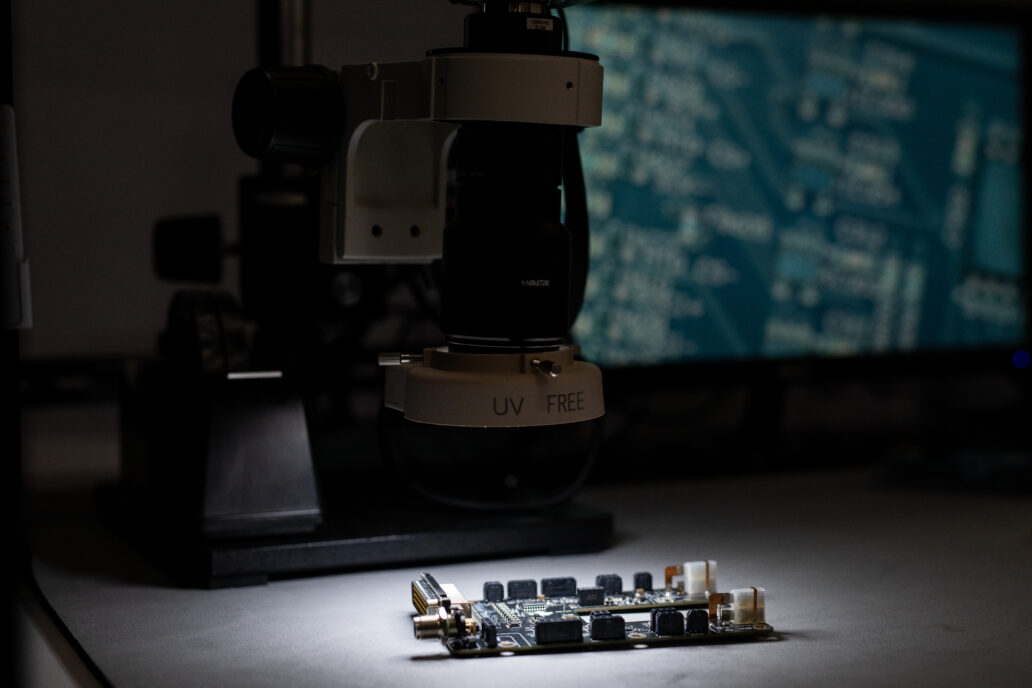
Re-use IVD Verification Test Equipment in Optics Manufacturing QC
Transfer to manufacturing is sometimes overlooked during the medical device product development program. The FDA 21 CFR 820.30 requires manufacturers establish and maintain procedures to ensure that the device design is correctly translated into production specifications, and ISO13485 (required for Health Canada and Europe) requires transfer activities to be planned under section 7.3.1. Reuse IVD Verification Test equipment for verification of In-Vitro Diagnostic (IVD) optical components as part of manufacturing quality control.
We developed a sensor which incorporated an LED emitting part and a PIN diode detector. We needed to verify that the wavelength, power, and spectral purity were to specification, and the photodiode sensitivity and dark current also met specification.
During Phase 0 ā Proof of concept, we performed a first attempt at confirming optical power by mounting the LED on an optical table in a dark room. Assuming a beam distribution pattern, we used a power meter mounted a preset distance from the LED in order to measure the detected optical power as it intercepted the emitted beam over a certain number of steradians. This was a low cost way for getting a first approximation of optical power.
To properly measure the power for verification, we needed an integrating sphere with a power meter sensor calibrated to the sphere. We reduced waste by purchasing a four-port integrating sphere. Note: the larger the better, as too small of an integrating sphere results in positional sensitivity. We then connected a spectrometer (precision 0.2nm) to one of the access ports and a pure Neon bulb to another port.
The Neon light source enabled a calibration check of the spectrometer to be performed at every session using NIST published tables of optical emission peaks for neon. The two remaining ports were used for the LEDs and the PiN diode for the device under test, which were installed into the final product as matched sets.
The same equipment is reused during manufacturing quality control. During incoming inspection the LED was energized with a predefined current. The power meter detected whether the LEDs emitted sufficient power. The same LED was then set for a given optical power using the adjustable current source, and the PiN diode output was measured to determine its sensitivity. Finally, the LED spectral purity was checked using width and centroids, not peaks, as LEDs often have asymmetric wavelength spectra.
The benefit of this system was that it was relatively easy to keep in calibration, as all that was required was a calibrated current meter to measure LED current, and the power meter to be periodically calibrated, as opposed to requiring reference light sources for both power and spectrum. The system was automated using a LabView front end which used the spectrometer and power meter OEM developer DLLs to generate test records with time and date, without having to use several different software packages.
A one-time system validation was performed in the usual manner by developing requirements, then proving the requirements have been met with reference sources.
This system works well in the early stages of manufacturing, as it is preferable to functionally test all critical components as part of incoming inspections to make sure they meet specification, and ensure the supplier meets their qualification obligations.
Later, when the supplier relationship has matured, one can rely on the supplier Certificate of Conformity (CoC), final inspection and test of the whole device, and random sampling of batches.
Planning ahead to avoid separate steps in development and manufacturing a cash strapped entrepreneur can reduce costs. Re-using IVD Verification Test Equipment in Manufacturing QC is one way, Iād enjoy hearing other ways from readers.
Vincent Crabtree, PhD is a former Regulatory Advisor & Project Manager at StarFish Medical for Medical Devices.
Image: 0462435 / gashaf – CanStockPhoto