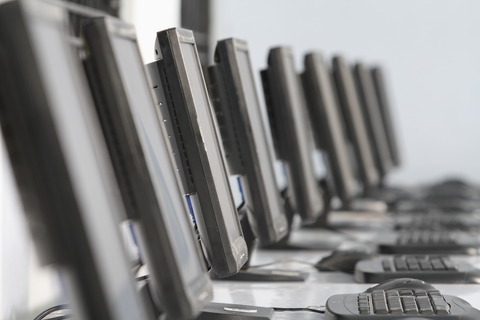
Off the shelf components in medical devices
When developing a medical device, it’s easier both in time and effort not to reinvent the wheel. Sometimes, off-the-shelf (OTS, or COTS – commercial off the shelf) components don’t meet the device needs, and usually these deficiencies are obvious. The problem arises when we unconsciously ask for more than the original widget design requires.
Obviously, if we’re designing part of the electrical safety system, we should choose medical-grade power supplies, power cables, and other components designed to comply with 60601. But what about something like laptops or monitors? There is a balance of tradeoffs to be considered between using Off the shelf components and more costly, customized components.
Here are a number of pitfalls we have to avoid:
- Lack of control over the availability of the component (obsolescence or supply).
- Lack of control over the revision of the component.
- Customization options can be limited or require large MoQ (minimum order quantity).
- Surface Finish and Quality aren’t guaranteed – you get what you buy.
- Components are not certified for the application.
COTS components have a marketable product life and are often frequently replaced by newer models. Laptops are one of those components that frequently change model numbers, as an example. If the component is highlighted in your Risk Assessment file and is an integral part of your device, then having it change frequently will drive a lot of regulatory review costs at a minimum, and potentially trigger costly retesting in the worst cases. Developing a laptop specification and submitting that specification may reduce the regulatory burden, or you can use an integrated system where the system is sufficiently supported (for a length of time).
With Off the shelf components, we also lose control of the revision of the component. While the supplier may not change the model number, they nevertheless, can change the product to suit their needs and on their timescale. Without a high volume agreement, suppliers may choose to not notify customers of changes, especially if the change still meets the supplier’s specifications even though it no longer meets ours.
Of critical importance to medical devices is installed software or firmware. When using COTS components (particularly those that have risks associated with them), it’s important to have in-line manufacturing tests (incoming, End of Line (EoL) tests, etc.) to ensure that the component hasn’t changed without supplier notice and still meets any risks or safety issues identified. Even if you are notified, you may still have to do costly testing to confirm that functionality hasn’t changed.
Often the cost of Off the shelf components are really attractive compared to custom ones, and that’s because of the component’s high volume. Customizing COTS components is possible – you can gain some of the benefits of the high volume product while at the same time, securing the component against design changes internal to the supplier. But the supplier may only be interested in large volumes (high MOQ), making this option unattractive. Similarly, you may have a required quality level for your device which the COTS component doesn’t meet or doesn’t meet consistently. Trying to enforce quality requirements on COTS components can be problematic without a custom order and a large MOQ.
If the component is used in a similar fashion as intended, usually a supplier is willing to stand by their product, even though it may not have been designed with the specific end use in mind. Some however, will not. Other suppliers may be willing to certify their product, but only with additional testing. It’s important to have those discussions early so a late substitution and/or development isn’t required.
COTS components can be extremely valuable for their lower cost and reduced development time. But there are some (sometimes exceedingly important) things to keep in mind before committing to their use. I’ve shared several in this blog. I’d enjoy hearing from readers about their experiences.
Dana Trousil is a StarFish Medical Manufacturing Engineer. He has successfully launched many products, from small volume production up to moderate volumes (up to 1 million parts per year).
Image: 4320532 © Kakarlapudi Venkata Sivanaga Raju / Dreamstime.com