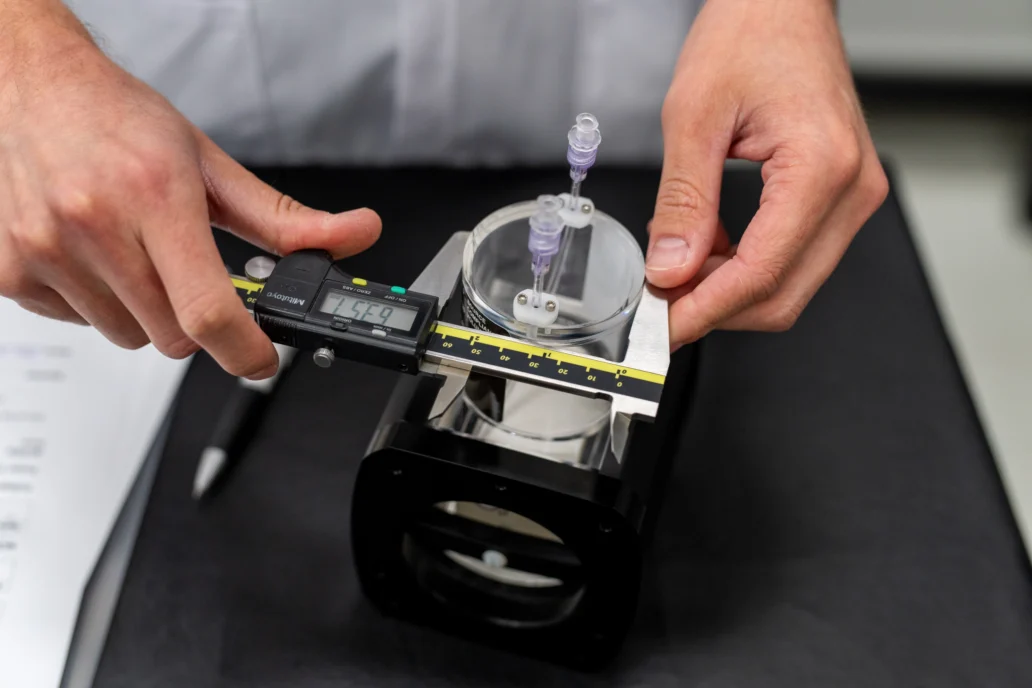
Test Method Validation in Medical Device Development
In the highly regulated world of medical device development, ensuring product safety, quality, and compliance is essential. One critical yet often overlooked aspect of this process is test method validation (TMV) in medical device development. Proper TMV ensures that the testing procedures used are reliable, repeatable and suitable for use. By validating test methods, medical device manufacturers can confidently assess product quality and maintain consistency throughout product development and manufacturing. This blog describe what TMV is, when it is required vs nice to have, and provide basics needed to execute a good TMV study.
TL;DR
- TMV ensures test accuracy, repeatability, and fitness for use
- It supports design verification, validation, and regulatory compliance
- Plan TMV studies around real-world variables and clear criteria
- Validate third-party lab methods before relying on results
- TMV improves data integrity and reduces development risk
What is Test Method Validation?
Test method validation is the process of demonstrating that a test method consistently produces accurate and reliable results for its intended purpose. TMV provides objective evidence that a test method is suitable for its intended use. TMV may apply to test methods used in design verification and validation, process verification and validation, incoming inspections, etc. In both development and manufacturing, TMV ensures that selected test methods accurately and reliably measure what they are intended to assess.
Regulatory bodies like FDA and ISO 13485 address test methods validation as part of the broader quality management system as stated below:
- 21 CFR 820.72 (a): Each manufacturer shall ensure that all inspection, measuring, and test equipment, including mechanical, automated, or electronic inspection and test equipment, is suitable for its intended purposes and is capable of producing valid results.
- 21 CFR 820.75 (a): Where the results of a process cannot be fully verified by subsequent inspection and test, the process shall be validated with a high degree of assurance and approved according to established procedures. The validation activities and results, including the date and signature of the individual(s) approving the validation and where appropriate the major equipment validated, shall be documented.
- ISO 13485:2016 – 7.5.6: The organization shall document procedures for validation of processes, including: c) use of specific methods, procedures and acceptance criteria;
When is Test Method Validation required?
Each test method must be evaluated to ensure that the method and equipment (including custom equipment) is reliable, appropriate for its intended use and meets the requirements of the test. Manufacturers should follow a risk-based approach to determine whether to validate a test method. Self-evident tests are defined as tests that have discrete outcomes that are easily discerned (such as a part feature that is present or not), and that require little training to discriminate between pass or fail.
A standardized test method or a self-evident test typically does not require a TMV. A risk-based approach should be used to determine when a TMV is required.
Types of Test Method Validations
There are two types of TMVs, based on the type of data collected: attribute or variable.
Attribute Test Methods (Non-statistical – Pass/Fail)
Example: A Go/No-Go gauge used to check if the part fits (or does not fit) correctly within the gauge. A good part would fit, and a bad part would not fit using a Go/No Go gauge.
Variable Test Methods (Statistical – Measured values)
Example: Measuring a part with calipers
An operator measuring parts with a caliper can be a source of variability as they can have different results each time. Multiple operators measuring parts can be another source of variability, as each could measure the parts in a different way. A TMV can determine the consistency of operators to themselves and to each other.
