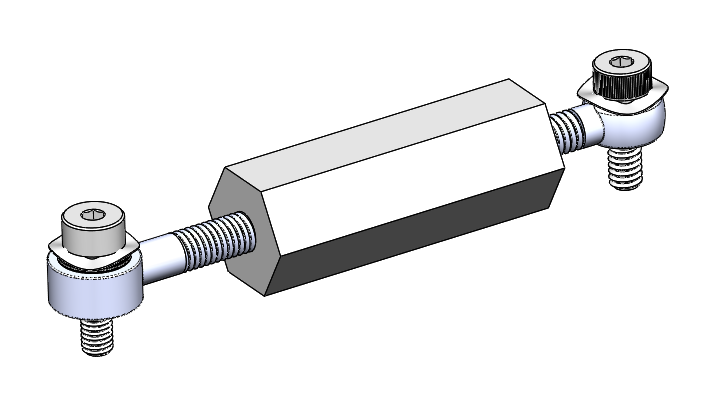
How to construct a custom differential screw
Understanding a differential screw and how to construct one
I recently had to construct a custom differential screw when designing a precision test fixture for one of our medical device projects. We used it to locate a test piece within +/-0.03mm. This motion required minimal force, and each part required a set of specific locating features. There are several options available to produce this motion, but due to the configuration and location features of our test piece, we pursued a custom solution using a differential screw.
Illustrated below, a differential screw contains two right handed threads of different pitches (A and B), a traveling element ( C ), and a fixed frame (D). For each revolution, the threaded shaft extends from the frame by the pitch of thread A (1.75mm), and the traveling element C is retracted by the pitch of thread B (1.5mm). For one rotation of the screw, the traveling element only moves by the difference in thread pitches (0.25mm). This allows an effective thread pitch that would be impractical for a single thread, and can provide a mechanism that has both precision and strength.
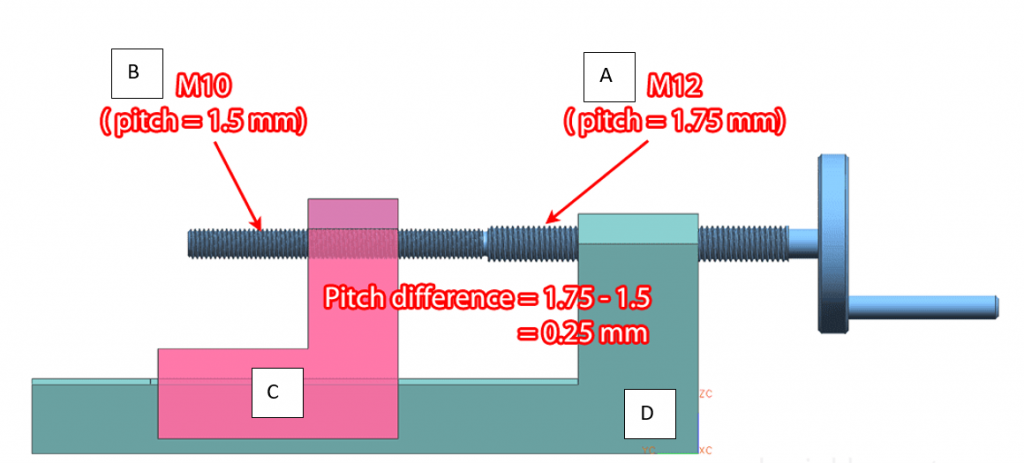
Differential screws are available as off the shelf units and integrated into manual stages. Unfortunately, the available options did not integrate well with the constants of our test fixture. In the end, we decided to design and construct a custom differential screw that was relatively inexpensive and easy to integrate with our system.
In our application, we used a combination of metric and imperial threads to get a slightly tighter effective pitch. A 5/16-18 thread paired with M8x1.25 thread provided an effective pitch of 0.16mm/rev. With this effective pitch, we only needed to rotate the mechanism within +/-67° to achieve a linear position of +/-0.03mm.
We used a custom nut spinning between two threaded rod ends to make the differential screw, and mounted the assembly with shoulder bolts, shim washers, and wave springs. The only custom part was a length of 1” hex stock with drilled and tapped ends. The hex stock was manually rotated to adjust test piece position, and a load cell provided position feedback.
Using off the shelf fasteners resulted in significant play when reversing the direction of travel, so the system required a constant force spring to keep the threads under constant tension. Differential screws also require the threaded element to travel by the larger thread pitch for each rotation. As a result we needed to make a relatively long test fixture to accommodate the screw mechanism. (See illustration of our example at beginning of article.)
Overall, choosing to construct a custom differential screw was a simple way to provide precise motion with manageable drawbacks.
Aaron Philippsen, is a StarFish Medical Mechanical Engineer, and recipient of the company’s Chris Denny Memorial Award for Innovation. You can watch Aaron in our Biotech Platform Design for Novel Medical Devices video below.