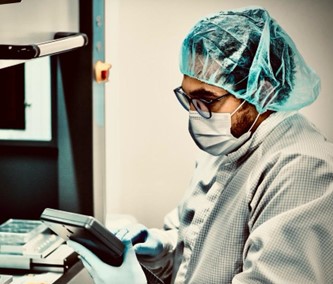
Validating Filter Integrity for Biopharmaceutical Manufacturing
Alternatives for Assessing Filter Integrity
Biopharmaceuticals are highly complex and regulated products. Single-use (SU) sterilizing grade filters are used to ensure that everything entering the process stream meets GMP requirements to maintain a low bioburden process and ensure final product sterility. Non-integral systems result in product loss, quality issues, time delays, increased costs, and potential safety hazards. Therefore, manufacturers usually provide practical controls, such as visual inspection and integrity testing, in their validation guide for SU components.
This blog discusses the importance of filter integrity and explores the relationship between microbial retention tests and integrity tests. These tests are essential for validating the effectiveness of filters in critical applications.
The largest segment of the Biopharmaceuticals market is antibodies and antibody-derived molecules derived from living organisms, which possess targeted efficacy and high potency for personalized medicine. For instance, monoclonal antibodies (mAbs) can be used as a targeted anticancer agent to boost the body’s natural immune system to suppress cancer cell activity. They are a promising treatment option for different diseases, including cancer, autoimmune and chronic inflammatory diseases.
More than 100 mAbs have been approved by the US Food and Drug Administration (FDA) for treating various diseases. These products require specialized manufacturing processes, quality control measures, and regulatory oversight to ensure their safety and efficacy. Their manufacturing process begins with upstream processes that include the cultivation of cells (the production agent) in a bioreactor, followed by downstream processes that involve the recovery, purification, and characterization of the final product.
Cells are cultivated in a bioreactor under certain conditions, including temperature, pH, and nutrients, to optimize and control the production of the desired biologics. Bioreactors should be designed to maintain sterility by selecting easily sterilized materials, incorporating effective sterilization methods, and ensuring proper sealing to prevent contamination from unwanted microorganisms.
Microbial Retention Test Correlation to Integrity Tests
The integrity of filters is crucial and significantly impacts the final product’s quality, especially in those applications where product sterilization or microbial bioburden reduction is required. Per ASTM F838-05, a sterilizing-grade filter is one that is capable of retaining a minimum of 1 × 107 CFU of Brevundimonas diminuta per square centimetre of effective filter.
ASTM F838-05 provides guidelines on the ‘Standard Test Method for Determining Bacterial Retention of Membrane Filters Utilized for Liquid Filtration. This method, known as the Bacterial Challenge Test (BCT), is a benchmark that most manufacturers must undergo on multiple filter samples to determine the filtration efficacy in terms of a log reduction value. However, the BCT is inherently destructive, time-consuming, and cost-prohibitive. Therefore, the SU industry has significantly improved non-destructive leak and integrity testing technologies for sterilizing grade filters that can be correlated to destructive BCT, used as a threshold for validation purposes, and documented within the filter documentation.
Liquid Integrity Tests Physical Principle
Different integrity test methods have been developed to verify the performance of wettable microporous membrane filters, including bubble point, diffusive flow, pressure hold/decay, and water intrusion (Hydrophobic-specific). Bubble point and diffusive flow are the two principal integrity tests that can be performed manually or using an automated test machine, which is often preferred to eliminate the subjectivity of manual operation.
The pressure hold/decay test is a variation of the diffusional airflow testing method. Apart from water intrusion, the main physical principle for the other integrity tests depends on the concept of surface tension and capillary action between the liquid and membrane material that prevents gas from flowing through the wetted membrane without a particular differential pressure.
When a microporous membrane is properly wetted, the pores become filled with the wetting fluid, such as water, by the capillary action. The bubble point pressure is the minimum air pressure required to force the wetting fluid out. The flow before this point is referred to as diffusive flow, and beyond is referred to as bulk flow. The bulk flow initially takes place through the largest pore with the minimum flow resistance, where it is easier to overcome the surface tension forces. Consequently, the bubble point pressure is typically utilized to gauge the largest pore size of a filter. The smaller the pore, the higher the pressure required to clear the pores of the wetting agent, and vice versa. For details on how to perform the bubble point test, ASTM F316-03 provides guidelines for conducting the ‘Standard Test Methods for Pore Size Characteristics of Membrane Filters by Bubble Point and Mean Flow Pore Test.’
The diffusive flow test relies on Fick’s law of diffusion, which states that the rate of diffusion of a substance across a unit area (such as a surface or membrane) is proportional to the concentration gradient. Therefore, if the air pressure applied upstream of the filter is lower than the bubble point, gas molecules will dissolve in the liquid retained within the membrane and diffuse to the downstream side.
The diffusion rate can be detected using a mass flow meter or by monitoring pressure decay on the upstream side of the membrane and using the ideal gas law, which, in this case, will be a pressure decay test. The diffusion rate is directly correlated to the integrity of the filter; a higher diffusive rate indicates compromised filter integrity, as it suggests larger pores or defects that allow for increased gas flow.
When to Integrity Test
Sterilizing grade filters are usually designed according to a stringent risk management tool, Quality by Design, for integrity assurance. Filters intended to sterilize a liquid should still be tested pre- and post-use with a non-destructive integrity test. The non-destructive test must be correlated to the bacterial challenge test during the validation phase. Where applicable, following a thorough risk assessment, it is recommended to conduct a Pre-Use Post Sterilization Integrity Test (PUPSIT) on the filters before use to verify that no damage or loss of integrity occurred during the sterilization process before use. The post-use testing must be performed to ensure that the filter has not been subjected to any damage during its operation.
Summary
The future of biologics development is full of potential breakthroughs in treating and possibly curing many once-untreatable diseases. Sterilizing grade filters play a crucial role in ensuring the quality and efficacy of these products. Maintaining filter integrity is critical. Testing methodologies, such as bubble point, diffusive flow, and pressure hold/decay tests, offer a reliable, cost-effective, and non-destructive alternative to the BCT for assessing filter integrity pre- and post-use.
Khaled Youssef is a Bio Services Engineer at StarFish Medical with an academic background that includes a BSc and MSc in Mechanical Engineering from Egypt, a Ph.D. in Mechanical Engineering, and a graduate diploma in Neuroscience from York University. His work has covered the development of microfluidic devices for neural and behavioural screening of living organisms, innovative materials for health and safety applications like smart bandages for chronic wounds, microspheres for bacterial isolation from water sources, point of care diagnostics development, and tissue engineering.
Khaled’s research and R&D experience resulted in over 30 publications (hindex=10) and one patent. At StarFish Medical, Khaled applies his engineering and life sciences expertise to support Bio Services projects in different capacities, including microfluidics, systems, and mechanical engineering, and as a research scientist.
Biocompatibility is a significant aspect of contact, but what about sterility? And if a device does not need to be sterile, then how clean does it need to be?