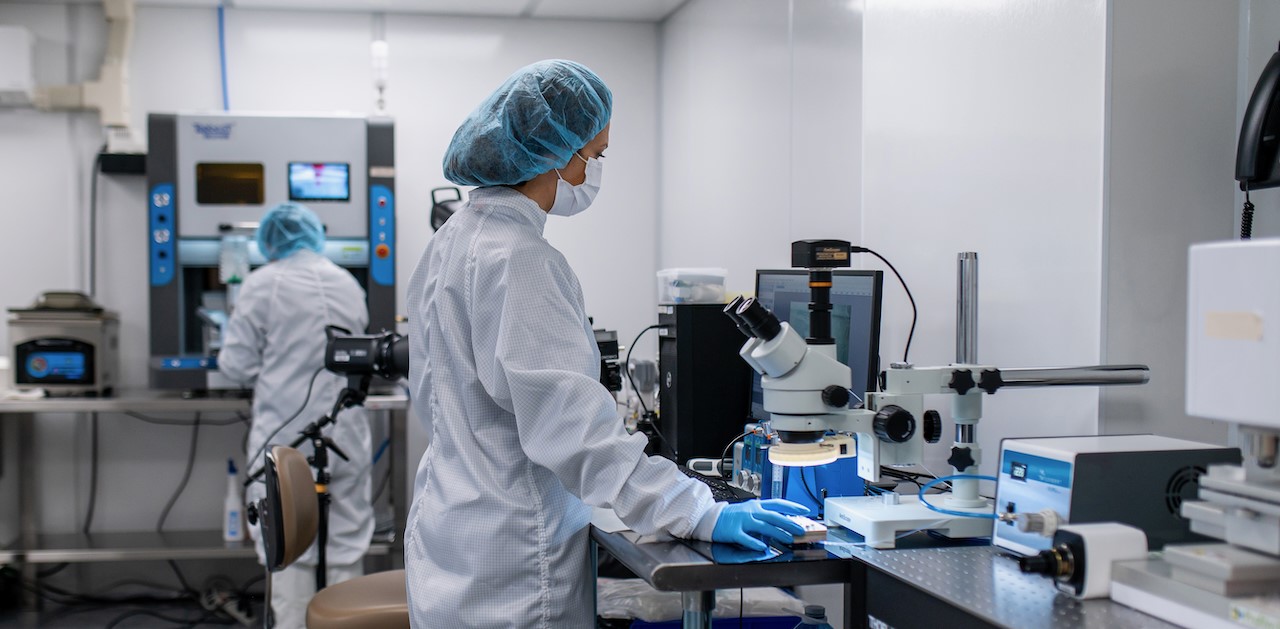
8 Cleanroom Best Practices to Maintain a CLEAN State
Cleanroom best practices are crucial to maintain a contamination-free environment, especially in industries like pharmaceuticals, semiconductors, biotechnology, healthcare, and medical devices. Here are some essential guidelines for ensuring your cleanroom is indeed clean:
Proper Gowning and Hygiene
Use gowns, gloves, shoe covers, masks, and hairnets according to ISO class level. Select personal protective equipment (PPE) and gowning order that is tailored to the product being built in the cleanroom and relevant ISO class.
Cleanroom gowning protocol differs depending on cleanroom class and application. In ISO Class 7 or ISO Class 8 cleanrooms, frocks are often acceptable. A cleanroom classified as ISO Class 5 or ISO Class 6 (or cleaner) requires cleanroom coveralls, along with hoods, gloves, and booties (shoe covers). For sterile processing, additional precaution is needed to assure that no sterile surfaces contact non-sterile surfaces during gowning, processing, or cleaning.
Select garments with low particulate shedding. Wash hands thoroughly before entering, and avoid touching exposed skin once in the gowning area. The Gowning Sequence is as essential as gowning itself.
Improper gowning procedures are the most common source of cleanroom contamination. Humans carry billions of microscopic particles that can easily be shed from the skin, hair, or clothing. Wearing unsuitable attire or skipping steps in the garbing process can quickly lead to contaminated work areas, product failures, or cleanroom shutdowns.
Wash hands properly prior to entering the cleanroom. Poor hand hygiene increases the vulnerability of cleanrooms to bacteria and potential transfer or introduction of microbes such as viruses and fungus.
Minimize Movement and Noise while in the cleanroom
Move slowly and avoid fast or jerky actions, as they increase particle shedding in the cleanroom. Fast movements can disrupt the particle flows in the cleanroom. Talking releases particles, so keep conversations to a minimum within the cleanroom environment. Speaking should be limited to necessary communication and should never occur in critical areas. Always limit the number of people by only allowing essential and trained personnel inside the cleanroom.
