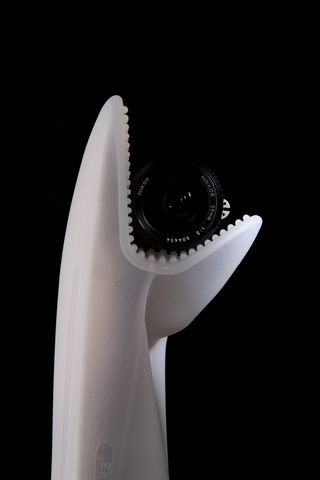
Silicone moulding strategies for medical applications
Two key variables in rapid silicone prototyping are material selection and silicone moulding strategy. In my “Medical applications and early stage design – silicone material selection” blog, I identified the most critical specifications to focus on when choosing an RTV (room temperature vulcanization) silicone to be used in moulded parts. In this blog I will cover how to mould silicone parts.
Rapid moulding
There are two common approaches for creating rapid moulds for silicone parts.
The first is to create a rigid positive model of the desired part (“master model”) and then submerge it on a high durometer silicone (most likely tin silicone). The master model will also include venting, casting and location features. The already cured silicone negative is then split into two parts (moulds) and the master model is removed. A “print” of the part is then ready for reproduction by casting the desired silicone in the negative silicone mould. This method is most commonly used in other materials such as epoxies, urethanes, and soft metals alloys, and it is intended to obtain more than one part out of the soft mould. When doing this procedure in-house there is a risk of not getting the desired tolerances due to the plasticity of the moulds.
The second approach consists of designing your own negative tool out of a rigid material (Stereolithography – SLA – processes are commonly used) and then cast, compress or inject the desired silicone into the rigid mould directly. Since we usually work with small size parts at StarFish, our preferred methods are compression or injection. Compression is often used in really small parts such as gaskets. Injection methods are normally used either in complex parts containing areas of difficult access, or in overmoulded or thin components. This method should not be confused with plastic injection moulding. In our case, injecting silicone refers to introducing the material via a manual syringe or similar using low pressure just to facilitate material to reach all regions of the mould.
Key points for mould design
Other aspects to consider while designing your mould include:
- Degassing: All silicone contains air bubbles, especially where mixing two parts is required. Air bubbles float to the surface and will definitely show in the final part if they are not removed. The easiest way of doing this is by degassing, i.e. applying suction to the whole system forcing air to escape. Air will only escape if there is room for it. Therefore, degassing or venting structures should be present in your tool.
- Equipment: Two indispensable pieces of equipment for in-house moulding are the vacuum chamber/pump (for degassing) and the precision scale (to procure the exact mixing ratio). The size of the vacuum chamber will definitely affect how your mould is designed since it has to fit inside it.
- Part size: Part size is an obvious one. Your mould has to be designed to accommodate the part you are creating. But what if the part is so small that it is hard to take it out of the mould? Sometimes extra material should be allocated in non-critical surfaces of the part to allow easy extraction once the part has cured.
- Cost: The less material you use to create the mould (if produced using 3D printing), the less expensive it will be. A good balance between thickness and strength of the mould must be always considered.
In-house vs Outsourcing
Producing silicone parts in-house provides flexibility in terms of time, cost, number of parts, material used, easy tool modifications, etc. Nevertheless, outsourcing should always be considered before committing to designing moulds in-house. Vendors will produce parts following the specifications you request and they generally have more experience in the field than you do. This may lead to a more cost effective solution than investing the time yourself.
As I noted in my previous blog, when designing elastomeric components that will be used in contact with the human body, silicone is often the “go-to” material. I hope my tips on material selection and silicone moulding strategies help. I’d enjoy hearing from readers on other tips or methodologies they have developed.
Joan Hereter Gregori M.Eng. is a former StarFish Medical Mechanical Engineer. He helps develop criteria for silicone moulding as part of his work in product development. A native of Catalonia, Joan is frequently bugged by his editor’s use of dashes- like this one.
Image: 15229167 © Phollander | Dreamstime.com