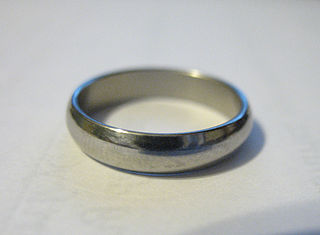
Honing Your Engineering Expertise
May is a wonderful month– full of new beginnings, longer days, more opportunities to hike and kayak, and our future– new graduates.
I had the pleasure of presenting the keynote address for the University of Victoria Engineering Students’ Society Industry Social Event in March. It gave me a chance to reflect on my days in school and lessons learned in the years since, both in and out of the medical device industry, and I’d like to share them with you.
Engineering Expertise
Here’s some of the things I’ve learned about engineering and honing one’s engineering expertise since graduation:
• Engineering school didn’t teach me how to be an engineer. In my first job I worked in lithium battery development and manufacturing. I realized very quickly how little I knew about the practicalities of machine design including materials, tolerances, standard parts and fasteners, design for machining. Some days I felt like a baby. Fortunately I had great people to learn from about design, manufacturing, machining and quality control. Learning from them was a huge second step in my education. Since then I’ve had to learn all about anatomy and physiology and the medical device industry. Learning is a constant.
• Technical problems don’t go away. You don’t get to hand in your assignment and move on. In one early case I was assigned a job of reliably removing metal tabs from batteries on an assembly line. I told the assembly techs I’d be done in a couple of days. Six months later after trying a variety of solutions it was still not reliably solved. Now I realize that solving tricky problems can take a long time. Over time you develop a sense of what smells like a tricky challenge and you can decide whether to engage or to find an easier way.
• It’s all about initiative. When you’re at school you learn how to anticipate the test questions and how to do what’s expected of you. In my experience the success of your career will largely depend on your ability to take initiative, which in some ways is the opposite of what you’ve been taught for the past 16 years. If you’ve always chafed at the structure of school and the game of marks you’ll probably like what you find in the real world.
• The importance of role models and mentors. I was lucky to have strong role models early. My manager Alec Rivers-Bowerman at Moli Energy was a great one. I’ve been equally lucky in the world of medical devices both on the technical and the business sides.
• Horses for courses. One big thing I’ve realized over time is that you need different kinds of people to make a project successful. For example, there are Innovators and there are Implementers– the Yin and Yang of engineering. Innovators love ambiguity and figuring out solutions to blue sky problems. Implementers like to have a better defined scope and get the details right within that. They tend not to respect each other very much, however, both are necessary to get the right product with the right reliability. Be what you are and leverage your strengths. I’m more of an innovator. Don’t ask me to spend the time necessary to get all the details right. (Ed. Note: Don’t be fooled. He’s pretty good at remembering details.)
• Project work was probably the most useful learning experience I had at university. Those projects were where all the theoretical knowledge came together into practical decision making and teamwork. I was lucky to have a chance to work on systems for telepresence and for automatic analysis of laser welding flaws with some great people which both won student awards and created the foundations for successful project work ever since. Being respected and trusted as a good team member is just as important as your technical skill.
• Most real technical challenges can be explained in about a minute. My wife used to laugh at the diversity of projects I would talk about and question whether I could really bring useful expertise from eyes to knees to spine and from lasers to ultrasound. One thing I’ve learned is that if you’re not afraid of technical problems you can understand them. Of course meaningfully solving and implementing solutions requires much deeper expertise but it starts with not being afraid to engage.
• A prototype and a product are vastly different things, especially for medical devices. I was lucky to start in a production facility making hundreds of thousands of units per month. There the huge gap between a prototype and a robust product smoothly flowing through manufacturing became very obvious. I got a chance to learn about Design for Manufacture and Assembly (DFMA), Design for supply chain, and Statistical process control (SPC) for example and have carried those lessons into the rest of my career.
• The importance of ID. When I graduated from university I had never heard of industrial design. When I think of it now it seems crazy. Industrial design is the human side of design; things like Interaction design, ergonomics human factors, workflow, UI, and human-centric design. I was lucky in an early job designing audio speakers to have the opportunity to learn about this critical element of successful design. Now, in medical devices there are specific standards that require ‘usability engineering’ to be implemented.
• No engineer is an island. Engineering education can be very hierarchical and we can tend to respect others based on their technical and analytical abilities. It takes a while to realize that those people who studied accounting and law and business are pretty smart too. To be successful as an engineer you need to work well with them and respect their abilities.
• Risk management and decision management. One of the big differences between junior and senior engineers is their understanding of where to put effort and how to manage decision making. In one sense we’re risk managers. We open up trees of possibility and then methodically work to an optimal solution while maintaining appropriate ambiguity.
I recall spending a month as a junior engineer on a battery durability test only to realize I had implemented the wrong protocol and solved the wrong problem. Years later I learned that my boss used this story as an example to train junior engineers on what not to do.
• We engineers undersell ourselves. We’re working on the core technical issues of the company. Often the whole success of the enterprise depends on what we do. In fact we’re working on business problems. If we understood that the problem set is much bigger than the purely technical we’d be more powerful. Sometimes we have to ask bigger and better questions of the right people to get a fuller picture of success. In medical devices getting the product right requires getting the usability, clinical workflow, manufacturability, serviceability, regulatory path and the price right for starters. That’s a lot bigger problem than getting the ultrasound pulse energy right. Even if you are working on the details you’ll make better decisions if you understand the big picture.
• Great engineers have a knack for getting to the heart of the problem. Fundamentally it’s not about saying smart things, it’s about solving the right problem. If you have that knack you probably know it already and it will be a huge asset to you.
• Engineering can be a great adventure. We get to figure things out that nobody has done before and make useful new things that change peoples’ lives.
In summary
After 25 years I love what I do. I get to work on really interesting and important problems every day and work with smart and inspiring people. I wear my iron ring with pride and hope you will too.
Scott Phillips is Founder & CEO at StarFish Medical. Scott holds a degree in Engineering Physics from the University of British Columbia. Under his leadership StarFish has grown into a diverse professional organization with clients around the world and 100% focus on medical devices.
The Iron Ring image is licensed under the Creative Commons Attribution-ShareAlike 3.0 License.
Check out this blog for engineering students to gain quality, hands-on experience.