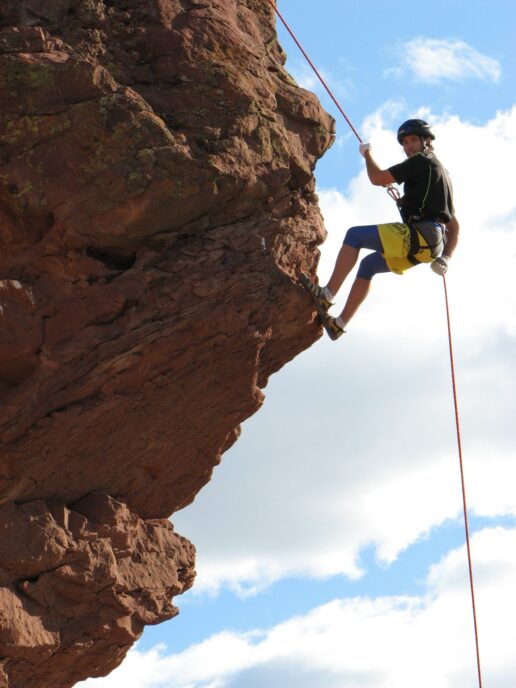
Extreme Risk Management in Medical Device Development
We take risks every day, often without realizing it. From crossing the street, eating new food, accepting a new assignment, using power tools, to saving important data on the network, we accept the possibility of an adverse event. Some risks require little more than an awareness of them, while other require in depth reflection – think of long term relationship commitment, company start-up investment, or medical device design. Any risk that may affect someone’s quality of life or safety is worth considering.
Device risk management is a serious business in the medical device development industry. Safety of patient and the operator must be proven beyond doubt for a medical device manufacturer / distributor to be able to sell. Medical device designers are required to follow a rigorous quality management system (QMS) documentation for the design history file (DHF) which includes a comprehensive risk analysis. The process is clearly defined as per national standard CAN/CSA-ISO 14971 Medical Devices – Application of Risk Management to medical Devices. The new 3rd edition of IEC 60601-1 testing and certification also mandates an elaborate risk management file consisting of an in-depth risk analysis and risk report. All possible hazards affecting the patient or the operator, and issues affecting the effective and safe operation of the device are considered.
For each medical device concept in development, a team of domain experts reassemble around a table to identify design risks and score them based on probability of failure mode, severity of consequence and detectability of the problem. A design solution or mitigation is developed for every risk scored assessed as high risk. The same review of the risk, but in combination with the mitigation design solution is re-scored to ensure that all potential hazards are removed. Along with the product requirements, the design mitigations guide the design and lead to the elaboration of specifications. During the design cycle, product manufacturability is considered and another series of risk identification is done at the transfer phase.
Manufacturing risk management is done during transfer to manufacturing upon closing the design phase. Mainly, it consists of asking a series of questions to ensure that the manufacturing of a newly designed medical device goes smoothly. Can parts be misassembled? Can components or steps be missed? Do we need a new fixture to ensure consistency in the bonding process? The whole point of manufacturing risk identification is to develop mitigations before risks turn into issues that may affect quality of the production run and ultimately causing reduced yield and decrease in profitability.
In addition to device and manufacturing risk management, medical device design engineers manage project risks throughout the development cycle. Project risks are identified right from project kick-off and throughout the project. StarFish works closely with clients to identify business and market risks in addition to technical ones. All project stakeholders are encouraged to participate and discuss project risks such as critical suppliers not shipping on time or a system being over-designed and too costly to built. What about if the technical lead get sick? What about if the device is too sensitive or fragile to ship internationally? These are all aspects of the project that need to be reviewed, addressed, and controlled. StarFish is moving towards a more robust project risk management approach to ensure timely closure of projects and an assurance of project success within budget allocation. The approach is not foreign to any seasoned project manager, but to the highly technical and cutting-edge medical technology designer, the basics of a well managed project is often overlooked and reduced in importance. Not anymore. A proactive project manager will also be on alert for project opportunities whether related to component bulk purchasing, material recycling or process consolidation.
So, between device risk management, manufacturing risk management, and project risk management, medical device clients will be able to enjoy a smooth product development ride and be assured that the likelihood of issues is minimized. For once, it pays off for the device development team to be negative and be on the lookout for anything that can go wrong. Success is the goal.
Martine Janicki, PhD, PMP, is a former StarFish Medical Senior Project Manager and Senior Director, Technology Operations & Facilities at Simon Fraser University. She was the first StarFish Medical PMO and her initial work on StarFish project management systems and philosophies continue guide our product definition and development.
Image: freeimages.com