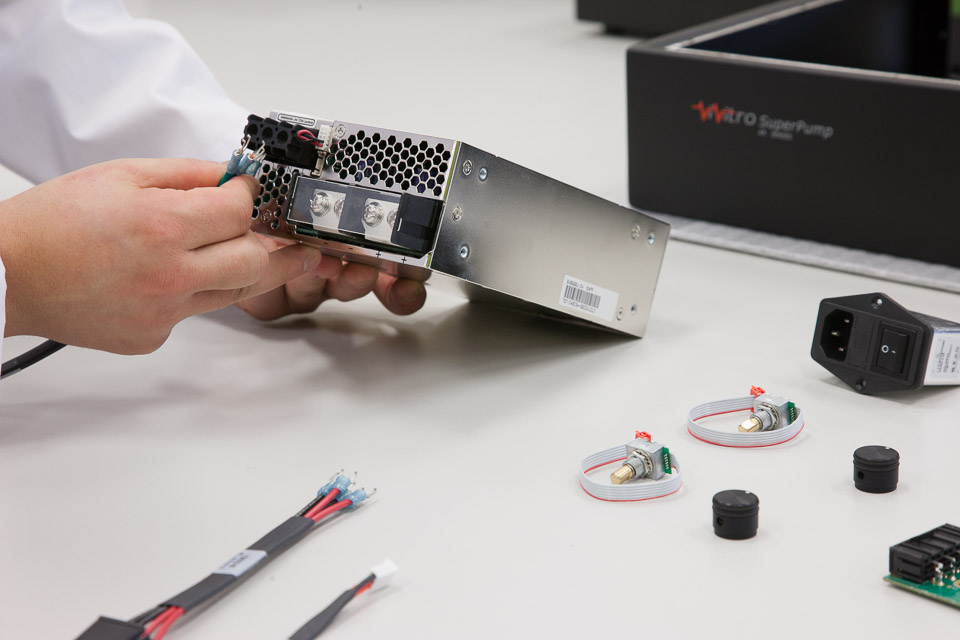
Top 3 root causes of design transfer problems
Often when a product design is completed and the design transfer to volume production begins, medical device developers run into a tsunami of issues that prevent them from meeting their planned build schedule and impact their capacity to meet forecasted sales.
An endless stream of new, unforeseen technical issues occur. Examples include high variability coupled with low system tolerance causing low product yield, or high production process variations causing long build delays. Sometimes even simple things like skin panels cannot be properly aligned during assembly.
Teams may encounter project issues like unanticipated long lead time on parts procurement, critical components going end of life, or mismatching part revisions between development and build phases. Cost can be impacted through vendor pricing increases, replacement part cost increases, or higher costs due to lower order quantities. All of these project risks can massively derail a build schedule or success
3 root causes are responsible for most of these issues:
- Companies don’t fully understand the true current state of their product prior to production transfer. They release the product to production too early – before the design is mature enough to be produced. Instead, they might have released a proof of concept design, or a proof of design design, or a proof of product design instead of a proof of production design. i.e. A proof of design is not a proof of production – that last spin is important to the repeatability and consistency required in production.
- Companies assume the Product Development (PD) group knew and thought about manufacturability during the design phase. Or they assume the manufacturing group knew and considered product design during manufacturing phase. In fact, it’s important the design is not done in isolation. Many manufacturing risk mitigations can be incorporated early in the design, but can be difficult later on.
- There isn’t a dedicated experience point person driving the production transfer effort. An experienced leader is required to guide PD and manufacturing teams and lead them towards the goal of transitioning to volume production.
A systematic New Product Introduction (NPI) process addresses all 3 root causes. The NPI process starts by assigning a single leader, who is experienced in product development, manufacturing and the phase gate management process. The NPI leader drives the production transfer process by coordinating the various activities between groups like PD, supply chain, planning, production and QA using the phase gate management process to ensure there is a seamless transition between the different phases.
For a production transfer to be successful
Upstream, the product design needs to be Designed For Manufacturability (DFM) and have low variability. Downstream, the different groups within manufacturing need to have well defined and completed Device Master Record (DMR) and Design History File (DHF) packages provided to them so they can simply execute the manufacturing process instead of inventing them.
The NPI leader uses their expert knowledge in fabrication process, DFM, and LEAN to help the PD design team design products that are high yield low cost starting at the proof of design phase. They will use strategies like poka yoke and BoM part count reduction, design for z-axis assembly, and matching design to suitable fabrication process capability. Devices or components destined for offshore need to be designed with this in mind (think sheet metal gauge versus metric sizes) and controls set in place. The NPI leader implements these DFM strategy throughout the different design phases with the PD team to ensure manufacturability is fully integrated into the design.
As part of the iterative phase gate design process, proof of product prototypes will be built to verify the manufacturing readiness of the design prior to commencing the production transfer.
While the iterative design phase gate process is being completed by PD, the NPI leader will drive manufacturing readiness activities with the manufacturing groups. These activities include creating work instructions and updates, jig & fixture design with PD team, supplier selection and procurement planning with the supply chain team, first article inspection (FAI) and incoming quality control (IQC) with the receiving team, training and production validation with the production team, and Process Failure Mode Effects Analysis (PFMEA) and manufacturing risk review with the entire PD & manufacturing group. The NPI liaises with various departments, pulling their input at the required moments to develop a cohesive and comprehensive launch plan. This allows the PD team to focus on technical design and the manufacturing team to focus on executing production processes.
Having a dedicated NPI leader drive design transfer to production using a phase gate process will ensure production transfer is a focused effort that is executed systematically, and not just an afterthought when the design is completed.
Henry Ho is an NPI Engineering Manager. He is passionate about successful production transfers as part of NPI. This is his first blog for StarFish Medical.
Images: StarFish Medical