Use proper Cleaning Techniques
Cleanroom cleaning procedure involves a series of steps that are followed to ensure thorough cleaning of the room. The importance of following a strict cleanroom cleaning procedure cannot be overstated. Any contamination in a cleanroom can have serious consequences, leading to product defects, equipment damage, costly rework, and even compromised safety of personnel.
Following an approved Cleanroom Cleaning Procedure helps to mitigate such risks by ensuring that the environment is free of contaminants that can cause harm. Furthermore, adherence to the Cleanroom Cleaning Procedure is essential for regulatory compliance. Regulatory bodies such as the FDA require firms in industries including pharmaceuticals, biotechnology, and electronics to meet strict standards for cleanroom cleanliness. Noncompliance can result in significant legal and financial penalties. In summary, Cleanroom Cleaning Procedure is critical for maintaining the integrity of the products or processes being protected, ensuring the safety of personnel, reducing costly rework, and maintaining compliance with regulatory standards.
Define Regular cleaning schedules designed based on product and class to clean surfaces, equipment, and floors. High-touch areas need frequent attention. Usually cleaning all touchpoints on per-use basis is preferred. Detailed cleaning can be done based on usage where all surfaces, furniture, walls, floors, and ceiling are included. Use low-lint wipes with approved cleaning agents, following the “wipe-down” method (top-to-bottom, clean-to-dirty).
Replace and maintain filters to prevent particle buildup in air filtration systems on regular interval.
Control Airflow and Pressure
Ensure airflow moves from the cleanest to the less-clean areas to reduce contamination. Always keep cleanrooms under positive pressure relative to adjacent spaces to prevent contaminants from entering. Avoid blocking vents and air returns and keep airflow unobstructed to maintain even distribution of filtered air. Air flow visualization tests can be performed for checking the flows
Furniture, featuring hard-to-clean pockets where dust and debris collect, is another common source of contamination.
Control Entry and Exit Procedures
Only authorized personnel should be allowed entry. Use secure access systems to control who enters.
De-gown in reverse order of the gowning process defined in your procedures; dispose of single-use items proper. Do not bring in personal items, as they may introduce contaminants.
Regular Training and Audits
Conduct regular training sessions for personnel on cleanroom protocol, gowning, and emergency procedures. Training should involve all necessary processes like cleanroom maintenance, cleaning and general safety measures on top of gowning processes. Every facility and product is different so design protocols and training intervals that best suit the standards you follow. Regularly audit cleanroom practices, cleaning records, and particulate levels to ensure compliance.
Proper Handling and Storage of Materials
Minimize storage in the cleanroom by only bringing in material needed for builds that can be packaged and shipped post build. No extra equipment or inventory should be stored in the cleanroom as they disturb air flows and create dead spaces. If necessary, store materials in closed, clean containers whenever possible. Transfer items carefully using clean containers and limit unnecessary movement of materials.
Monitor Environmental Conditions
Maintain stable temperature and humidity levels, as fluctuations can affect particle generation. Temperature and humidity can be measured in-house by placing a temp-hygrometer. Regularly monitor airborne particulates using a calibrated particle counter that is available in-house or by using third part vendor. Monitor microbial counts to ensure they remain within specified limits defined in the applicable standard(s).
The clean room classification table shows maximum concentration limits (particles/m3 of air) for particles equal to and larger than the considered sizes shown. Some classifications do not require certain particle sizes to be tested because the respective concentrations are too low or too high to be tested.
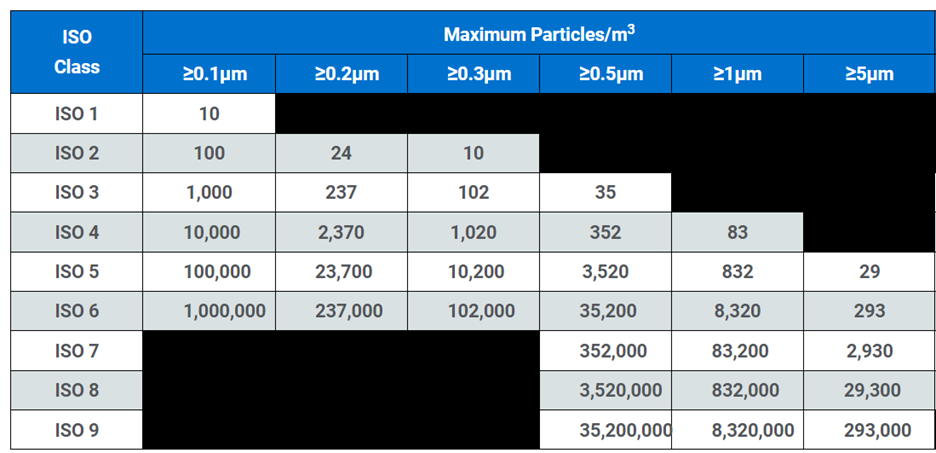
Summary
Creating and following a list of Cleanroom best practices is an important part of maintaining a contamination-free environment. The eight areas describer in this article provide guidelines for designing a checklist that will ensure your cleanroom remains clean. I would enjoy hearing additional tips and best practices from readers.
