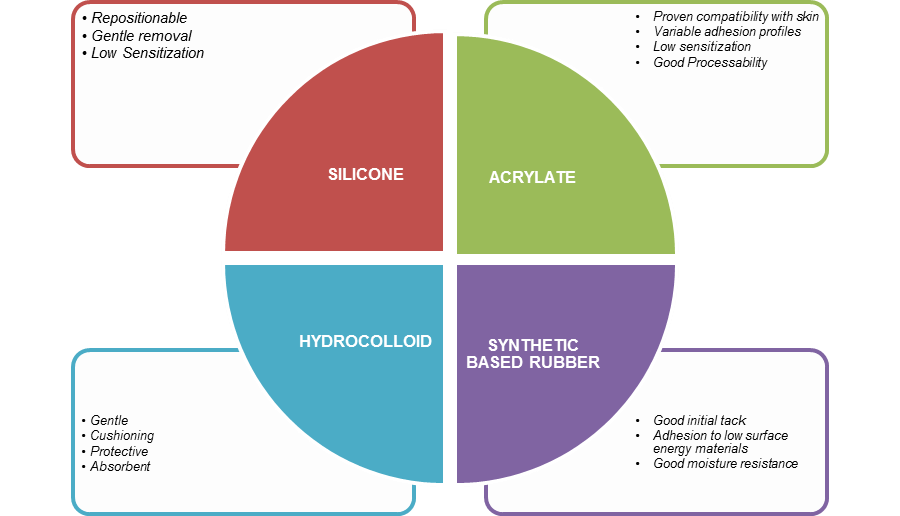
Selecting wearable medical device adhesives
Understanding the Basics of Wearable Medical Device Adhesives
Selecting wearable medical device adhesives requires a solid understanding of the basics of adhesive. Sticking a medical device to skin is not as simple as it sounds. Numerous variables come into play such as the patient’s age, gender, race, diet, activity, skin condition, and climate. Other variables include the stretchability of the skin, contours of the body, perspiration levels and how much hair the patient has at the fixation site.
But wait, there’s even more. Wear time and load requirements will have an effect as well. This is a consolidation of my three-part blog series covering selecting wearable medical device adhesives, the dos and don’ts of developing a skin-worn wearable medical device and the science of sticking to skin.
It is impossible to become an adhesive expert overnight. Thankfully, there are industry adhesive experts ready to provide material recommendations that will meet your product requirements. Directly contacting representatives of 3M or Avery Denison is an option.
Another is to contact a contract medical device manufacturer that specializes in adhesive converting and manufacturing. They will have an adhesive expert to discuss your device and its requirements. It is good to get them involved early in the ideation phase. These experts know what is feasible and what is not. They will make recommendations based on your performance and Cost of Goods (COG) requirements.
In addition to the 3M and Avery Denison brands, there are many other options offered at lower prices. These vendors often have helpful samples in stock, and they will work with your design team to design and make prototypes. Once the design is finalized they will source the adhesives from their supplier then die cut, attach liner, assemble, and package according to your specification.
