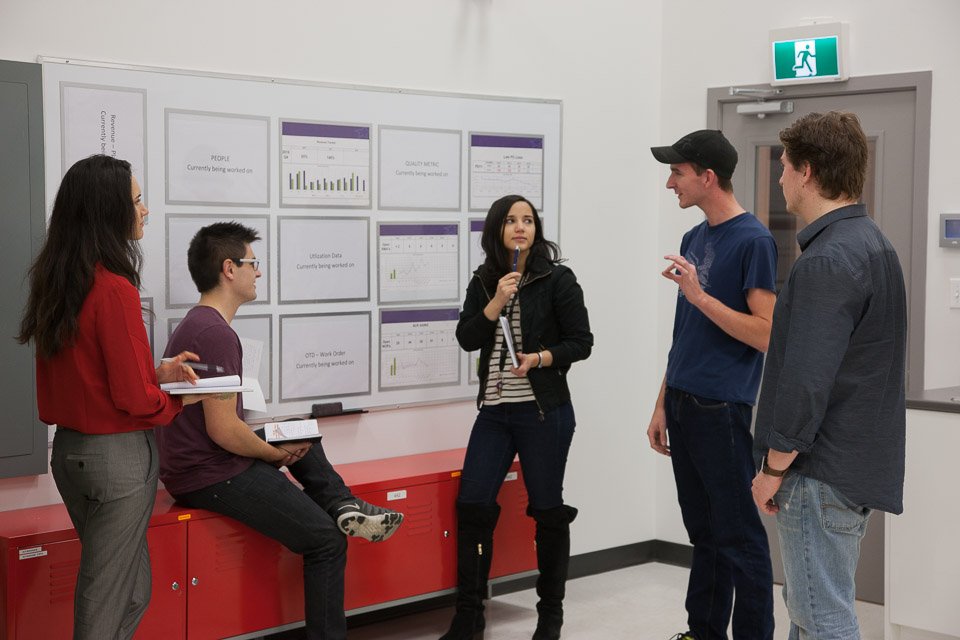
Applying PFMEA efficiently to Medtech manufacturing process
Process Failure Modes and Effects Analysis (PFMEA) can be a powerful tool to identify potential failures in the manufacturing process of medical device, and help prioritize which failures should be improved first. However, the effort required to complete a PFMEA can take many hours, which costs money. Applying PFMEA efficiently will be addressed in this blog.
Based on my experiences, to maximize value, a PFMEA should be performed as early in the manufacturing development cycle as possible. In addition to regular PFMEA processes, I will share some tips and tricks for making the PFMEA process more effective and efficient.
Applying PFMEA efficiently in the start line
A detailed flowchart of the process or a traveler (a list and record of instructions that follows a part in a manufacturing process) is a good starting point for reviewing the process to be sure that all team members are familiar it. This is especially important if you have team members who do not work on the process on a daily basis.
Instead of gathering a larger team of everyone involved in the event (just in case a specific team member might be needed), invite only the core team. Put the others as “experts on call”. When the team runs into an issue, highlight the impacted flowchart cell by color to identify who needs to answer the question. Then bring in each expert as needed, and review any questions for the expert all at once.
Typical PFMEA team members may include Manufacturing Engineers, Design Engineers, Industrial Design Engineers, Tooling Engineers, System Safety Engineers, Supply Chain Engineers and even Customers.
Applying PFMEA efficiently in Forms and Templates
While the RPN focuses on failures which could enter the field, high impact and high frequency (with good detection), cause manufacturing headaches. To highlight these issues, create a new column for Severity x Occurrence.
Process Controls and Detection are often contained in the same column. With only one column, groups tend to focus too much on the detection and forget to talk about prevention activities. I recommend breaking out process controls from the detection control column, and having the columns in this order: Cause of failure mode, Process controls, Occurrence score, Severity x Occurrence, Detection controls, and Detection score.
Applying PFMEA in Efficiency (completing PFMEA faster with fewer people)
Before diving too deep into the exercise, scope the overall effort ahead of time. Consider evaluating Key Characteristics, Critical to Quality (CTQ) or Most Important Requirements (MIRs) only, instead of trying to assess every requirement. The idea is to start with the most important risks, so the biggest risks get identified as early as possible.
Start with listing all the failure modes, then group the failure modes together and score them all. This helps align the team with the proper severity score. Next, list all the detection controls and detection scores (that align with the failure modes). Next, brainstorm the causes of the failure modes, then list the process controls and then score the occurrences (to help align the occurrence scores).
Keep sessions between 2-4 hours long. Over 4 hours can be tough for the team members to keep attention. Less than 2 hours is inefficient, since it takes some time to get setup and calibrated, and requires scheduling many more sessions, which increases the chance of people not attending.
Applying PFMEA in Effectiveness (Identify more potential failures and causes, and make analysis more complete)
Bring in the physical product, forms, software (view on screen), etc. being discussed so the team can physically see the process. If possible, perform the PFMEA in the actual process area, so observations and questions can be answered quickly by the right people.
Be sure you are listing and considering all the potential failure modes for each function/process in all three levels of System, Sub-system and Components.
Fill out as much detail as possible in each column, such as document and reference numbers.
In order to reduce occurrence scores after actions are implemented, you must include a process control (training, fixture, mistake proof device, procedure change, etc.).To reduce detection scores, you must implement an inspection or test.
Determine the effects associated with each failure mode. Some failures will have an effect on customers and others on the environment, the facility, and even the process itself.
A regular review of the PFMEA should be set up as a recurring meeting (suggest monthly or quarterly), to force teams to get together and update the PFMEA.
To assign detection rankings, identify the process or product related controls in place for each failure mode and then assign a detection ranking to each control. Detection rankings evaluate the current process controls in place
Don’t use a cut-off RPN score as the criteria for determining if action should be taken. Instead, work on the top risks only. Teams can be biased in their scoring when trying to stay below a value (such as 150 or 100) that would require action.
Some processes may have many actions over a stated threshold, however, the team cannot address all of them at once. I recommend taking action on the top 5 RPNs regardless of score.
Customize the PFMEA ranking tables to align with your business to minimize scoring differences between teams. This is especially important when conducting a PFMEA in a service or transactional process.
Applying PFMEA efficiently in Action Plan and Outputs
PFMEA output includes Actions to prevent causes, Actions to detect failure modes, and a Document History of any actions taken.
Bear in mind that Mistake-Proofing, Statistical Process Control, and Design of Experiments are among the most powerful tools available. These techniques can make it impossible for a mistake to occur, thus reducing the Occurrence ranking to lowest possible level. This is especially important when the mistake Severity Ranking is high.
Statistical Process Control (SPC) is a statistical tool that helps define the output of a process to determine the capability of the process against the specification and then to maintain control of the process in the future.
Design of Experiments (DOE) is a family of powerful statistical improvement techniques that can identify the most critical variables in a process and the optimal settings for these variables.
A PFMEA control plan needs to address three types of control groups: Prevent the cause, Detect the cause and Detect the failure mode
PFMEA is a continuous improvement tool and a living document that needs to be updated throughout the entire medical device life cycle. Use my tips above to make the PFMEA process more effective and efficient for your organization.
Vahid Faridsaleh is a former Production Line Manager – Toronto at StarFish Medical. He has over 16 years experiences in Medical Device Industry, with extensive background in design, development and production in this field, includes several Medical Device New Product Introduction (NPI).
Images: StarFish Medical