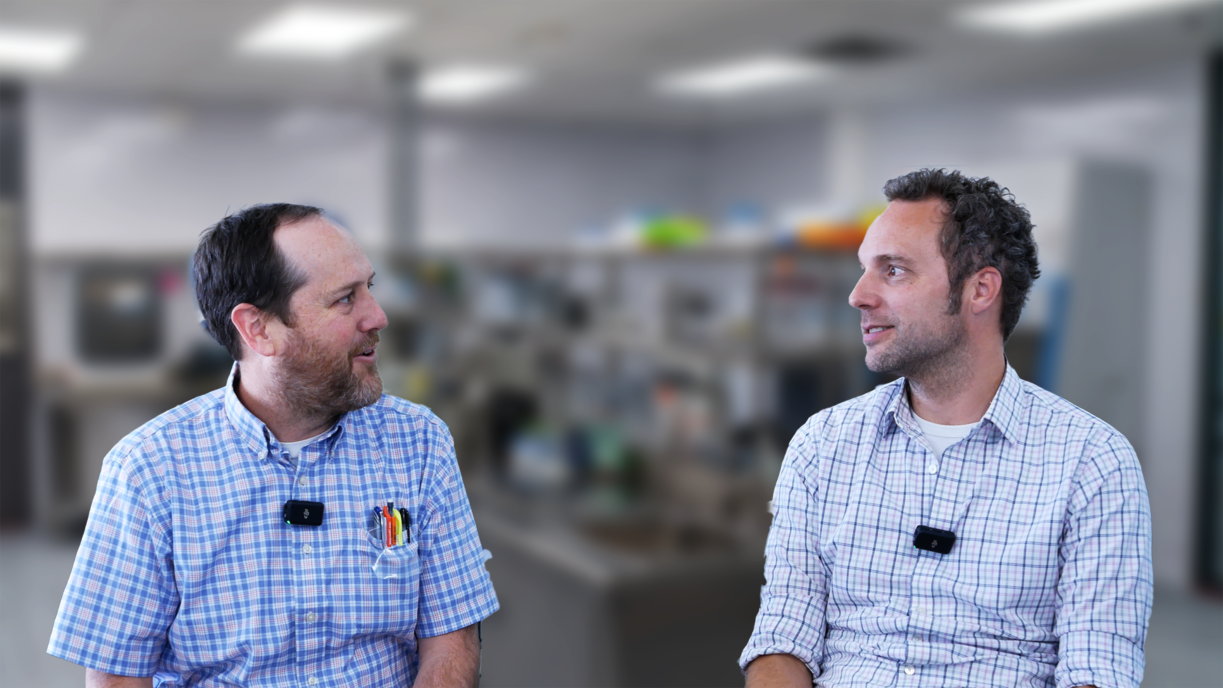
Bio Break: Achieving a 20-Year Resolution – Biofilm Testing Standard
In this special New Year’s episode of Bio Break, Joris van der Heijden and Nick Allan reflect on resolutions, persistence, and a 20-year journey to establish a new standard for biofilm testing in medical devices.
Nick shares the story of his two-decade-long mission to develop a standardized test method for growing and monitoring biofilm on medical device surfaces. This effort, initiated through the ASTM E35 Committee (American Standard Test Method Organization), recently culminated in the release of ASTM Standard E3435. This method enables researchers and developers to evaluate biofilm growth and assess the effectiveness of materials designed to inhibit or prevent biofilm formation—an essential consideration in medical device development.
Nick showcases a prototype from 20 years ago that played a critical role in this process. The device uses loops of various catheter materials, some treated with antimicrobial agents, to test biofilm growth under controlled conditions. This tool allows developers to measure the performance of materials against biofilm formation, offering a reliable way to test and improve medical devices.
Key takeaways from the episode include:
- The importance of standardized testing in ensuring the safety and efficacy of medical devices.
- How the ASTM E3435 standard supports innovation by providing consistent methods for evaluating biofilm interactions with materials.
- The value of persistence and long-term vision in bringing impactful projects to fruition.
This episode highlights the critical role of biofilm testing in advancing medical devices and the dedication required to turn a passion for innovation into a tangible outcome.