Prior to speaking with an adhesive manufacturer, it is helpful to know the commonly used terms and the basics of adhesives.
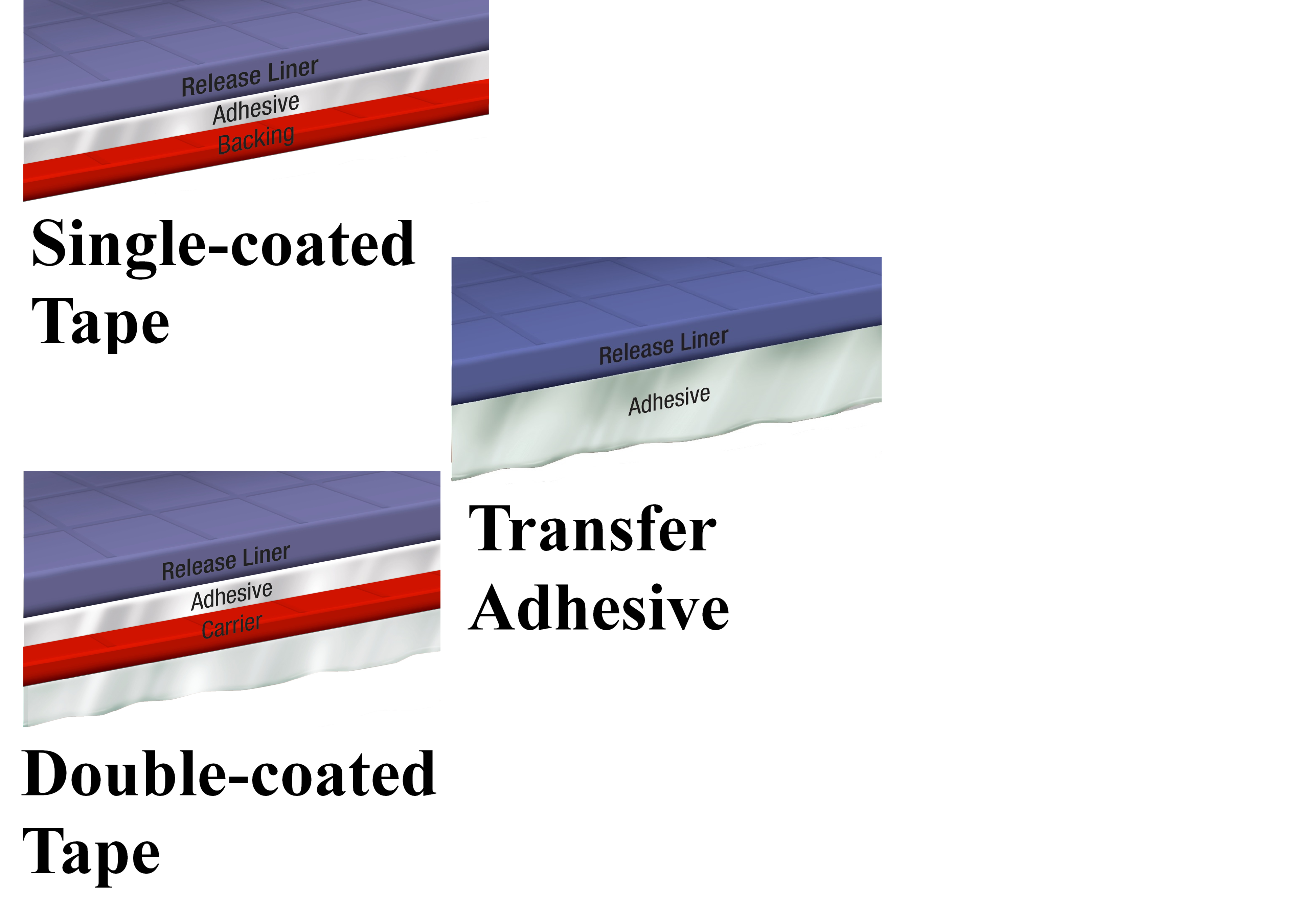
Different Configurations of Adhesives (Tape):
Pressure-sensitive adhesive (PSA) is used for adhering a device to the skin. It only requires light pressure to bond with a surface. PSAs come in different formats such as transfer tape, single-sided, and double-sided as seen in figure 1. Single-coated tapes have a PSA layer laminated to a carrier (also known as a backing) on one side and a removable liner on the other. The carrier can be a wide variety of materials such as foam, textile, woven, non-woven and more. Transfer tapes consist of a PSA layer and removable liner.
Double-coated tapes feature two layers of PSA laminated to either side of a carrier and protected on one side by a removable liner. Double-coated tape is commonly used for attaching a device on one side and to skin on the other. The adhesive on the side that attaches to the device can be more aggressive than the adhesive on the side that attaches to the skin.
Types of Adhesives:
There are four categories of adhesives commonly used today. Each has its own pros and cons and performs differently over time when worn on skin.
A summary is presented in figure 2.
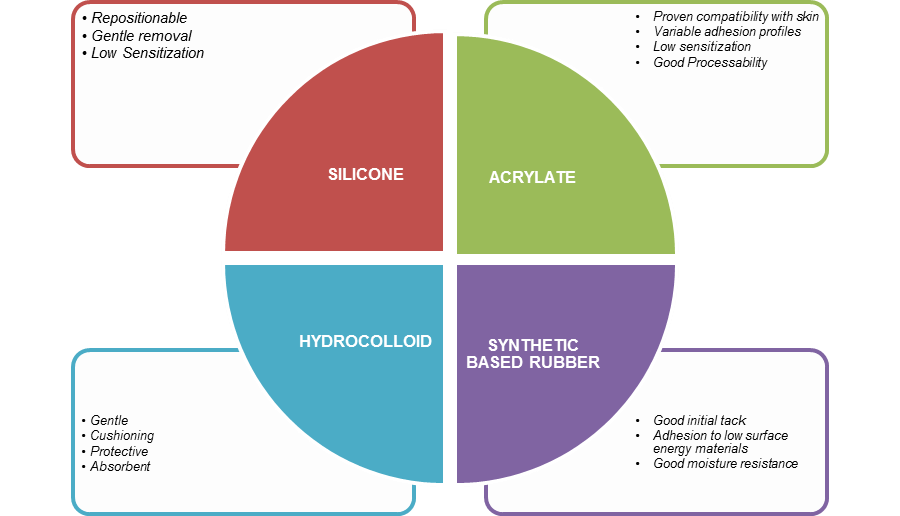
Adhesion Level:
Another factor to consider is the level of adhesion. The adhesive must be strong enough to adhere well, but must release without causing trauma to the skin. Strength tests are done to measure the peel, tack, and shear strength. The results are found in the specification sheet of the medical tape. Adhesivetest.com has a definition for each component of testing.