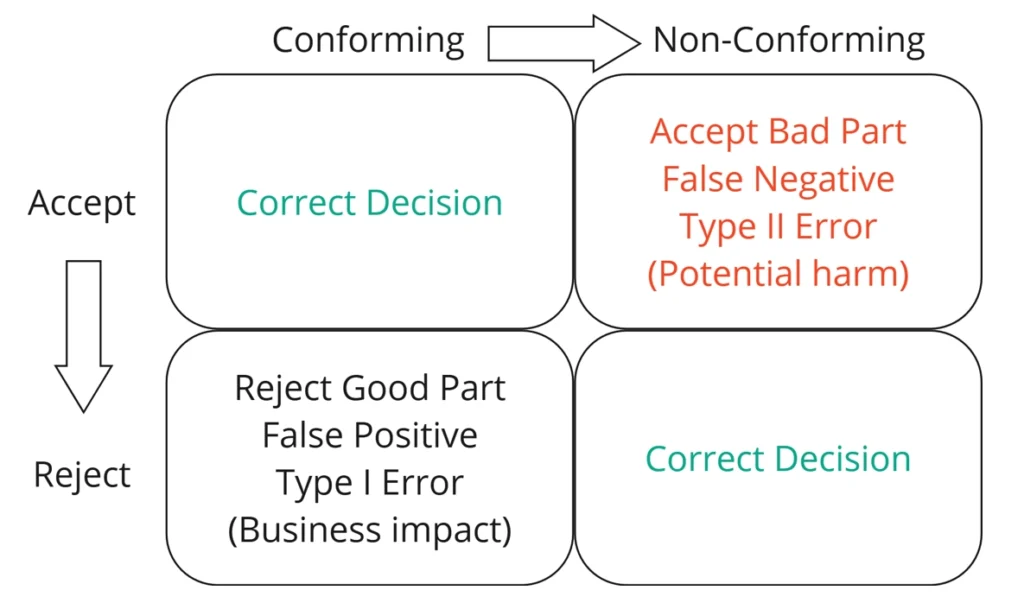
A successful test method minimizes the occurrence of type I and type II errors (Figure 1). A type I error (false positive) occurs when an inspector rejects/fails a good part. This has a business impact because a part that is good did not make it to the consumer.
A type II error (false negative) occurs when an inspector passes/accepts a bad part. This has a potential patient risk and therefore is desirable to minimize as much as possible.
Once a medical device moves into manufacturing, maintaining consistency in quality and performance is crucial. Test method validation plays a vital role in quality control (QC) processes by ensuring that manufacturing tests provide meaningful and repeatable results. Some benefits of TMV in manufacturing include:
- Process Stability: Validated test methods help manufacturers monitor process control, ensuring that every batch meets the required specifications.
- Regulatory Compliance: TMV is a critical component of Good Manufacturing Practices (GMP), helping manufacturers meet FDA and ISO 13485 requirements.
- Confidence in Test Methods: TMV ensures that testing procedures consistently produce accurate and reliable results, reducing the risk of false passes or false failures.
Key Steps in Planning Test Method Validation
To conduct test method validation for medical devices, the following structured steps should be considered:
- Plan the TMV
- Define the objective(s) of the test method and key performance parameters. What are you trying to assess?
- Example: Is a caliper an adequate measurement tool for what I am trying to measure? Will there be variability between users?
- Develop the Protocol & Acceptance Criteria
- Document the test method (i.e. a Gage R&R), equipment and any other conditions for the test.
- Define the acceptance criteria.
- Example: 3 different operators will use the caliper to measure parts, 3 times each. Their measurements will be compared to themselves and each other.
- Conduct the Testing
- Perform the TMV on production representative samples.
- Example: Trained operators will randomly measure parts with calipers multiple times.
- Analyze the Data
- Evaluate the results from the TMV.
- Identify sources of variation (operator technique, equipment calibration etc.) Is this test method sufficient for the purpose? If not, determine the sources of error and mitigate (and re-run the new TMV). This could result in operator training or selection of different equipment.
- Document & Report Findings
- Summarize TMV results, statistical analysis, and conclusions.
- Ensure documentation supports regulatory compliance and quality control.
Proper execution of these steps ensures that test methods are scientifically sound, regulatory-compliant, and reliable for assessing the medical device quality and performance.
Conclusion
Test method validation is a fundamental aspect of medical device development and manufacturing. It ensures accuracy, reliability, and compliance. Without robust validation, companies risk regulatory delays, quality issues (passing bad parts), business risks (failing good parts), and potential safety concerns. By following a structured TMV approach, organizations can enhance manufacturing consistency, and bring safer, high-quality medical devices to market. Investing in thorough test method validation not only meets regulatory expectations but also establishes trust in product performance and reliability.
Palash Jha is a QA/RA Specialist at StarFish Medical with a strong background in biomedical engineering. He has over 7 years of experience in orthopedic medical devices and have worked in product development and quality engineering roles. Palash is driven by a passion for continuous improvement and enhancing the quality of life for people through his work.
Images: StarFish Medical
References
- Code of Federal Regulations, Title 21, Part 820.72 Inspection, measuring, and test equipment
- Code of Federal Regulations, Title 21, Part 820.75 Process validation.
- ISO 13485:2016 Medical devices – Quality management systems – Requirements for regulatory purposes
- Statistical Procedures for the Medical Device Industry by Dr. Wayne A. Taylor