Whether you’re a medical device developer, materials scientist, or healthcare professional, this episode offers valuable insights into the process of creating industry standards that drive innovation and improve patient outcomes.
Achieving a 20-Year Resolution – Biofilm Testing Standard
Related Resources
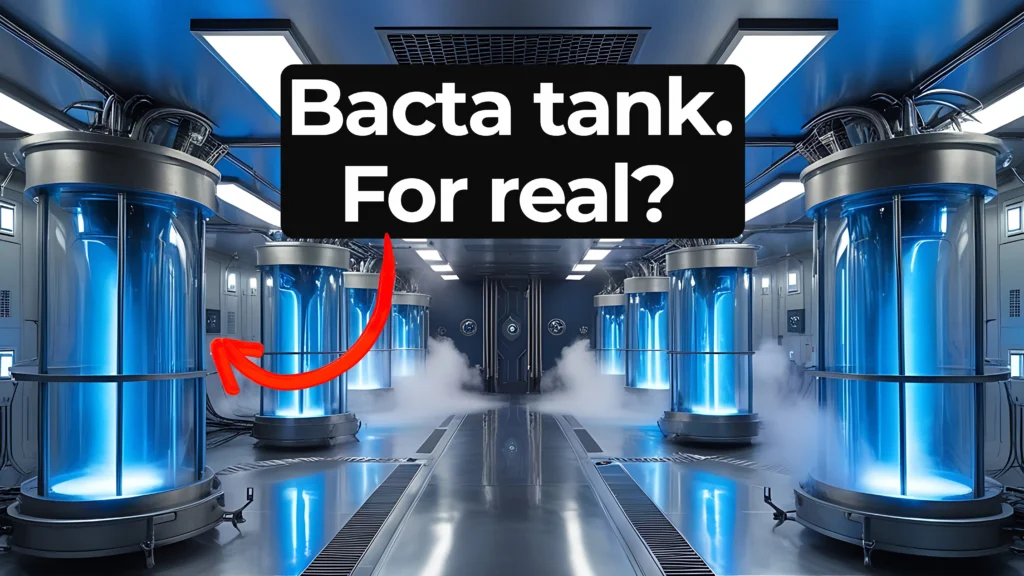
Ariana Wilson and Mark Drlik take inspiration from a scene in The Empire Strikes Back to talk about real-world parallels to the Star Wars bacta tank.
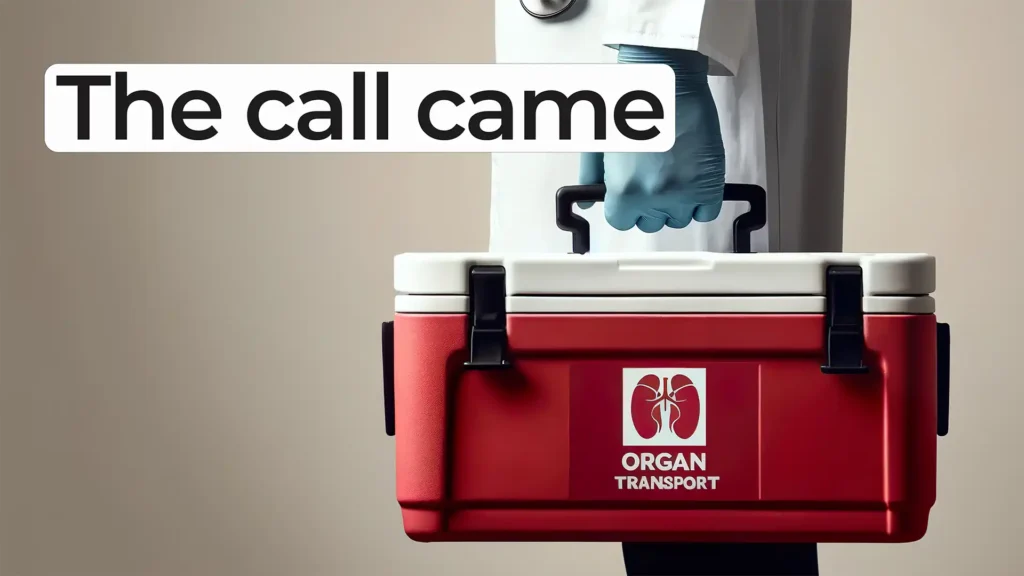
In this Before the Build episode, Eric Olson and Paul Charlebois dive into the importance of organ transplant logistics when designing effective medical devices.