Here are a few definitions from the site:
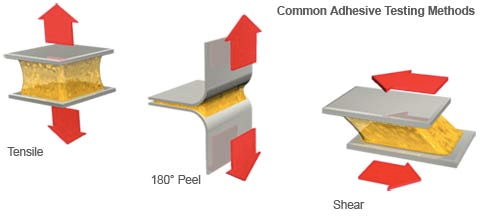
Peel Adhesion – the force required to remove a label after a length of time, at a specific speed, and at a 180 or 90 degree angle. This measurement is usually measured in pounds/inch. (Figure 3)
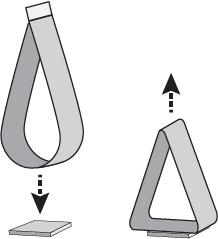
Loop Tack – a looped label sample with the adhesive on the outside is lowered into contact with the test substrate, relying on facestock stiffness to regulate force applied. The label is removed and the force required to remove the label is measured in pounds/inch. (Figure 4)
Static Shear – A test sample is cut with a liner folded back on one end. The exposed adhesive is attached to a stainless steel panel and placed in a grip with the label facing down and a 250 or 500 gram weight suspended from the label. (Figure 3)
There are no magic numbers for adhesion specification that work for every use scenario. Variables such as the patient’s age, gender, activity, skin condition, and etc. will determine which adhesive is most appropriate. The specification data allows you to compare different adhesive options.
Transepidermal water loss:
If the device is to be worn for longer than a brief moment, moisture handling is another factor to consider. Transepidermal water loss is a natural occurrence of water that passes from inside a body through the epidermal layer (skin) to the surrounding atmosphere via diffusion and evaporation processes.
The skin’s natural transepidermal water loss will cause excessive hydration of the skin underneath if the moisture cannot be transmitted. The moisture vapour transmission rate (MVTR) describes the breathability of the adhesive. In general the MVTR has to be greater than 500 g/m2 per day to be considered breathable. The level of breathability required depends on the user’s gender and the location of the fixation site. For example, women generally lose more water than men and certain body parts (such as hands and foreheads) have higher water loss.
There is a lot of information to consider when choosing the right adhesive for a stick-to-skin device. It is not a task to be taken lightly. Selecting the right adhesive is critical to the performance, wear time, comfort, and success of the device.
5 things to do when designing a wearable medical device
Although timing is critical for technology based devices, what is more important is to review and address any high risk issues carefully during each step of development to ensure a successful design. It is much easier to make changes in the beginning rather than make costly fixes later in the development.
In this section I explain the dos of skin-worn medical device design and development.
