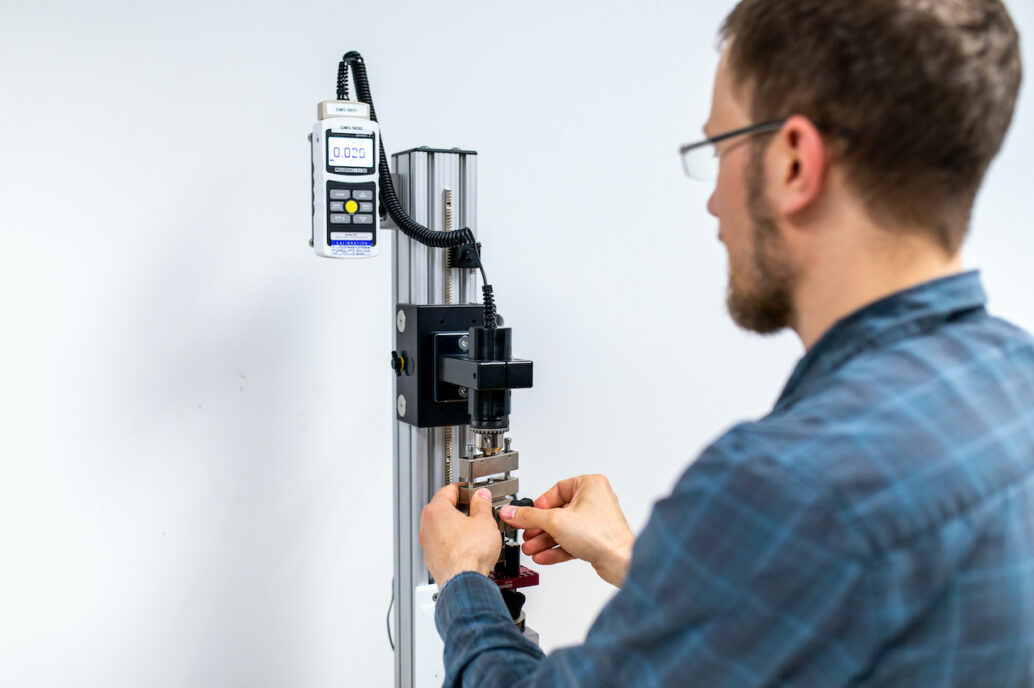
Rushing to the Wrong Product (implementation)
A few months ago I wrote a blog on the most common causes of getting the wrong product based on the career experiences of our senior staff. I focused on the product definition process. Today I’d like to focus on wrong product implementation and launch parts of the process.
As before, it’s a given that entrepreneurial companies are always resource and time constrained. Some stern advice to do everything perfectly is not helpful and that is not the spirit of this post. The interesting question is where to focus. Here are some examples:
Wrong Product Implementation : See Standards as Bureaucratic Hurdles
If you see the standards as pylons to avoid, you’re doing it wrong. I believe that if implemented well, ISO 13485, and FDA QSR, are lifesavers for an entrepreneurial company.
We sometimes see companies that consider risk and failure analysis minimally or too late in the process to do anything about it. Also we have seen cases where design reviews and gate reviews were not meaningfully performed, or where verification testing wasn’t linked well to the specification, all with costly and risky consequences. These design control processes are designed to save you money and heartache later.
Also remember that design control can’t be whitewashed on later – it’s fundamental to the operation of the company during development.
I have other more complex views on how IEC60601 ed3 was foisted upon the industry, but that’s a story for another day.
Wrong Product: Premature Optimization
There is a reason why formal design methodologies call for a sequence of improved prototypes – typically from Proof of Concept to Alpha to Beta to Pre-production leading to a production device. In the early stages the big configuration and product feature risks are being managed. In the later stages the cost and manufacturability are the focus. If you attempt to roll them all together you’ll just spend time and money optimizing the wrong things.
Wrong Product: Design for Manufacture and Test Not Considered Early Enough
This one is obvious but it’s still amazing how many times our people have seen issues where, for example, test points aren’t added to circuits, assembly steps can’t be reversed, in-process measurement points can”t be accessed, required precisions are too high for the processes specified, etc. In our process manufacturing, people and questions are included as early as the product definition gate review.
Wrong Product: Insufficient Testing
When I look back on the many products I’ve been involved with in my career and I think about some of the early product issues, it’s clear that most of them could have been avoided by more testing. For example, we had a case where a battery in a 3rd party module self discharged in two weeks causing out of box failures and expensive service support. This particular product had been rushed to an early launch based on a trade show (ever heard that before?). In retrospect, we had never tested the product for long enough in the field to discover this issue.
Wrong Product Implementation: Poor Manufacturing Transfer
It’s always tempting to assume that the beautiful beta prototypes that worked so well in early validation can be rapidly pushed into production. In truth there’s a lot to be done to audit critical vendors and implement, document and validate manufacturing processes and get the packaging and shipping validation resolved. If you want a reliable repeatable product built by real-world manufacturing technicians, you have to do these things well.
Wrong Product: Launch Strategy/Post Launch Not Planned
In almost every case where a novel product is launched there will be some fine tuning of the features and functionality of the product based on early market experiences. Some budget must be assumed to allow fixes and improvements to be implemented, tested and rolled into controlled manufacturing. Sometimes companies assume that they can cut all development expenses on the day after shipping unit #1 and are left with difficult choices when that turns out to be wrong.
And there you have it. I welcome your stories and comments. Feel free to email me at sphillips AT starfishmedical DOT com.
Scott Phillips is Founder & CEO of STarFish Medical. He holds a degree in Engineering Physics from the University of British Columbia. Prior to starting StarFish, he worked in diverse areas such as lithium battery development and manufacturing, UV spectroscopy instrumentation and hi-fi audio speakers. Under his leadership StarFish has grown into a diverse professional organization with clients around the world and 100% focus on medical devices. Scott is a past Chair and current member of the LifeSciences British Columbia board, member of the 2022 VIATEC Board of Directors, Fellow of The Canadian Academy of Engineering, winner of the EY Entrepreneur Of The Year™ 2017 Pacific Awards Technology category, 2017 recipient of the VIATEC Technology Champion award, and volunteers with Junior Achievement, Entrepreneurs Organization, and University of British Columbia.
Learn more: There are a number of safety implications to choosing lithium batteries as well as practical business implications.