I was asked recently if I knew whether anodized aluminum meets ISO-10993 (a standard for biocompatibility). USP class VI is another standard that’s often quoted – the two standards are similar in some respects, but are not equivalent.
Aluminium oxide, Al2O3, also known as alumina, forms readily when bare aluminium is exposed to air. Alumina is a non-toxic substance in and of itself and as an example, has been used in the dental industry for many, many years as a ceramic compound. With the rise of antibiotic resistant bacteria, alternative antimicrobial methods are being researched, and among the antimicrobial agents being looked at is alumina. Aluminium, on the other hand, is toxic in high doses, and can lead to bone disease, encephalopathy, and other conditions, generally as a result of renal failure when aluminium is allowed to build up in the body. Aluminium is in many things in trace amounts, pop in pop cans for instance, has slightly elevated amounts due to the acidic nature of many soft drinks, but the levels are still well below recommended limits for the vast majority of people.
Anodizing works by controlling and forcing the oxidation of aluminium (into alumina) such that the oxidation layer is anywhere from 0.5μm, to over 100μm, depending on the type of anodizing. By contrast, the normal layer of alumina is just a fraction of that (.002-.003 μm). In the anodizing process, the aluminium surfaces are washed and rinsed, etched and then finally oxidized. It is this hard surface of alumina that provides the barrier for corrosion. The anodizing process, however, creates a porous surface on the microscopic scale:
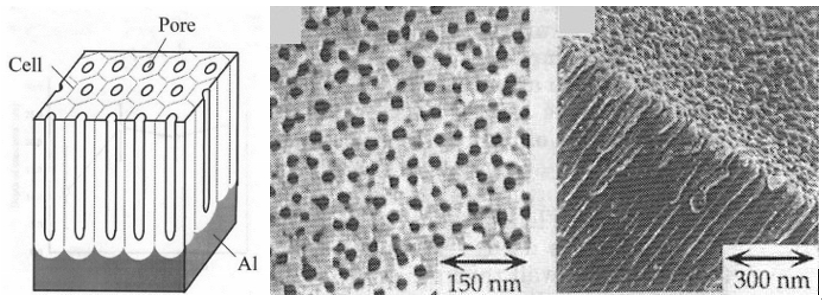
If a part is dyed, these pores are where the dyes take hold. Regardless, the final step is sealing the pores with a sealant.
ISO-10993 has a significant section on risk (see this blog here), but focusing on the device categories, these categories are divided into surface devices (wearable), externally communicating devices (e.g. dialyzers, laparoscopes), and implantable devices. These categories are broken down further into various subcategories such as skin contact, mucosal membrane contact (i.e. inside the nose), contact with blood, etc. Finally, the duration of contact is considered (<24h, <30d, >30d). Generally, for intact skin contact only, there are three tests that are required, regardless of duration: cytotoxicity, sensitization, and irritation/intracutaneous reactivity. As contact increases through mucosal membranes, compromises surfaces, and on to implantable devices, the list of tests grow for obvious reasons.
In context of biocompatibility and ISO 10993, the anodized surface provides a barrier against the aluminium, but the coating is porous, thin, and subject to corrosion from cleaners and biomedical environments. Anodizing does not stand up well to bleach, as an example, and any dyes will not stand up to repeated sterilization as the sealant is broken down and the dyes leach out.
It’s possible that for some surface contact applications, anodized aluminium will perform adequately, but this approach is not recommended. The chemical processing and nature of anodized aluminium means that of the risk assessment of the device’s manufacturing processes surrounding biocompatibility will need to be comprehensive, and, as always, biocompatibility thoroughly tested. The sealing steps and any dyes will need to be chosen with care, and likely require significant controls in production. Research into the suitability of anodized aluminium is continuing, and some special processes have shown promising results as the demand for cheaper, light-weight materials continues to grow.
Designing a medical device, but not sure whether it needs to be biocompatible? Check out A design engineer’s perspective of medical device biocompatibility.
Dana Trousil is a StarFish Medical Mechanical Engineer. He has successfully launched many products, with experience in a variety of processes, including anodizing medical devices.
Images: H. Asoh, K. Nishio, M. Nakao, T. Tamamura, and H. Masuda, “Conditions for Fabrication of Ideally Ordered Anodic Porous Alumina Using Pretextured AI”, Journal of The Electrochemical Society, Vol. 148, p. B152-B156, 2001.
T. Kyotani, L. Tsai, and A. Tomita, Chemistry of Materials, Vol. 8, p. 2109, 1996.
Tips and Techniques for Anodizing Medical Devices