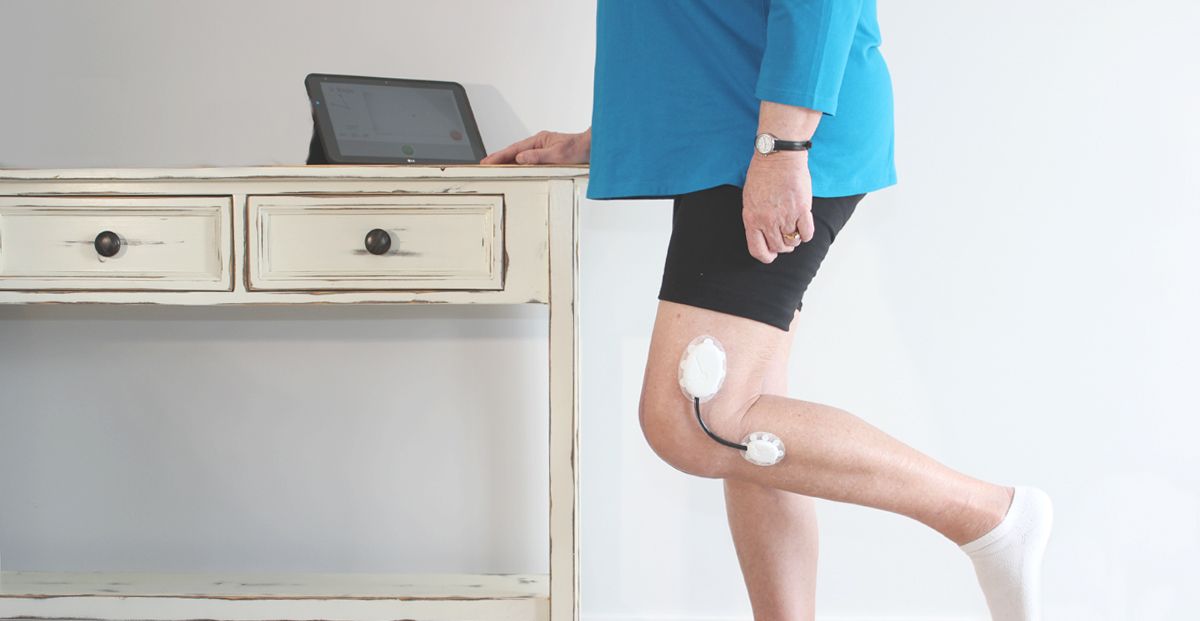
Do
Research the user population first thing and define the use scenarios and appropriate workflows that blend into their current daily lives or current protocol for procedure.
User demographics, diets, skin types, common skin diseases, body hair, gender, wear time, level of activity, placement (such as a joint or a flexible site), size of the contact area, climate (region), chance of exposure to liquid (such as water, sweat, blood, and etc.) of the target user population are all critical information that need to be collected before the design of the device can begin. These factors will drive the features of the device, how the user interacts with it, how it looks, how it will be manufactured, and the adhesive choice.
Do
Facilitate an open line of communication between your industrial design/human factors engineering team and electrical/firmware and software engineering team.
What kind of data and how much will the device collect? Does the data need to be transferred to a separate viewing device? If so, what type of connectivity will it have? What type of battery should it use? Does it need to be recharged or will it be disposable? Is flexible circuitry an option? The processing power, power consumption, and wireless communication requirements will affect the size of the device and workflow for device use. Layout of electric components will influence the geometry of the device. The two teams must work together to prioritize performance requirements, agree on the electrical component size and layout in order to create a device that have the overall appropriate size, form and user interface layout.
Do
Determine if the device should be completely disposable or reusable.
Will it have consumable parts? Should it be refurbished? If so, what is the protocol for collecting the used devices? The workflow research conducted in the beginning of the development will shed some light onto whether the device should be disposable or rechargeable and whether it needs consumable (disposable) parts or not. The decision you make will have an impact on the workflow. The goal is to create a device that does not disrupt or intrude current workflow of the procedure. If the device is for long-term wear, it should not be intrusive to their clothing choice and the daily activities of the user.
Do
Start connecting with adhesives vendors to source the right adhesive for your device.
There is no such thing as a “miracle go-to adhesive” suitable for all skin-worn devices. Different adhesives (such as acrylic, silicone, hydrocolloid, or synthetic base rubber) have different characteristics appropriate for different uses. There are a variety of choices for carrier (backing) material (such as nonwoven, foam, vinyl, polyurethane, polyethylene and many others) as well. It is important to define your user population and scenario and discuss them with your vendor.
The vendor can then help you decide on the right adhesive. At StarFish Medical we have working relationships with adhesive vendors who source from variety of adhesives manufacturers such as 3M, Avery Dennison, and etc. They work with us to customize, prototype, and die-cut the adhesives. The adhesive must be strong enough to conform to the contours of the body and stay secure, but must be gentle enough to minimize trauma to the skin when it is being removed. Finding the right balance is tricky. That is why it is important to speak to the experts to help identify the most suitable adhesive for your application.
Do
Make sure all components that have direct or indirect contact with skin are biocompatible.
News about massive recalls due to skin rashes tainted the brand image of Fitbit in 2014. In August 2016, McDonald’s had to recall 33 million wearable fitness trackers due to skin rash and burns. Both are wristbands designed to be worn throughout the day. Skin-worn devices pose unique challenges when it comes to biocompatibility.
