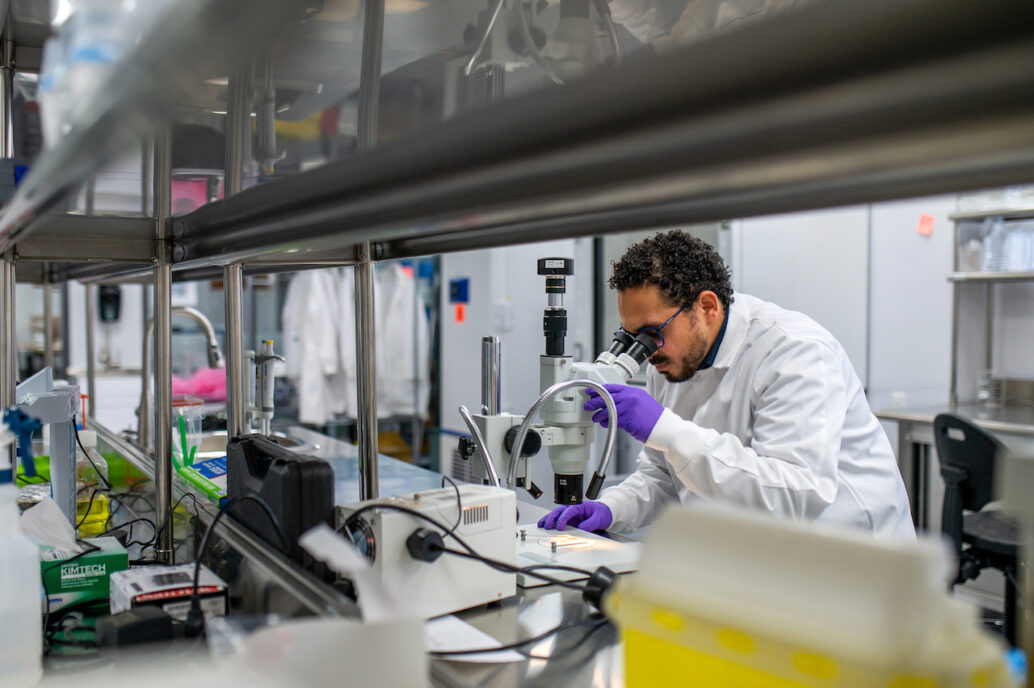
12 Steps to Set up a Biomed Lab
Some lab managers get to manage a running lab, but others get a whole new challenge of being a lab manager where there is no lab yet. Each phase to set up a Biomed Lab – from having nothing to having everything in operational condition – requires thoughtful decision making and involves professionals from various backgrounds.
This blog covers 12 steps to set up a biomed lab and make the process smooth.
When taking a leadership role in setting up a new laboratory space (on a budget), the process can be overwhelming and exciting at the same time. Opening a biomed lab is not just about planning a layout and placing equipment. It includes managing multi-layer organizational involvement all the way from facilities to the head of operations.
If you are starting a new lab from scratch, the first step is to fully understand the organization’s mission and business goals. This will have a direct impact on how you approach setup of the lab, and any purchasing decisions you make. It is important to understand how the new space might better accommodate upcoming work, and how it could contribute to future business goals as the organization goes through various changes.
Apart from a start-up organization, there are many scenarios in which you might find yourself managing a new lab setup. Perhaps you’re starting a new position. Maybe your lab has found a home in a new building, or your existing lab space has been renovated. Whatever the reason, it’s important to take an organized approach towards tracking what’s necessary to get the lab up and running smoothly. Here is a checklist of steps to follow when starting a new lab.
1. Explore the lab space and formulate a layout by considering:
- Containment level required and the need for biosafety cabinets or fume hoods.
- Dedicated space for larger instruments, such as fridges, freezers, and nitrogen tanks
- Bench space for equipment and workspace for personnel
- Storage space for both general consumables and biological/chemical agents
2. Licensing Needs
- Based on type of work to be carried out, make sure to apply for related licenses and certifications before construction/remodeling or finalizing the lab layout and materials.
- Investigate whether submitting a layout plan to authorizing and licensing body is required.
3. Review the lab layout with building management.
- Make sure to understand any building requirements and restrictions on use of the space that may require additional locks and door access for the lab
- Verify that electrical, plumbing, and waste lines are in place and meet lab codes
4. Review guidelines with safety officers
- Verify that containment hoods and biosafety cabinets can operate in compliance with standards and certification requirements.
- Consider having a working alone policy and emergency response plan in place. It is important review these even after lab set up is done and your project is operational
- Obtain verification to work with volatile chemicals, radioisotopes, and biosafety hazards.
5. Waste Disposal
- Order appropriate waste bins and containers to contain and transport projected waste
- Estimate the quantities to be generated and make sure to have adequate supplies
- Establish an account with regulating government authority and register all waste streams that will be generated.
- If not disposing waste yourself (In most cases), contact and set up contract with waste disposal companies that can come and take care of all bins and provide documentation to comply with regulations
6. Itemize and catalog existing lab equipment (if applicable)
- Evaluate limitations of existing equipment and explore upgrades if needed
- Offload or research storage options for unneeded equipment
- Catalog equipment information: make, model, and year; serial number; operation dates; calibration and service records
7. Identify any new equipment needed for the lab
- Explore equipment options and identify equipment sources and vendors
- Create budgets for the required equipment
- Obtain quotes from various vendors and purchase details along with lead times
8. Identify furniture needs for the lab for safety and ergonomics
- Assess ergonomics of workstations and equipment, including chairs, floor pads, and high-use items like pipettes
- Evaluate chemical resistance of benches
- Based on layout find out what sizes of benches are suitable and how many are needed that come with proper overhead storage.
9. Identify space, power, and access requirements for equipment
- Review equipment requirements for power, ventilation space and other features, for example -80°C freezer and fume hoods requires 20Amp outlet
- Be sure the equipment will be accessible and can be maintained and serviced as needed.
- Verify that requirements such as vibration or electrical isolation can fit in planned spaces
10. Check loading dock and equipment installation needs
- Review specifications of the planned equipment — weight and dimensions
- Check for any handling instructions — i.e. fragile or heavy
- Contact your facilities department to be sure there is adequate means for transportation from loading dock to lab destination; check doorway and passageway clearances
11. Review regulatory specifications and be sure the new lab is compliant
- Perform evaluations with key staff and resources to be certain of compliance with local, state, and federal regulations
- Regularly check to be sure the lab remains in compliance
- Keep records of any issues or changes
- Create logs for future audits; for example, waste disposal, cleaning and equipment maintenance
12. Create a master list of all equipment and consumables
- List all equipment along with maintenance schedules
- List all consumables and miscellaneous items with frequency of orders along with price and secondary vendors to make life easy in the future
Dealing with everyone and everything at the same time will require niche talents like budget prep, window shopping, convincing management on why and what is a needed vs wanted in a lab. All of this must happen while time is ticking to hit project deadlines.
Having an expectation that everything will happen on time is very unrealistic in this phase. Delays and issues are extremely common and WILL happen each day. A lab is often a must need when leading a new project or product development. Follow these 12 steps to set up a Biomed Lab to greatly smooth your journey and enhance your likelihood of success.
Disha Patel is a Research Scientist at StarFish Medical.