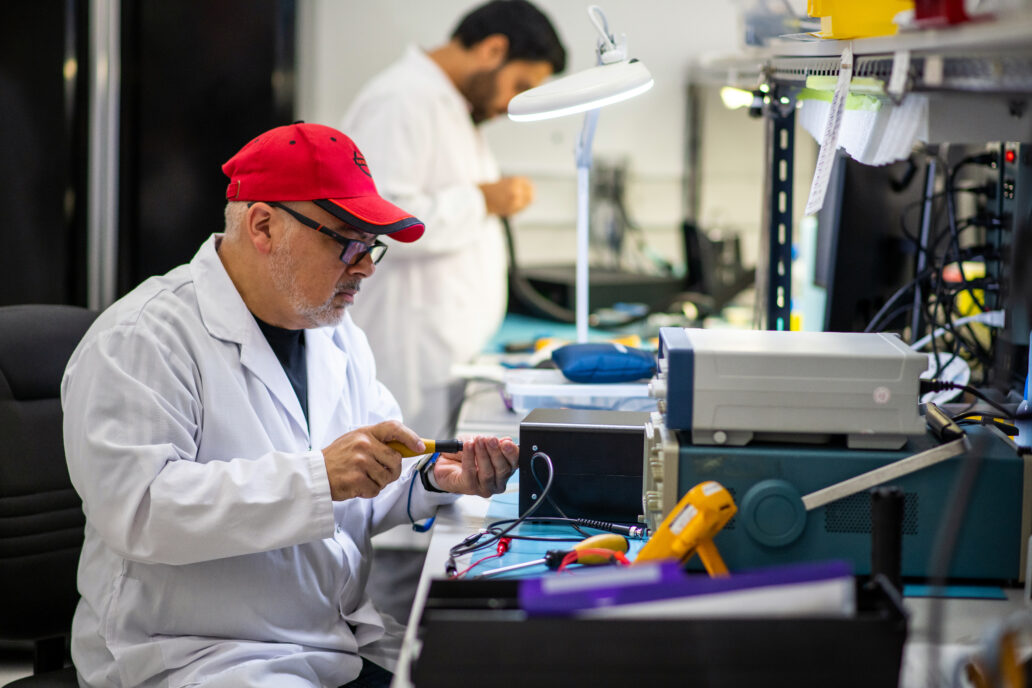
New Product Introduction
Develop a product that’s ready for manufacturing and commercial launch
Prepare to launch.
Transform your vision into a safe, functional product that meets a defined market need.
From initial design to the first manufacturing run, StarFish Medical employs cutting-edge new product introduction (NPI) strategies to deliver products that truly serve patients and clinicians. By performing all activities in-house, we ensure a streamlined, lower-risk process when transitioning to full production. Our unwavering focus on cost control, resource allocation, and overall efficiency guarantees consistency, positively impacting cost, timelines, and quality. With StarFish Medical, you can confidently navigate the complexities of product design and development, knowing that our expertise and dedication will help you succeed.
![]()
Michael Baker
CEOOtoharmonics Corporation“I am extremely happy with StarFish support while setting up a QMS for Otoharmonics and the Levo System tinnitus sound therapy device. I’ve worked with a lot of QMS people in my life and the StarFish team are the most helpful and easy to work with.”
![]()
Ian Maclean
Project ManagerKoven Technology Canada"I commend you for your vision in looking well ahead to regulatory and contract assembly issues, as well as a decision to concurrently develop key prototypes. This ultimately led to a successful design concept. All initial design requirements were satisfied."
![]()
Erik Henne
Vice President of Research and DevelopmentUptake Medical“StarFish in one word? “Boutique”, that really means “Bespoke”. We are ourselves a boutique medical device company. We are very focused on single product platform. We are not a giant diversified company, but we have important things happening here and the size and scale of StarFish matches our size and scale.”
What is New Product Introduction for Commercialization?
New Product Introduction / NPI is a comprehensive activity that spans the entire medical device design, development, and validation process to prepare for commercial-volume manufacturing. Both a process and a plan, NPI typically begins in the design stage and may continue through the first production run. Think of NPI as a crucial bridge to manufacturing, ensuring a smooth transition from concept to market-ready product.
Why Do I Need NPI?
Manufacturability of a device is often overlooked and can be a blind spot for development teams. Preparing a device for commercialization involves developing a supply chain, qualifying vendors, sourcing parts, and preparing for regulatory clearance/approval. All these activities take time, but they are essential for successful commercialization.
NPI and product development teams work together to ensure engineers have everything they need to consistently and reliably reproduce the prototype. By introducing the concept of manufacturability at the right time during product development, medical device companies can avoid costly mistakes downstream.
Medical device innovators that leverage NPI move their products through to first production runs with fewer delays and missteps—missteps that could lead to usability or quality issues. By following design for manufacturing (DFM) principles, NPI leads to lower costs and faster time to market. Without NPI, a medical device may reach manufacturing with a design that isn’t suitable for repeatable processes, resulting in costly redesigns and extended timelines. With consistent NPI processes, the focus is on manufacturability, traceability, audit readiness, risk management, and patient safety, all of which are essential for a market-ready product.
How StarFish Medical Digs Deeper into Commercialization
Innovative Commercialization Outcomes for Our Clients
Medical device innovators partner with us to overcome commercialization challenges and bring breakthrough products to market. Here are a few examples of how our new product introduction / NPI-driven approach delivers real-world results.
