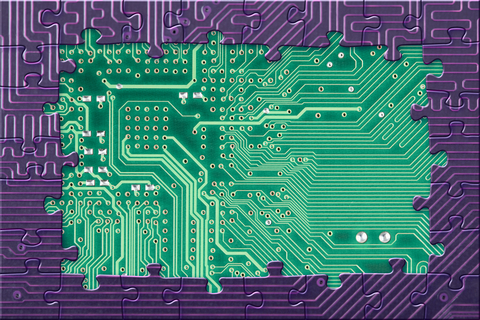
6 Tips for designing a medical device PCB prototype
Designing a printed circuit board (PCB)? Is it for a prototype? I’m a Junior Electrical Engineer at StarFish Medical. This article summarizes some of the things that I’ve learned since I’ve been here. It is intended to serve as some words of advice to the novice PCB designer. The focus is on medical device PCB prototypes, but some of the information here is also applicable to more mature designs. For more PCB design best practices, check out these blogs from Kenneth MacCallum.
Design with modifications in mind. For a first board spin, you’re kidding yourself if you think that everything is going to work the first time. I know a senior engineer who says that he’s done this once. My first rule of thumb is to make sure that all traces are accessible from the top layer. This makes them easy to cut, scrape away solder mask, and solder to. The second is make vias and test points large enough that you can easily solder jumpers to them if you need to. While modifying boards, components that are placed too closely together can make modifications difficult. Putting extra space between components can help with this, so when you’re doing your layout, feel free to use up the entire board.
Design your board so that it’s easy to test and debug. On the subject of things not working the first time, Add test points. Lots of test points. Put them on your signal traces, put them on the output of your power supplies. Put them everywhere. Many times I’ve found myself wishing there was a test point on a particular trace. I’ve never found myself wishing that there wasn’t one. Also, if you keep the test points (and as many components as possible) on the side of the board that is exposed while the board is installed in the assembly, testing will be much easier.
Recycle your old circuit. Is there a sub-circuit from a previous design that perfectly suits the needs of your current project? Consider saving time by re-using a sub-circuit from a previous design. Switching power supplies are a good example of circuits that are often easily transferable from one design to the next. It can be tempting to design everything from scratch, but it’s often best to avoid doing things twice if you don’t have to.
Put down the footprint(s) for the component(s) that you aren’t sure you need just in case. Is there a component or sub-circuit that you think you might need, but you’re not sure? For instance if you think that maybe an RC low-pass filter at a certain analog input is a good idea, but you don’t know if it’s necessary, you can easily leave out the low-pass filter and put a zero-ohm resistor in place of an actual resistor to avoid having an open circuit.
Most of the time, more copper is better. I generally put a ground plane on all layers. Stitch your ground planes together with lots of vias. If you have both analog and digital sub-circuits on your board, it’s best to split the ground planes to minimize the noise that the digital circuits will impart onto analog circuits.
Don’t forget to design for ease of assembly and serviceability. You’re placing components and meticulously routing, routing, and re-routing. After that, you’re re-routing some more. While you’re paying attention to a myriad of minutia, it’s easy to forget the things that are most obvious to the people who will actually be assembling, taking apart, and re-assembling your device (even though it’s entirely likely that you’ll be one of them). Are your connectors arranged so that a human hand can reach into the assembly and mate them to their cables? Do pads connected to ground fills have thermal relief connections to ease solderability? Have you exported a 3D model of your board to do a virtual test fit in the assembly? Where are your components placed?
My biggest serviceability nightmare was when I made the mistake of using screw terminal blocks for several connectors. This saved time in initial assembly (no crimping!), but meant that every time the board was removed for debugging, every terminal had to be unscrewed. Every time this happened, I wished I’d just crimped together some cables and used Molex connectors (or anything other than terminal blocks).
This article is intended to serve as a non-exhaustive summary of things to make your life easier when you’re designing a medical device PCB prototype. I hope you’ve found it useful.
Kristofor Dolberg is an Electrical Engineer. This is his first blog for StarFish Medical. Kris is a graduate of the University of Victoria where he was part of the ECOSat team that won first place in the Canadian Satellite Design Challenge.
Image: 11990740 © Pzaxe | Dreamstime.com