Disha Patel is a Research Scientist at StarFish Medical.
Images: StarFish Medical
Related Resources
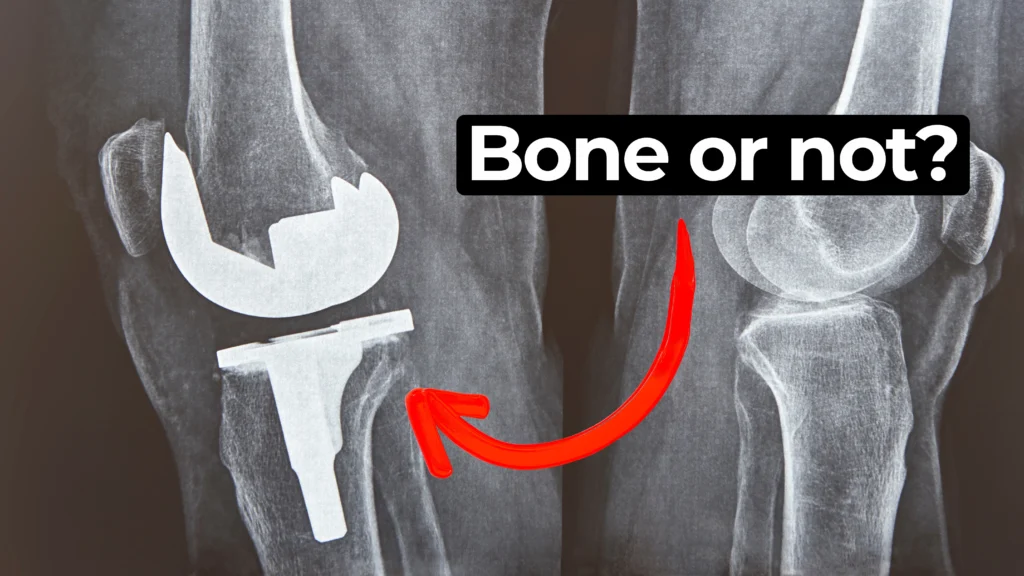
In this episode of MedDevice by Design, Ariana and Mark dive into the biomechanics and materials science behind osseointegration for implants.
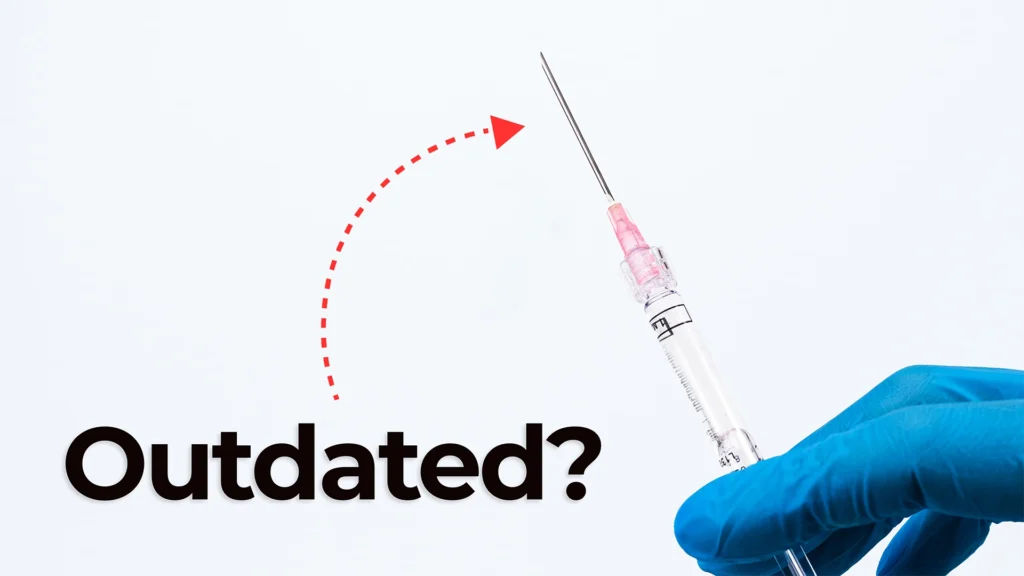
Nick and Nigel dive into the world of jet injector drug delivery. This needle-free method, made popular in science fiction and real-world vaccines, is still used today.
