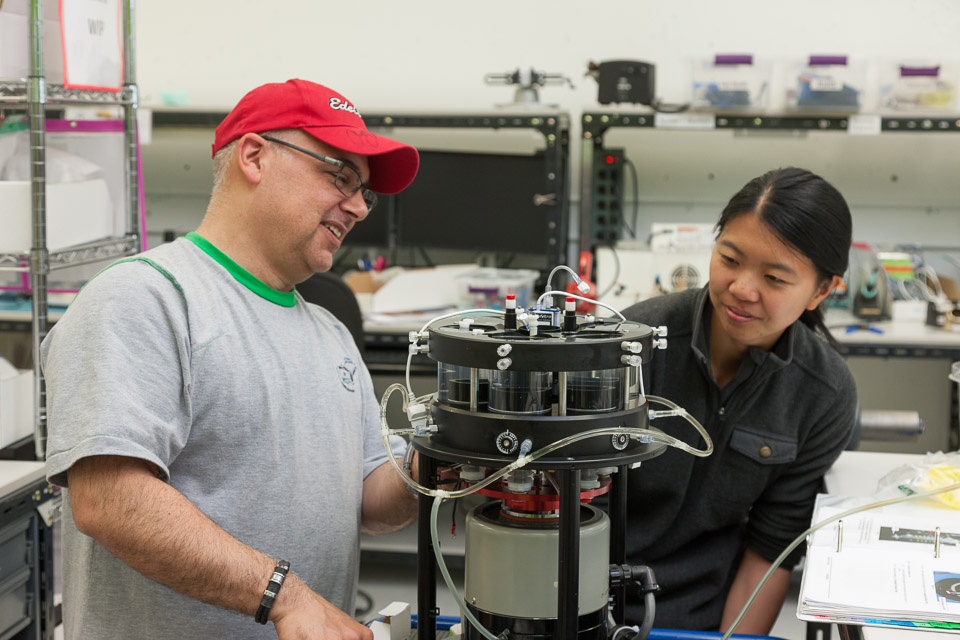
Why an early PFMEA is important
It behooves designers to look at the assembly processes early, with a focus on how we can stop critical faults or those that are likely to happen. Process Failure Modes and Effects Analysis (PFMEA) is a tool to assess potential process failure points during assembly and how the failures could be felt or observed by a customer. A ‘customer’ is not just an end-user, but any further user in the production line, or anyone in between.
The Design FMEA, referred to as DFMEA, supports the design process at the system, subsystem, interface, and component level to reduce the risk of product failures.
A PFMEA steps through the causes of the process failures, how often they occur, and how the causes could be detected. It assumes that all the parts are correct and focuses strictly on process failures in assembly.
There are three main questions:
- Is there a design element that prevents the cause from occurring?
- Is the cause detectable (and therefore the failure mode prevented)?
- If we can’t detect the cause, or prevent the occurrence, can we detect the failure mode?
Part of the analysis looks at the severity of the effects. Coupled with the detection and occurrence, it ranks the risk associated with each failure mode, the “RPN” score. The goal is to identify those processes which have higher risks to safety, efficacy, or affect the cost of manufacturing (e.g. while a process might not generate any safety risks, it may generate an unacceptable degree of scrap).
Any Risk Assessment (per ISO 14971) of a medical device typically focuses on the failures and effects only, and as such, the PFMEA is a support tool for the Risk Assessment. But a similar philosophy exists: scores should be reduced as far as possible, with mitigations in place for those risks deemed unacceptable. Once scored, mitigations are implemented, and the risk scores re-tallied under the new detections (or preventions).
So, back to the original question: why is an early PFMEA important? Of the detection methods listed, only the first one can be mitigated through design and actually prevents the cause from occurring. The other two require either the failure mode to be detected just before it happens (detecting the cause), or the failure mode has occurred, and the failure mode is detectable.
Rather than detecting causes or the effects of failures, preventing causes is the preferred approach, and needs to be incorporated into the design. If the device has been sent to clinical trials or IEC 60601 testing, or if the device has been through verification, it may require very costly repetition of testing. The required mitigations must be incorporated and validated to confirm the manufacturing process is not generating unacceptable safety or other risks. The sooner these design changes can be incorporated into the design, the cheaper it will be to absorb the changes.
Practically speaking, we can’t always design prevention into a device. The Risk Assessment is a living document, and the PFMEA is a great tool to keep the manufacturing section of the Risk Assessment up to date.
Dana Trousil is a StarFish Medical Mechanical Engineer. He has successfully launched many New Product Introduction devices, with experience in a variety of processes.
Images: StarFish Medical