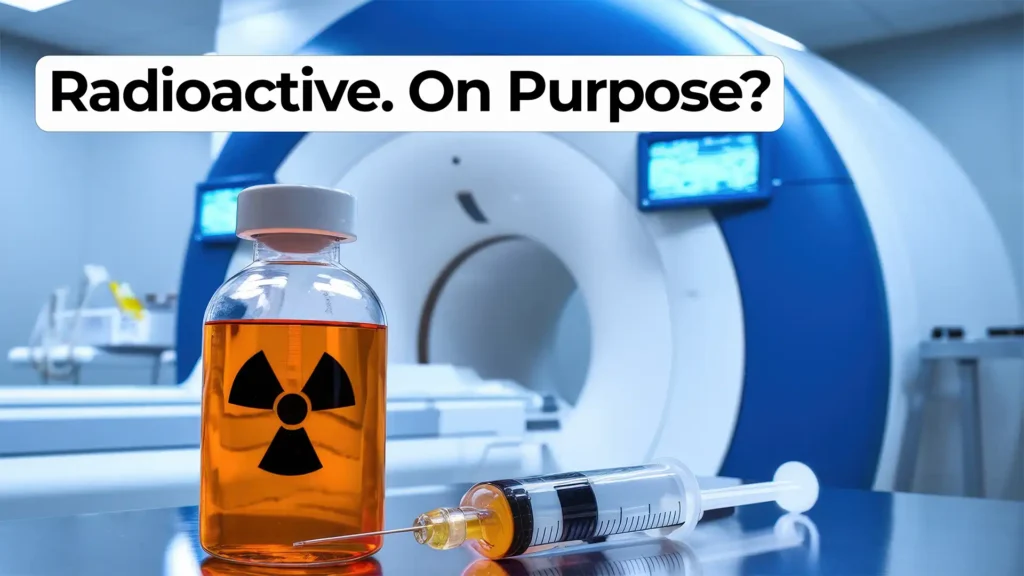
Radiopharmaceutical device development is gaining momentum as medical teams explore new frontiers in diagnostic imaging and cancer treatment.
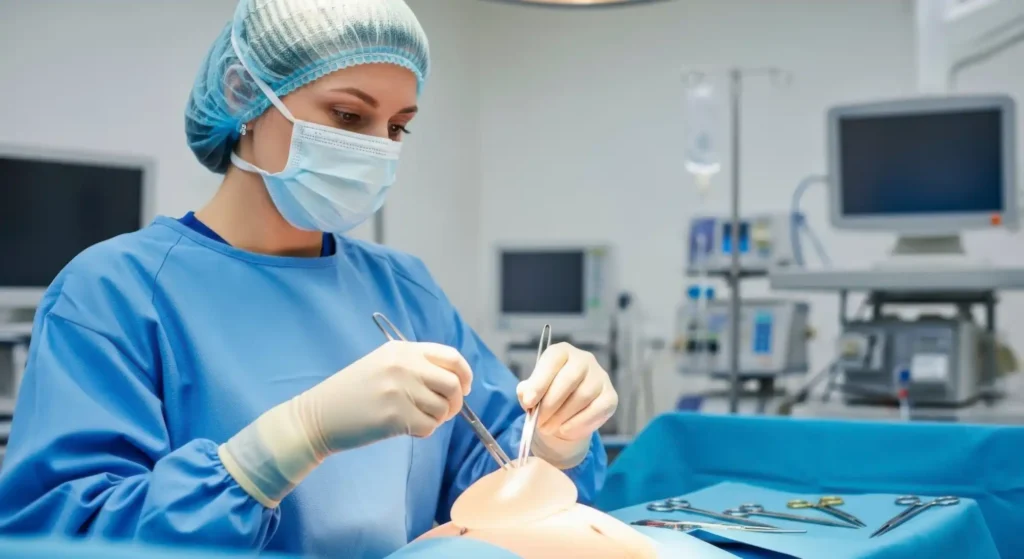
The simplest and least expensive way to train users of medical devices is to ask them study the Instructions for Use (IFU) beforehand.