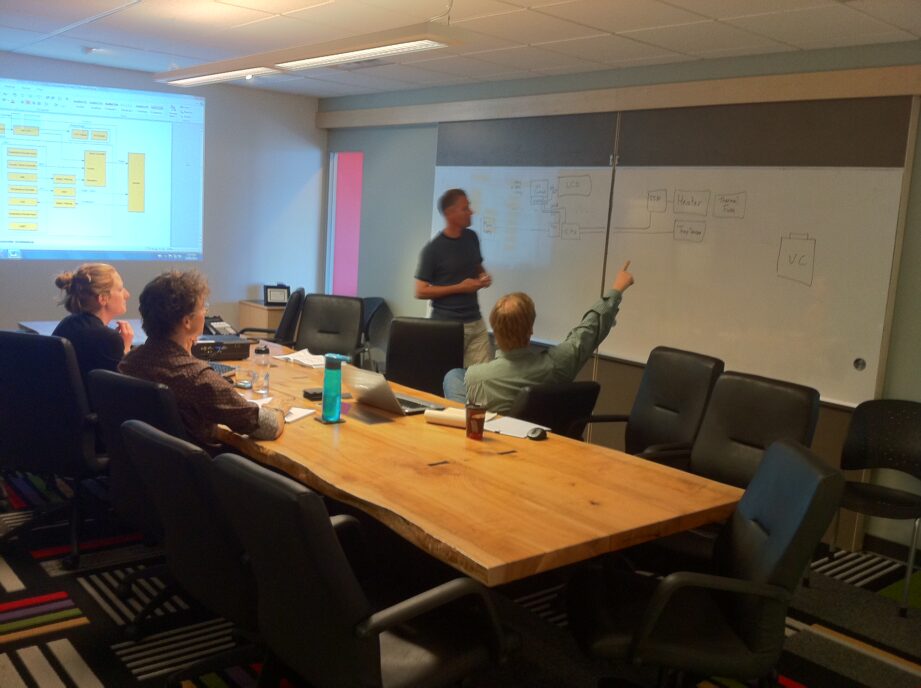
Sailing the Pacific and Medical Device Design Consulting
Things I Learned about Medical Device Design Consulting at the Boatyard
My partner and I have sailed long passages between islands in the Pacific in the past and plan to do so again. Spending weeks, even months, in locations far from machine shops, lumberyards and hospitals, it is important to be self-sufficient. Thus, any opportunity to expand our skills is embraced.
On dry land, however, having help to complete a difficult task is sometimes necessary; learning from that experience is even better. Last week our sailboat was on blocks in the boatyard benefitting from annual attention. As usual, some tasks were straightforward and others were complex. Painting the sailboat bottom is a ritual we can do with our eyes closed (it helps keep out the spatters), but correcting a bent propeller shaft is something new.
While some folks hand annual maintenance over to the yard’s experts, go home and return in a few days to a restored boat, we wanted to do as much ourselves as we could. So we took on most tasks, but employed assistance from the boatyard’s service manager, Simon. While this project unfolded, I mused on the many similarities between my current situation and those of my customers at StarFish Medical.
As with any medical device design consulting project, our first step was to assess the situation and plan what to do about the prop shaft. We engaged Simon to help evaluate the scope of the work. Like experts in any field, he had seen many similar situations and used that experience to guide his opinion on the magnitude of the work. Tasks that boat owners might face only once, an expert faces daily, and he or she has certainly encountered many ways of doing them right and doing them wrong.
In this case, he advised us to remove the shaft, send it out to a machine shop for testing/truing, and then fit it back in place[1]. Sounds simple, but project plans are like that; details are omitted for clarity and sometimes simply because they are unknown as of yet.
Professionals understand the client’s desire to save money and should be willing to advise which parts of a job can be done by the client. They can usually give an accurate assessment using their knowledge of the skills and tools needed for a given task.
After some discussion of our level of expertise, Simon suggested that we could extract the shaft, replace the cutless bearing, reinstall the straight shaft, perform the engine alignment, and reassemble the stuffing box. However, confirming the straightness of our 2m long stainless steel shaft to within 50 microns would best be left to a machine shop.
Once we dove into the work, we ran into complications. Readers who are boat owners or who have been through a few projects are likely nodding knowingly. The sailboat’s twenty-year-old engine mount nuts were seized and required several hours of work to free without destroying the studs they attached to. The shaft coupling, likewise, was firmly affixed to the shaft, adhered by corrosion over time. Specialized tools exist that ease jobs like these, but we improvised with what was at hand. This illustrates another point: Medical Device Design Consulting professionals often have tools, test equipment and techniques that help to make the job go faster. Had we been in more of a hurry, we could have engaged a mechanic.
Upon receiving the newly straightened shaft, we briefly consulted Simon on what the next steps were. It’s good to ask beforehand to avoid having to redo a job. We installed the straight prop shaft and then spent several hours adjusting the height of the four engine mounts so the strut, stern tube, stuffing box and engine transmission coupling were all aligned.
Our target was to have the couplings mate and be parallel to within about 70 microns. Near the end of the day we achieved what we considered a good alignment. Ascending and descending the ladder during each set of adjustments to compare results inside and outside the hull provided a fitness benefit to the job.
For this particular project we didn’t need skills or resources beyond those of Simon and ourselves, but if we had, other boatyard personnel were available. An advantage of working with a Medical Device Design Consulting expert is that they often know other experts in related fields they can call upon if needed. We did use Simon to inspect our work before we finished tightening everything up.
While not mandatory in our situation, getting an independent assessment from a Medical Device Design Consulting firm or accredited test results at various stages in a project is a useful service. On the boating side, there are standards such as those by the ABYC (American Boat and Yacht Council) that experts would be familiar with; on the medical device side one can seek out experts in areas like US FDA requirements, Health Canada Medical Device Regulations and EMC (Electromagnetic Compatibility) standards.
One final thought on the benefits of engaging a boatyard’s services: access to the skilled workers (and Medical Device Design Consulting) is usually shared withothers. A wide variety of yachts occupy the yard – everything from multimillion dollar palaces to weekend racers – all of whose owners have one thing in common: Their boat is their highest priority. A good project manager understands this and will coordinate the services of the boatyard to ensure fair and full access to professional attention, and communicate with customers so they know what to expect.
It turned out that our adjustments to the prop shaft alignment were satisfactory. We learned some new skills and now eagerly await the relaunch of our sailboat. I hope your own spring and summer pursuits are enjoyable. If you have any comments or questions on either boats or medical device development or Medical Device Design Consulting, I would be pleased to hear them.
[1] Those of you who own boats will understand that this is a very high-level overview; many interrelated systems are involved. A prop shaft is only one part of the propulsion system that includes the engine, stuffing-box, stern tube, the strut supporting the shaft, the cutless bearing, and the propeller.
Bjarne Hansen is a former Electrical Engineer at StarFish Medical. He contributed to the design and development of novel medical products at StarFish and particularly enjoys designing embedded systems when not writing blogs while working on his boat.
Images: StarFish Medical