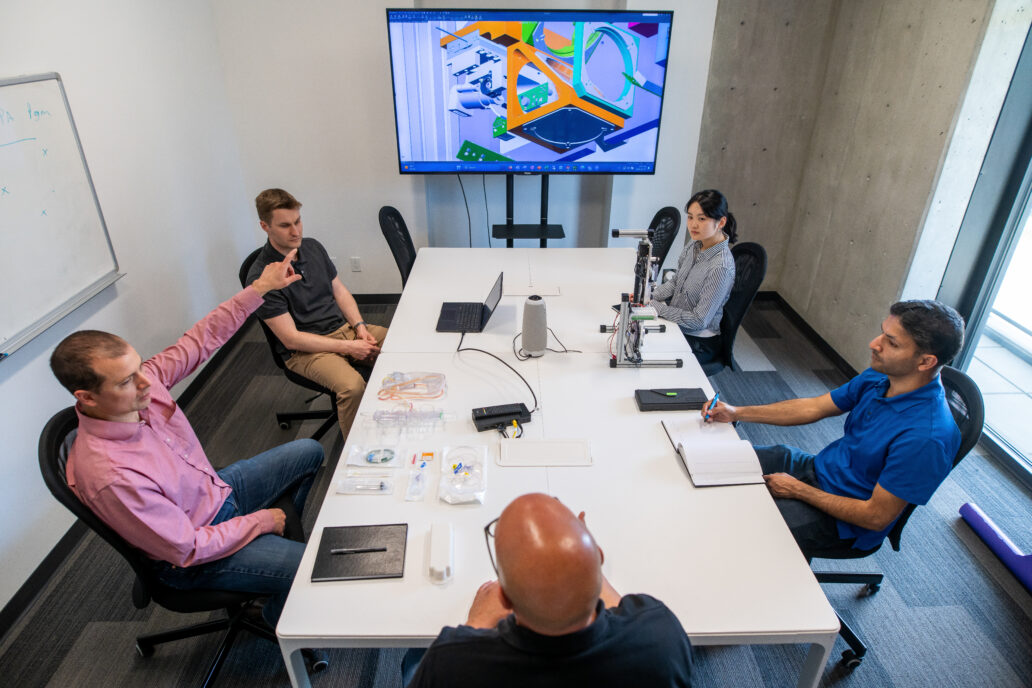
Biggest Medical Device Success Factors
What are the most important medical device success factors during development and manufacturing? StarFish employees from QA/RA, NPI, Optics, Computational Analysis, Project Management and Manufacturing answer that question with the factors they deem most important for their area of expertise.
QA/RA Medical Device Success Factors
Paying attention to detail is critical for QA/RA professionals because they serve as the final safety net to ensure product and process compliance. This involves meticulous review of Design History File (DHF) and Device History Record (DHR) documentation to identify errors or oversights that may have been missed by authors or during earlier stages of the process. By catching these issues, the QA/RA team safeguards the integrity of the product, ensures regulatory compliance, and protects patient safety.
Attention to detail is essential for navigating the complex regulatory landscape. Regulations often involve intricate requirements, and even minor mistakes in documentation, testing, or labeling can lead to delays, fines, or product recalls. Thoroughness ensures the company maintains compliance, builds trust with regulators, and delivers safe, high-quality medical devices to the market.
One thing that’s really made a big difference for QA/RA, for external audits is online training records. We must show our people are trained and competent. That is a basic premise of ISO 13485. It’s very handy to pull up transcripts of completed training. It is a big success factor in getting through audits smoothly as far as the training components and showing competence. It’s organized, it’s current and it’s very quick to access.
Computational Analysis Medical Device Success Factors
During Phase Zero of design, it is critical to identify and address the highest risks associated with the proposed architecture. The key question at this stage is: What are the primary risks in our approach, and how should we mitigate them? Engaging the computational analysis team early allows for informed discussions on the balance between computational methods, physical testing, and first-principles analysis to address different aspects of the design. For more information, read my colleague’s summary of the FDA Guidance Document “Assessing the Credibility of Computational Modeling and Simulation in Medical Device Submissions (17th November 2023)”.
Computational analysis is broadly applicable, such as for drop and impact assessments; evaluating fluid systems like blood transfusion, drug handling, microfluidics; multiphysics interactions; and exploring design through altering parameters. Early collaboration ensures that the design approach is considered in a collaborative manner while risks are mitigated before committing to plans. The goal is to save time and resources by answering critical questions before advancing an architecture that might later prove unsuitable. The design must be mature enough to provide clarity on the concept’s functionality – moving beyond abstract ideas – but not so rigid as to prevent necessary adjustments during de-risking efforts.
With a lot of optical systems, especially ones that have less stringent performance requirements, you are unlikely to get everything you need without doing some kind of computational analysis. And these days that usually means computer-based simulation. and computational analysis is necessary to meet stringent performance requirements. Once you’ve done that, it’s also necessary to do physical testing and make sure the component is behaving as the simulation says it should. That generally should be the case, but it is important to make sure. If you’re doing something that’s really simple, it may not be necessary. But, if you’re trying to make a laser beam spot of a certain size and quality, then it’s really necessary to do modeling.
Project Management Medical Device Success Factors
The most important factor in Project Management is clearly understanding the ultimate vision. Only then can the team make the right decisions independently and with confidence. Otherwise, the team is at risk of either heading in the wrong direction or inefficiently having to discuss every small detail along the way.
NPI and NPI Manufacturing Medical Device Success Factors
The most important success factor in NPI is having alignment with the client on the risk/reward for key deliverables. LEAN transfers get you to a milestone faster but defer risks to manufacturing which may cause production delays and incur additional costs. Understanding the client’s true milestone for success is key to providing the transfer that fits their needs.
For NPI manufacturing and NPI, the most important success factor is to plan for it. As far as medical device development goes, just because you managed to make one device doesn’t mean the journey is done. A lot of effort goes into making 100 devices exactly the same as the first device that you produced. Don’t assume that the job is done once you have one device working. It takes a lot of effort to make every device meet those same requirements.
The biggest success factor is always keeping an eye on the client goals and aligning internal goals and activities to align as best we can. There are times when we may have a “preferred way” of performing a task or activity, but if it is not optimal for the client to do it that way and there are no regulatory compliance constraints, we have to ask ourselves how we can accomplish the task in a way that serves the client need.
Conclusion
The most important medical device success factors during development and manufacturing vary by department and phase of development and manufacturing, but three factors play a role in almost every area:
- Goal (Vision) Alignment
- Early Identification of Risks
- Attention to Detail
Keeping these areas a high priority will greatly increase the likelihood of achieving medical device development success.
Astero StarFish is the attributed author of StarFish Medical team blogs. We value teamwork and collaborate on all of our medical device development projects.
Images: StarFish Medical