
Optics handling during manufacturing
Our Optics experts and manufacturing leaders met to identify lessons learned and tips from recent projects involving optics handling during manufacturing, prototyping and transfer to manufacturing. This blog features their tips and lessons for handling optics during the manufacturing process.
Minimize Contamination
There’s a reason why a lot of optics manufacturing is done in a Class-10,000 clean room: because dust is everywhere and it will collect on optics. Dust may not always cause a product to not work, but it will make it look bad.
Avoid cleaning whenever possible
If you’re not in a clean environment, any attempt to clean an optic is likely going to make it worse. That’s because having the optic out for cleaning in such an environment is going to – by itself – add dust. As a result, it’s a self-defeating process.
The cleaning process itself can weaken optical coatings, or a surface wipe can drag hard particulate contamination across the surface of the optic, leading to new scratches. There is always a danger of nicking the part with tooling that you’re using in the cleaning process (e.g. forceps used to hold lens tissue).
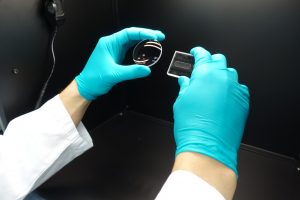
One exception is when you are inspecting for scratch/dig. Such an inspection is a “best practice,” not a functionality check, but it’s industry-standard. When you are inspecting for scratches and digs, it can be hard to tell them apart from dust. So if a process includes a scratch/dig inspection, you will have to clean the part before the inspection.
The level of cleaning documentation should be carefully considered. Every time you touch an optic, you run the risk of damaging it. There is a balance between too much documentation burden, and need for information on the detailed part history if there is an issue with that part in its lifetime. Any decision regarding the level of documentation needs to consider the question: what is cleaning? For example, does a dust off count as cleaning or is it just a standard preparation?
Depending on the criticality of the optic, or the optics that you’re manufacturing in general, consider requiring a “traveler” (a log that travels with each individual optic recording “touches”).
Never scrub if you can avoid it. Dust-offs or “drag wipes” are the first line of defense. If the dirt is so caked on that a scrub is required, it’s really at the “Hail Mary” point of “can I save this optic?” But once in a while, a scrub leaves the optic seeming better, somehow. However, sometimes the optic only appears better because the scrub has pulled off the optical coatings leaving fresh, bare glass!
Robustness is material-dependent. For example, titanium-sapphire crystals are extremely hard, with a Mohs’ hardness of 9. Glass is relatively robust. But any time there is anti-reflection coating, polarization or filter coating, you’ve got to be really careful. With a prism, if you need to clean it, you’re probably doomed and better off scrapping it.
Compare the labor cost of cleaning vs. the parts cost. If you are cleaning a part that costs a dollar or five dollars in volume, it may not be worth your time. That’s a decision every manufacturing floor, every product manager, needs to make for themselves.
Tips for manufacturing technicians handling optics
Optics are not like normal parts for manufacturing technicians. There are multiple levels and layers of handling practices. Here are key learnings discovered with our manufacturing personnel.
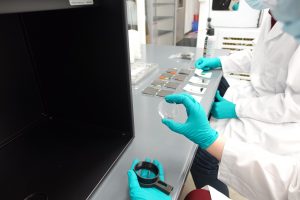
A big first step in training technicians how to handle optics is the clear aperture. Ensure that all technicians understand what it is, and get into the practice of only handling optics outside of the clear aperture.
Gloving is big hurdle to surmount. Technicians need to learn and understand proper gloving protocols.
Avoid bringing contaminants into the environment. Three great sources of contamination are the tools that you’re using if you don’t pre-clean them, your cell phone, and you yourself. If you end up touching within the clear aperture, you might think: “Oh, my pen isn’t actually dirty” or “while pushing my glasses up, I just pressed on the metal frame… It’s fine.” It really isn’t. You will end up with enough oil on your gloved hand to warrant a cleaning of some kind. People are oily and dirty and the things that they touch are oily and dirty.
Enter into a state of mindfulness. It’s really hard not to scratch your neck or your nose or your eyes. It’s subconscious: you don’t even notice you’re doing it. And it’s not the end of the world as long as you re-glove after scratching
Having the right tools is key – so is a manufacturing-friendly design
To minimize scratches from tools during assembly, ensure you have the correct tool. Buy a tool that’s made to order. That makes it a lot easier with less chance for errors. You can buy an adjustable tool that works for all lens retaining rings or special ones. We used a big universal tool and it had to be adjusted each time: if it wasn’t adjusted perfectly, there would be problems. The investment in buying the right size tool is really worth it. It’s like an adjustable wrench: you don’t want to use one for precision work.
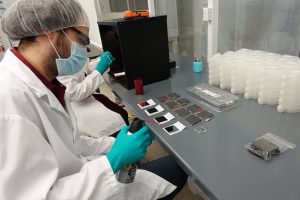
Similarly, invest in the correct inspection tools and standards: such as a light box and comparator slide for scratch/dig inspection. Trying to speculate on what counts as a scratch or judging by eye alone whether a scratch’s width is > 200 μm is foolhardy.
Make sure that you can use tools consistently without the risk of a tool slipping because it is being used at an awkward angle.
Design the process to limit the chance for failure at the assembly stages. Incorporate a “design for manufacturing” early in your design process. DFM isn’t a consideration optical design engineers typically think of unless they incorporate it into their methodology.
Once you have any sort of volume, and have locked in your design to be repeatable, you want to buy the right tool for the job. The tools are not that expensive. You only have to scrap a few lenses with coatings on them before you’ve paid for the tools.
Training
Training is key to successful optics manufacturing. A lack of training will be immediately noticeable through a spike in “non-conforming” parts. For specialized tasks such as scratch/dig inspections, invest in a good training course so that you can know exactly what you’re looking for (such as judging the scratch grade by the brightest part of the scratch).
Buy-in from your Manufacturing Technicians is critical. They will understand that a lack of training will lead to non-conformance report paperwork, and increased rework. Our technicians were very engaged in training because it’s making their lives easier. They’re gaining knowledge. They’re going to make more acceptable parts with less re-work. There’s nothing more annoying to a technician than having to rework devices for the same reason time and time again.
Invest in addressing the frustrations or difficulties of the different roles. When a project is quickly ramping up, there are many learning curves at different levels. Everybody is excited to partake in a training course that addresses their particular concerns.
We had quite a lot of discussion about understanding what meaningful specifications were for the optics and what quality specifications were. You want to empower the technicians to say, “Hey, there’s a problem with this.” Who has the training and who’s empowered to actually make the call? You want this to happen without spending too much cycle time.
We didn’t want to always turn to the engineers regarding what was acceptable or not. But without the training, we weren’t able to justify making that call on the floor.
Manufacturing optical products is a unique process which brings many challenges with it. But by investing in the correct, clean assembly environment, the proper tooling, and paying attention to appropriate training, bumps along the road can be smoothed out. Be mindful, and avoid cleaning whenever possible! We would enjoy hearing your experiences and perspectives on optics handling during manufacturing and transferring optically based medical devices into production. Contact us for a free, no-obligation 30-minute consultation.
Astero StarFish is the attributed author of StarFish Medical team blogs. We value teamwork and collaborate on all of our medical device development projects.
Images: StarFish Medical