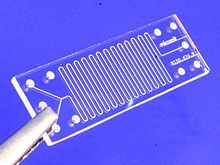
Using Microfluidic Development Tools in Medical Devices
The key to developing, innovating and refining your microfluidic system is to generate accurate information to validate your assumptions and models. Choosing the correct tools to do so is critical to the short and long term goals of your company.
Microfluidics is a broad field, with many applications verging on the frontiers of science. Medical Device applications in microfluidics are being enhanced by electric field manipulation, novel ligand sequestration, photometrics, spectroscopy, florescence, and a whole host of adjunct technologies. The potential applications in the medical space are nearly limitless and with advancements in micro fabrication, have become very cost effective.
One of the many challenges in developing these devices is figuring out if they are going to work, and then how best to optimize them. Below are my tips on how to develop your next microfluidics device:
Tool #1 – First Principles Calculations and Checks
Fast iteration and design with first principles calculations is the quickest way to glean insight into a design. The toolset available to microfluidic designers is a little different than pulling out a Moody diagram and calculating your pressure drop in a pipe. However, in many instances, the fluid interaction challenges are more easily solved, which can be attributed to the very low Reynold’s Number found in these systems. As fluid flow becomes dominated by fluid viscosity, the uniformity of the flow fields becomes predictable and simplifications such as Stokes Flow and pressure drop calculations may be applied. Where things start falling apart is with the unique properties of microfluidic systems. Phenomena associated with particle-particle, particle-solid, free surface, and multiphysical interactions are still possible to calculate, but the analysis complexity become higher and the confidence in results becomes lower. Microfluidics also plays host to very specific phenomenon like Electrowetting and Marangoni effects whereby electrical and density gradients interact with surface tension to influence flow properties that can make first principles calculations even more challenging.
Tool #2 – Multiphysics Modeling An alternative to in-house
Multiphysics modeling is the use of high end Finite Volume or Finite Element Analysis Software, such as FLUENT, ANSYS and COMSOL. Each of these packages have strengths and weaknesses associated with them – with particle and surface interactions generally being claimed as expertise fields for FLUENT (with ANSYS as a complimentary package), and integrated multiphysical analysis generally being claimed as COMSOL’s territory. The time and cost to set up and optimize a model of this nature is extensive, and physical models will likely be required in order to verify assumptions in the model setup. Once a model has been verified, optimization of critical geometric features, electrical frequencies, and/or other key features, can be quickly iterated In Silco. A few key tips when considering Multiphysical Simulation’s include:
- Verify your results with simple physical models early and often
- Clarify if your software package will model particle interactions and/or specific physical phenomena of interest. Be specific in posing questions to 3rd parties.
- Defer sophisticated or fully integrated prototypes until you have a solid understanding of your physics and have verified with simple mock-ups.
- Do not expect your expensive software package will ‘do it all for you’. The software is a tool – you still need an expert at the tiller.
Tool #3 Ballpark it and Iterate
Depending on the phenomenon you are trying to exploit, a Monte Carlo approach with the myriad of rapid prototyping techniques available today may be the fastest and most cost effective method to prove out designs. Suitable prototyping techniques may include cut paper stock, laser or knife cut plastic sheets, Micro-SLA, or possibly soft lithography with a PDMS transfer. Accompanying electronics are also well suited to be utilized as a part of the flow channel or support structure. Fluid movement in prototypes is often achieved with syringe pumps, Compact Disk like cartridges, or off the shelf microfluidic pump elements. Don’t throw out the textbook when deciding on permutations, reason out what should intuitively work and observe the results and bracket accordingly. A few keys to success include:
Utilize a clean room or laminar flow hood during assembly to reduce unwanted artifacts
Develop appropriate metrology early and ensure it is properly validated and calibrated to recognized standards
Pay close attention to surface tension of prototyped materials versus production materials
Conclusion
Using the high level tips provided above, I’m sure you’ll be “stoked” about using microfluidic development tools in medical devices. And when in doubt, remember Steve Jobs: ‘Innovation distinguishes between a leader and a follower’.
Mark Drlik is the Concept Development Manager at StarFish Medical. He is a strong advocate of using microfluidic development tools to design medical devices.
Image: wikipedia