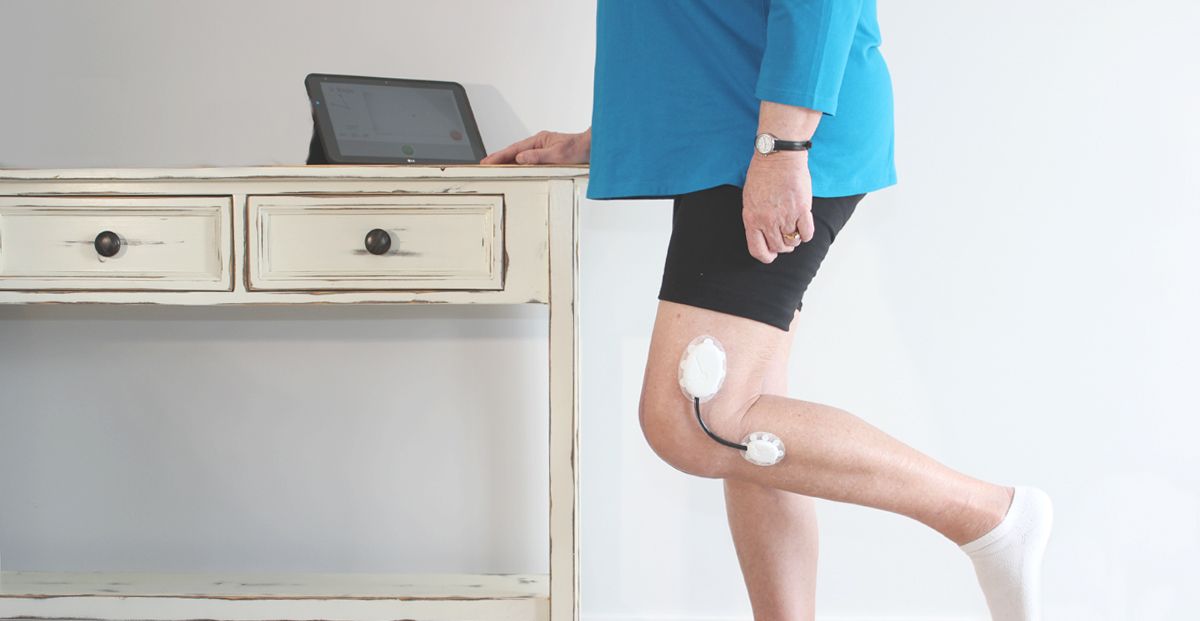
5 things to do when designing a wearable medical device
There is no denial that the wearable medical device market is growing extremely fast and companies are rushing to get their device to this fast evolving market. Although timing is critical for technology based devices, what is more important is to review and address any high risk issues carefully during each step of development to ensure a successful design. It is much easier to make changes in the beginning rather than make costly fixes later in the development.
Over a three-part blog series I will go over the dos and don’ts when developing a skin-worn wearable medical device and the science of sticking to skin. This first blog explains the dos of skin-worn medical device design and development.
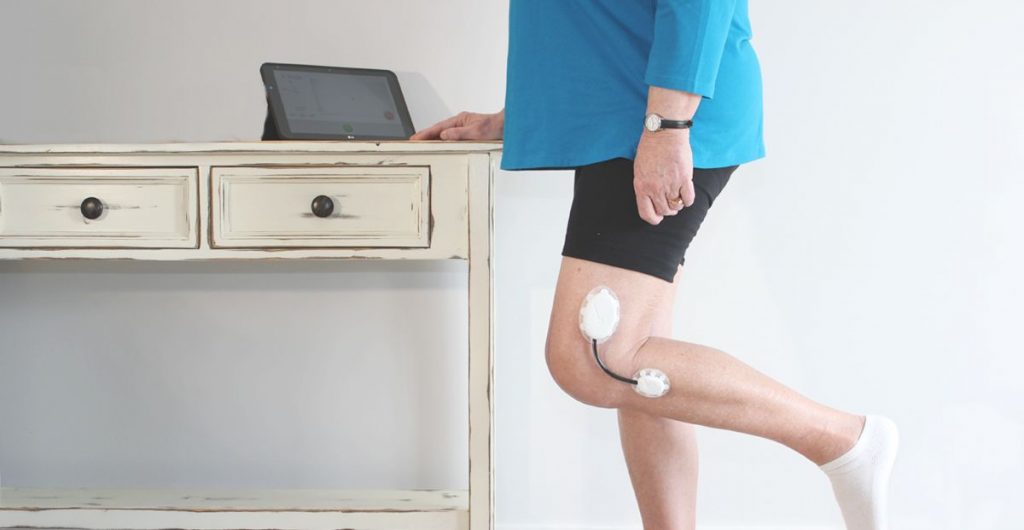
Do
Research the user population first thing and define the use scenarios and appropriate workflows that blend into their current daily lives or current protocol for procedure. User demographics, diets, skin types, common skin diseases, body hair, gender, wear time, level of activity, placement (such as a joint or a flexible site), size of the contact area, climate (region), chance of exposure to liquid (such as water, sweat, blood, and etc.) of the target user population are all critical information that need to be collected before the design of the device can begin. These factors will drive the features of the device, how the user interacts with it, how it looks, how it will be manufactured, and the adhesive choice.
