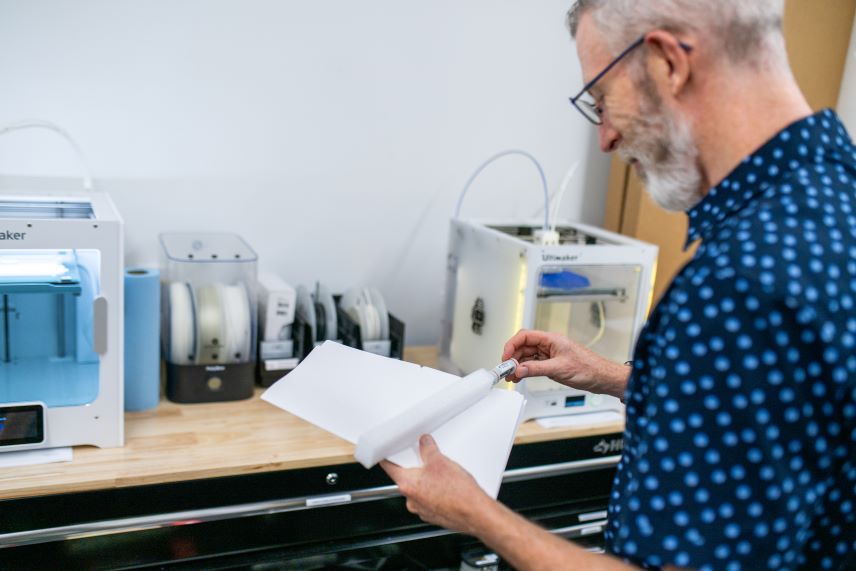
ESG Medical Device Impact
As major buyers continue to request Environmental, Social and Governance (ESG) reporting from suppliers, there will continue to be new and revised regulations requiring supply chain attention. Jurisdictions all over the world are increasingly enacting regulations aimed at curtailing the use, import and/or export of certain substances in response to political, environmental and social responsibility concerns. These regulations have far-reaching implications for designers, manufacturers and importers of complex Medical Devices and related equipment.
Whether you are a raw material processor, substance or part manufacturer, product designer, importer or OEM, this blog offers a few tips to fulfill compliance obligations.
What is the current climate? Consider the ESG medical device impact of the following regulations and recommendations:
- The European Union’s REACH legislation (Registration, Evaluation, Authorisation and Restriction of Chemicals) came into force in 2007 to limit and eventually eliminate the importation and use of certain substances within the EU. While the framework has been around for a while, new substances of concern are included every six months;
- The European Union’s Restriction of Hazardous Substances (RoHS) Directive, adopted in February 2003, seeks to limit the amount of hazardous chemicals in electronics, and many other countries have enacted similar restrictions;
- The state of California’s Proposition 65, requires businesses to provide warning labels on products if they contain chemicals known or suspected to cause cancer, birth defects or other reproductive harm, and prohibits California businesses from knowingly discharging significant quantities of these chemicals into sources of drinking water;
- Extended Producer Responsibility (EPR) Regulations: In Canada, various provinces have enacted legislation that extends product packaging manufacturers’ responsibilities into the post-consumer stage of a product’s life cycle. This means that manufacturers need to take end of life considerations (recycling, disposal, servicing) into account when designing their products.
- The OECD (Organization for Economic Cooperation and Development) Due Diligence Guidance for Responsible Supply Chains of Minerals from Conflict-Affected and High-Risk Areas (the “Conflict Minerals” policy) was developed to help companies avoid contributing to conflict through mineral sourcing practices primarily for tin, tantalum and tungsten
Tips to ensure you meet the ESG medical device impact of compliance obligations:
- Know the product market
To understand your obligations, first understand where the products are being sold, imported, and used. Does the device have a worldwide reach, or does it focus on a niche industry or a limited geographical footprint? Some regulations are confined to individual countries, states or continents. If the product does not reach those areas during its lifecycle, then consider whether any regulations in place in those areas need to be addressed. Because this can be difficult to keep track of due to changing market strategies and regulations, many companies choose to be regulatorily compliant on a global level. - Understand the regulations that apply to the goods
If you frequently build, design or trade in Printed Circuit Board Assemblies (PCBAs), chances are you are already quite familiar with RoHS, since this directive is aimed primarily at the electronics supply chain. However, California Prop 65 is not a concern if the products are not intended for human contact or likewise not used in food and beverage, water or wastewater conveying applications. Note that if there is a chance the components within the product (such as plastics) could potentially discharge chemicals over a longer period of time after disposal in a landfill, then Prop 65 compliance could become an issue.
For more information on how RoHS regulations apply to medical device development, refer to this StarFish RoHS blog. - Have visibility into materials used in the device
Maintaining complete visibility into the Bill of Materials (BOM), including component serialization and lot traceability, is no longer a ‘nice to have’. It is a necessity from a risk management perspective, whether driven by the regulatory environment or not. If regulations change and suddenly some components are or will be at risk, know where they have gone. - Supply Chain Roles and Responsibilities
In the complex multi level supply chains for medical device manufacturing, an organization usually does not have the necessary internal resources to investigate their entire upstream supply chain for compliance. Instead, it is common practice for manufacturers to request that their upstream suppliers provide this information as part of their part or material certification process. Sharing this blog post is useful in helping suppliers who receive a request understand their customers’ needs. - Organize and share compliance information, and be prepared to review and make updates
A Greek philosopher is credited with first saying “the only constant in life is change”. Just as the ancient Greeks contemplated the changing environment around them, prepare for change in your products and components. Regulations will receive updates, chemicals that previously were acceptable for use will be discovered to be problematic, raw materials will be obsoleted and component designs will be revised. Check the compliance status of component BOMs on a regular basis, and ensure suppliers do the same.
Despite the daunting nature of this assignment, there are tools in the marketplace designed to help all parties in the supply chain manage the ESG medical device impact and related regulatory compliance. Web based platforms provide a centralized repository for part compliance information, enabling compliance data for complex standardized components (think diodes, resistors, processors) to be shared in a secure fashion all along the supply chain simultaneously.
At the same time, bespoke custom designed part data can be uploaded and shared to all downstream stakeholders. Some platforms also offer managed services as part of their portfolio, reaching out to suppliers on your behalf and helping them to upload and manage their own part compliance declarations within the platform. These services excel at monitoring and communicating changes to the regulatory landscape, including new and revised regulations, new chemicals under review, increases or decreases in notification thresholds, and other changes of interest to their customers.
It may seem like a daunting prospect to ensure medical device products comply with the myriad of regulations that exist in the market; but with a little planning, cooperation with suppliers and some compliance tools, you can avoid unwanted regulatory surprises and prevent costly delays in bringing products to market.
Supplier Quality Management for Modern Medical Device Commercialization
Sean Mitchell is a StarFish Medical QA/RA Specialist. He works with quality assurance, manufacturing and supply chain teams to optimize business processes, identify best practices and make improvements within the supply chain and manufacturing.