Some areas of the body are more prone to sensitivity (face, eye areas versus feet) and some age groups have more fragile skin (seniors and infants vs. healthy adults). Natural rubber-based (“latex”) compounds, nickel in metal alloys, plasticizers are commonly known skin allergens and irritants. All these factors should be taken into consideration when choosing materials for sensors, adhesives and any other components that may come in contact with the skin.
Next Up: Don’ts for wearable medical device design
In this section, I will go over the list of don’ts for wearable medical device design and development to prevent costly fixes that may arise later in development.
Don’t
Don’t develop the device and required accompanying application independently from each other.
Device development team and app development team need to collaborate with each other to create a workflow that is coherent. Also, the design of the device and the Graphic User Interface [GUI] should look like they belong together as a system. Do the form, colours, material, finish, and user interface elements of the device tie in well with shapes, colours, and design language of the app GUI design? Does the design language of both align with the client’s brand identity?
Don’t
Don’t forget to conduct user wear testing.
Standardized bench testing and bench testing using skin proxy are great ways to collect information but having real people from the target user population wear the devices for the intended duration under intended conditions will provide better insights and challenges that you might not have discovered otherwise. You want to address and mitigate all issues before the product launch, not after. In addition, interacting with people from the target user population allows designers the opportunity to connect and grow their empathy for the users. Empathy is a strong design tool.
Don’t
Don’t just focus on technology first and put off industrial design and human factors engineering until later.
Wearable devices are a fairly new product category. Research done by Endeavour Partner in 2013 shows that a third of consumers who purchased a wearable fitness tracker (Jawbone, Fitbit, Nike, Misfit, and etc.) stopped using it within six months. More than half of the consumers stopped using it within two years. Even if you succeed at developing a novel technology, if you can’t find a way for the users to adopt it then you have a failed product.
Usability research needs to start from the very beginning. We need to find out what is the easiest, approachable, and non-intrusive way for the device to be adapted into the current standard protocol if worn during a procedure or the user’s daily life. Get industrial designers/human factor specialists involved from the beginning. By gaining a deep insight into the user’s daily life activities, lifestyle and emotional state, designers will be more equipped to creating a wearable medical device that makes users feel comfortable physically and physiologically and is enjoyable to use.
Don’t
Don’t push off packaging design until the very end.
Packaging can be incorporated as a part of the workflow of the device. Packaging does not necessarily need to be just a box that protects the device during transit and then gets thrown out. It can be incorporated as a part of the system to eliminate steps in the device use process or function as a charging dock.
We have designed devices that get automatically activated or powered on when taken out of their packaging. It may eliminate a power button, saving precious real estate on small devices. Designing the packaging to work as a holder or charging dock when the device is not in use give it another purpose and saves materials from ending up in garbage.
Don’t
Don’t forget to assess if the chosen adhesive material is compatible with the packaging, cleaning, and sterilization method if any.
Does the device need to be sterilized? Silicone adhesives deteriorates under gamma sterilization. Ethylene Oxide is usually gentlest on tape or film as backing material. Autoclave is not suitable for polyethylene based tapes. Does packaging involve a heating process? Characteristic of adhesives and backing material can change under heat. Are there chemicals used during after use cleaning process? Once again, adhesives and backing material can react differently to different chemicals.
Don’t
Don’t put off talking to a regulatory advisor about your device.
Besides dealing with FDA, REACH, and RoHS compliance issues as a medical device, skin-worn devices have to follow the standard of ISO 10993-1 for biocompatibility evaluation. Regulatory advisors will provide valuable guidance on pricing, timeline and types of testing needed. Even if a material has been tested by the manufacturer and is described as “medical grade” or “biocompatible,” it needs to be tested as a whole device.
Each use scenario is unique. Adhesive, plastic housing, sensors, and other components of the device can react differently under different use conditions. In addition to biocompatibility issues, regulatory advisors can provide information that may influence what features to add to the accompanying app if it has one.
Wearable Medical Device and Adhesives
The global wearable medical devices market should reach $83.9 billion by 2026 from $20.1 billion in 2021 at a compound annual growth rate (CAGR) of 33.1% for the forecast period of 2021 to 2026 according to BCC Research. I hope this blog has helped you understand the key success factors in designing, developing wearable medical devices as well as the importance of selecting appropriate adhesives.
Christine Park is a former Industrial Designer at StarFish Medical where she uses her knowledge of usability, colour, material, finish and emotion to design innovative medical devices for clients.
Images: StarFish Medical