Do
Facilitate an open line of communication between your industrial design/human factors engineering team and electrical/firmware and software engineering team. What kind of data and how much will the device collect? Does the data need to be transferred to a separate viewing device? If so, what type of connectivity will it have? What type of battery should it use? Does it need to be recharged or will it be disposable? Is flexible circuitry an option? The processing power, power consumption, and wireless communication requirements will affect the size of the device and workflow for device use. Layout of electric components will influence the geometry of the device. The two teams must work together to prioritize performance requirements, agree on the electrical component size and layout in order to create a device that have the overall appropriate size, form and user interface layout.
Do
Determine if the device should be completely disposable or reusable. Will it have consumable parts? Should it be refurbished? If so, what is the protocol for collecting the used devices? The workflow research conducted in the beginning of the development will shed some light onto whether the device should be disposable or rechargeable and whether it needs consumable (disposable) parts or not. The decision you make will have an impact on the workflow. The goal is to create a device that does not disrupt or intrude current workflow of the procedure. If the device is for long-term wear, it should not be intrusive to their clothing choice and the daily activities of the user.
Do
Start connecting with adhesives vendors to source the right adhesive for your device. There is no such thing as a “miracle go-to adhesive” suitable for all skin-worn devices. Different adhesives (such as acrylic, silicone, hydrocolloid, or synthetic base rubber) have different characteristics appropriate for different uses. There are a variety of choices for carrier (backing) material (such as nonwoven, foam, vinyl, polyurethane, polyethylene and many others) as well. It is important to define your user population and scenario and discuss them with your vendor. The vendor can then help you decide on the right adhesive. At StarFish Medical we have working relationships with adhesive vendors who source from variety of adhesives manufacturers such as 3M, Avery Dennison, and etc. They work with us to customize, prototype, and die-cut the adhesives. The adhesive must be strong enough to conform to the contours of the body and stay secure, but must be gentle enough to minimize trauma to the skin when it is being removed. Finding the right balance is tricky. That is why it is important to speak to the experts to help identify the most suitable adhesive for your application.
Do
Make sure all components that have direct or indirect contact with skin are biocompatible. News about massive recalls due to skin rashes tainted the brand image of Fitbit in 2014. In August 2016, McDonald’s had to recall 33 million wearable fitness trackers due to skin rash and burns. Both are wristbands designed to be worn throughout the day. Skin-worn devices pose unique challenges when it comes to biocompatibility. Some areas of the body are more prone to sensitivity (face, eye areas versus feet) and some age groups have more fragile skin (seniors and infants vs. healthy adults). Natural rubber-based (“latex”) compounds, nickel in metal alloys, plasticizers are commonly known skin allergens and irritants. All these factors should be taken into consideration when choosing materials for sensors, adhesives and any other components that may come in contact with the skin.
In the next blog article, I will go over the list of don’ts for wearable medical device design and development to prevent costly fixes that may arise later in development.
Christine Park is a former Industrial Designer at StarFish Medical where she uses her knowledge of usability, colour, material, finish and emotion to design innovative medical devices for clients.
Image: Claris Healthcare