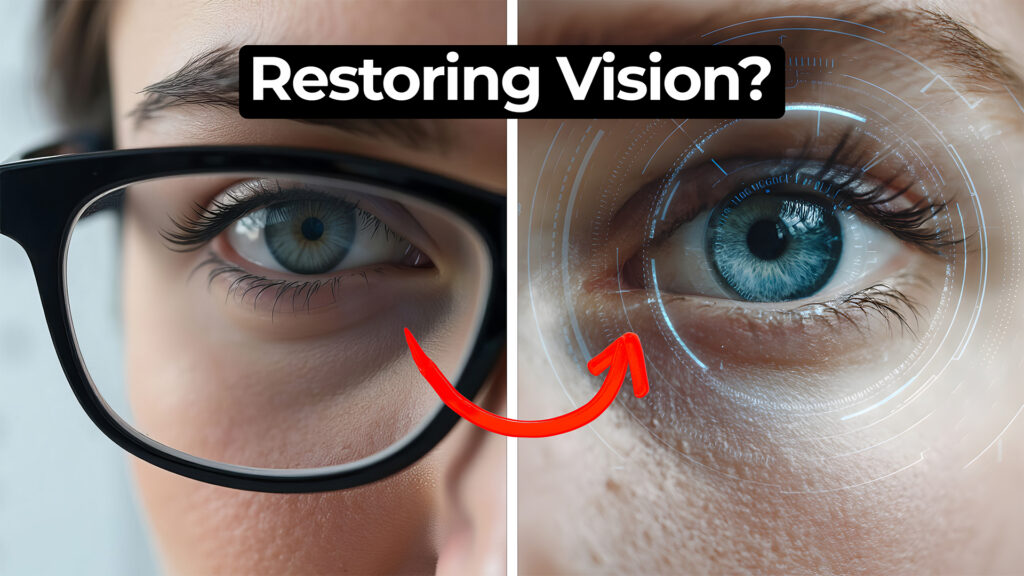
Ariana and Mark explore how accommodative intraocular lens technology may one day restore natural vision for people who require cataract surgery or suffer from presbyopia. As Mark shares, traditional bifocals are not ideal, and new lens solutions may offer better outcomes.
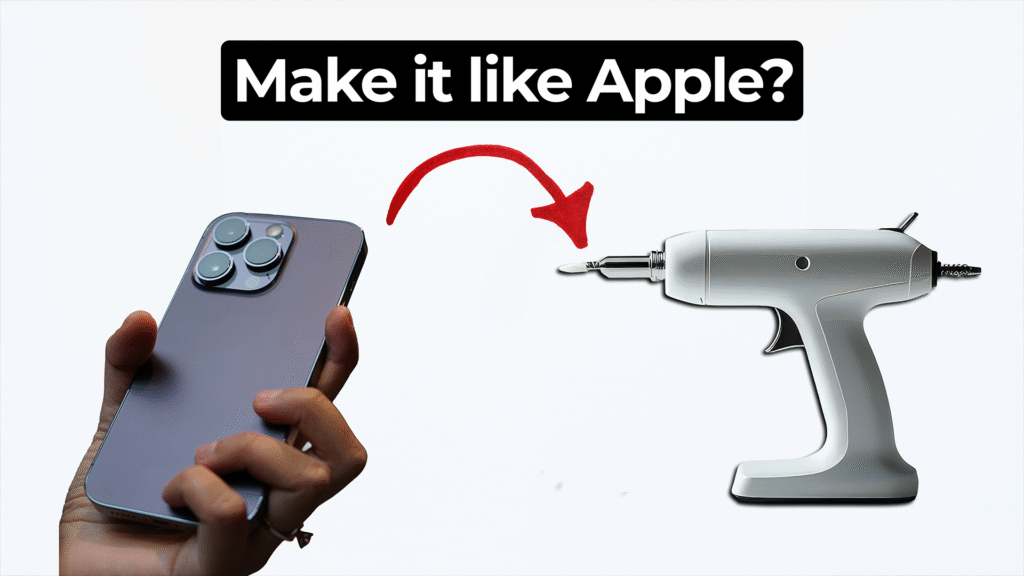
Many clients now request their devices to look and feel like Apple products. But achieving that level of simplicity and elegance is not as easy as it seems.
Learn how StarFish Medical led a consortium that created a Ventilator 2.0 therapy device in record time.