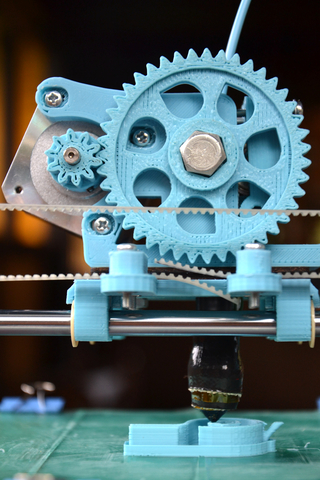
Compare 3D printing prototyping merits for three common processes
From form studies to functional components at the early stages of prototyping to full production, the applications for 3D printed parts and 3D printing prototyping are growing rapidly. Parts designed in 3D modeling software can be transferred and quoted by a 3D printing company almost instantly. Many 3D printing companies return parts to the designer within 24 hours. This decreases timelines for the overall design iteration process, as verification of components is performed promptly upon receipt of parts.
What 3D printing prototyping processes are available and what are their relative merits? Several techniques are employed at commercial scale. In this blog I outline and compare three of the most commonly used in medtech product development.
FDM (Fused Deposition Modeling) / FFF (Fused Filament Fabrication)
FDM uses thermoplastic filament which is fed through a nozzle to create fine micro-scale strands, deposited side-by-side and layer-by-layer. This eventually builds a finished part. The part’s walls are generally solid, with a variable in-fill density which can make for lighter parts. Since engineering-grade plastics can be used, the parts can exhibit strength properties approaching injection moulded or machined plastic parts. Also, because thermoplastics are reflowable, heated inserts can be used for fastening. This increases part application potential due to the strength of both the parts and fastening points. However, surface quality is generally an issue due to the cosmetic lines/layers and support witness points created during fabrication. To make up for this, certain materials can be manually polished, but others, like Poly(lactic acid) (PLA), cannot.
While setting up the build of the part it is important to consider build direction to minimize the effects of the final layered surface on part function and cosmetic requirements. The direction of the build can influence the directional strength of the part, the amount of additional support material used, and the level of detail in a given feature. Finally, certain materials with higher processing temperatures will exhibit shrinkage, especially with larger parts. This creates design constraints such as a required lower in-fill (reduced density) of material in larger parts.
SLA/SL (Stereolithography)
SLA employs a photo-polymer resin bath, platform, and laser beam to create parts on the micro-scale layer-by-layer. Parts can be completely solid or hollow, with hollow parts reducing material required and lowering part cost when strength is not required. However, hollow parts will require drainage features to allow for entrained resin to escape. SLA materials form thermosets, which cannot be reflowed and therefore heated inserts cannot be used to the same effectiveness as they are intended. Alternative fastening techniques can be employed, such as helical or press fit inserts.
Unlike FDM, finished parts show little evidence internally or externally of layering. Standard post-processing creates a matte finish on the parts which suitable for most uses. However, when optical clarity is required, vendors can provide additional processing to produce surfaces that emulate polycarbonate or acrylic, allowing for optical applications such as lenses or parts used to visualize internal flow of fluids. There are a wide range of materials that can emulate the strength of traditional materials, from polypropylene to die-cast aluminum. The metal emulating parts require a significant post process that increases the cost, but provides a highly detailed part with the mechanical properties of metals. Finally, because the curing process employs a laser beam, ultra-fine resolution can be achieved. You can create layers as small as 0.001” (0.025mm), with features as small as 0.002” (0.050mm).
SLS/DMLS (Selective Laser Sintering/Direct Metal Laser Sintering)
SLS comprises a high-powered laser, powdered material (plastics, glass, ceramics), and a bed-roller assembly. Powdered material is applied by the roller in thin sheets. Sweeps of the laser then sinters (or fuses) together material layer-by-layer, creating parts with up to 100% in-fill density. DMLS employs the same process, but instead uses applicable metals (aluminum, titanium, stainless steel, etc.). An advantage of the SLS process is that it allows for the highest strength plastic parts across all three processes. When engineering-grade plastics with high stiffness and strength along with glass in-fill, SLS parts are extremely tough. Parts can be employed in the most demanding of applications, with functional features such as snap fits providing assemblies that don’t need separate fastening components.
Standard surface finish is a matte/sandy texture due to the fabrication process, but this can be polished or blasted to a desired final finish. Repeatability across a small volume of parts is high when compared to machined components, as parts are created on the same bed.
A distinct advantage of SLS over FDM or SLA 3D printing prototyping is that since parts are supported by unsintered surrounding material, there is no need for support structures for features. This allows a consistent surface without the need for post-processing to remove supports. Parts can also be made within parts, which opens the doors to alternative designs.
3D-Printing Prototype Sheet Metal Parts
Process Comparison:
Attribute | FDM | SLA | SLS |
Part Quality | Low to Medium | High | High |
Plastic type | Thermoplastic | Thermoset | Thermoplastic |
Surface | Layered finish | Matte to clear finish | Matte to smooth finish |
Transparency | Opaque material | Opaque to transparent material | Opaque material |
Mechanical Strength | High tensile strength | Brittle | High overall strength |
Layer thickness | 0.125 to 0.5mm | 0.025 to 0.05mm | 0.10 to 0.25mm |
Support structure | Needed | Needed | Not needed |
Airtight | No | Yes | Yes |
Chemical Resistance | Not airtight | Not defined | High |
Materials Available | ABS, PLA, Nylon | Photocuring Resins | Polystyrene, Polyurethane, Nylon, Aluminum, Titanium, Stainless Steel, Cobalt Chrome, Inconel |
Nathan Müller, EIT, is a StarFish Medical Mechanical Engineer. He is an experienced EIT with primary skills based in mechanical design of biomedical products ranging from biomedical lab research to solar and building systems. This is his first blog for StarFish Medical.
Image: 27707049 © Josefkubes | Dreamstime.com
How to get the most from your FDM 3D printer.