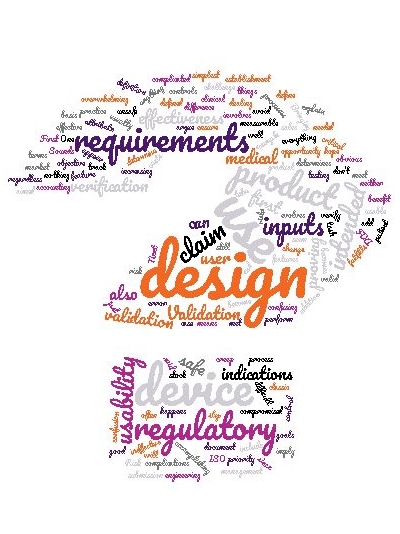
Design Control, the method to the madness
All regulatory processes are aimed at proving a device is safe and effective. One would hope that regardless of the regulatory requirements those goals would be a priority, if only to avoid the after sales costs of dealing with an unsafe or ineffective product. I would argue the FDA, as well as the ISO 13485 design control process, don’t include anything that is not good design practice.
Bringing a product to market is a challenge, add in the regulatory complications of a medical device and the task can appear overwhelming. But, is it?
First is the establishment of design inputs. In the simplest terms the design inputs are the intended use, indications for use and then all of the requirements needed to meet that use. The intended use and indications for use imply a claim to effectiveness. This claim is the basis for the regulatory submission since it should explain why the product is a medical device and also define the benefit to the patient.
Risk management and usability engineering are critical to the design inputs definition. Sounds complicated, but this is where we ensure the end product will be safe and usable. Both things seem so obvious, but neither attribute just happens. As a design evolves, the risks change and usability can become compromised. A classic example is feature creep, the gradual addition of features until a device becomes difficult or confusing to use, increasing the risk of user error.
Next, perform verification and validation. This is nothing more than proving the device does everything we said it would and that it also fulfills the claim defined in the first step. There is often confusion as to the difference between verification and validation. In the first case we verify the requirements have been met through a very objective accounting of all the measurable requirements. Validation determines if the device is a valid means of accomplishing the intended use. Validation usually involves user and clinical testing to document effectiveness and usability.
The design control process is an opportunity to take stock and determine if the design is still on track. The main difficulty in implementing a design control process is not in performing all of the steps but rather in keeping a record of the design process to provide proof to a regulatory body that all of the steps were taken. Design is generally an iterative and adaptive process and the steps are almost never done in the linear fashion described above. It is very easy to get sidetracked in design and lose track of part, or even all of the original design goals. In other words, the tactical decisions start to affect the strategic decisions.
Design control shouldn’t inhibit creativity; it should enable it by providing a safety net in the form of a system to fall back on when the unknowns start showing up during design. Creating a new medical device is always challenging but having a method to the madness increases the chances of success.
Rob Keur is a former regulatory affairs expert at StarFish Medical. He follows his own advice on medical device performance specifications when providing Regulatory Support and Quality Management services like QMS-in-a-box to our clients.
Images: StarFish Medical