Why Companies Choose StarFish Medical
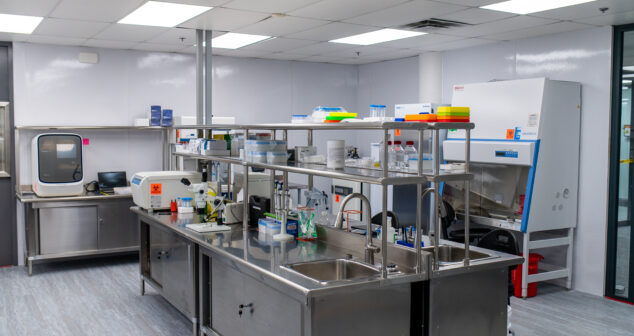
A Controlled and Compliant Manufacturing Process
Our manufacturing facility is ISO 13485 certified and compliant with FDA Quality System Regulations (CFR 820).
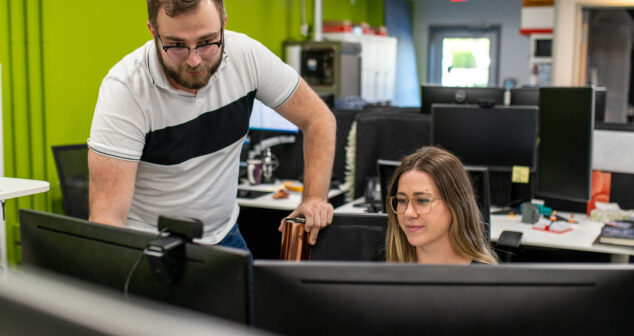
Your Milestones, Our Mission
We align our deliverables with your milestones, whether for preclinical trials, clinical trials, or fundraising rounds.
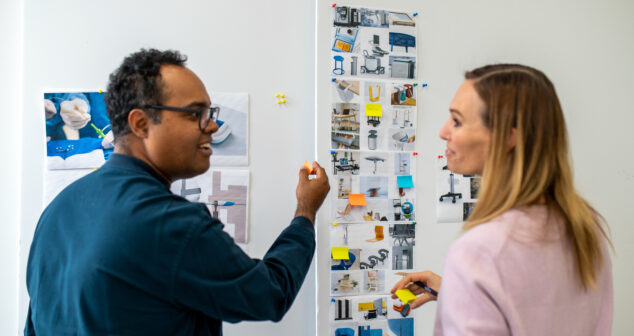
Design for Seamless Manufacturing
Our design-for-manufacturing process ensures your product is ready for manufacturing and assembly, with support for clinical trials and transfers to contract manufacturers.
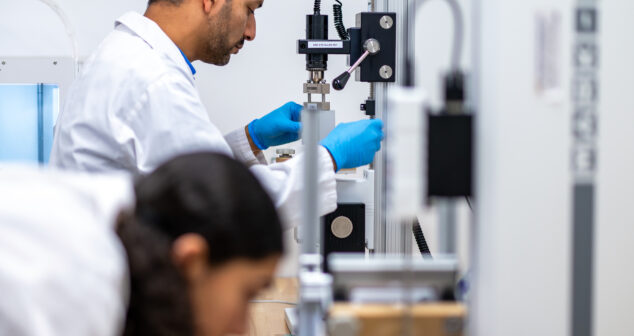
Multiple Services under One Roof
StarFish has the people, processes, and facilities to take your medical device or diagnostic from concept to commercial manufacturing. Start with consulting to clarify the value stream and continue through to quality and regulatory support. We provide engineering, human factors and usability testing, and low-volume manufacturing in house.
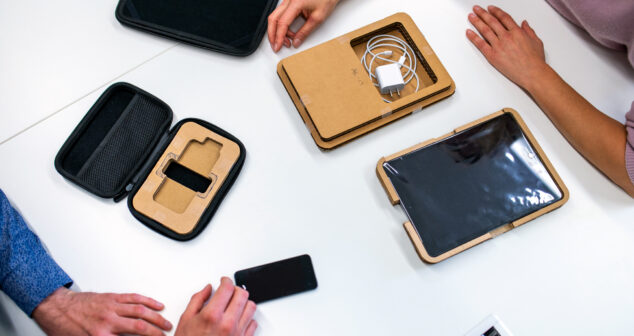
Rapid Prototyping and Product Builds
Whether you need a prototype to prove to investors that your technology works, a device ready for clinical trials, or a product for transfer to large-scale manufacturing, we’ll get you there fast, with zero compromises to quality.
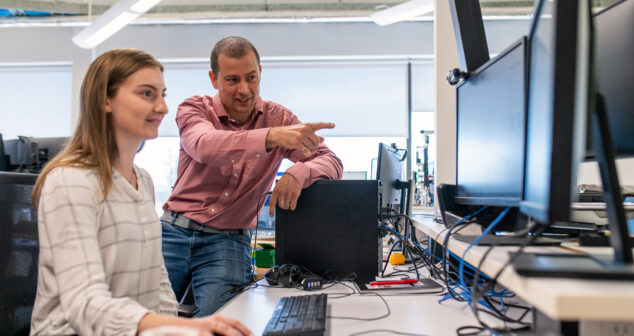
Agile Program Management
Our approach combines agile project management with scientific methods to meet your clinical objectives. Proven processes and a rigorous quality management system (QMS) are embedded in everything we do.
Explore Our Other Services
Related Resources
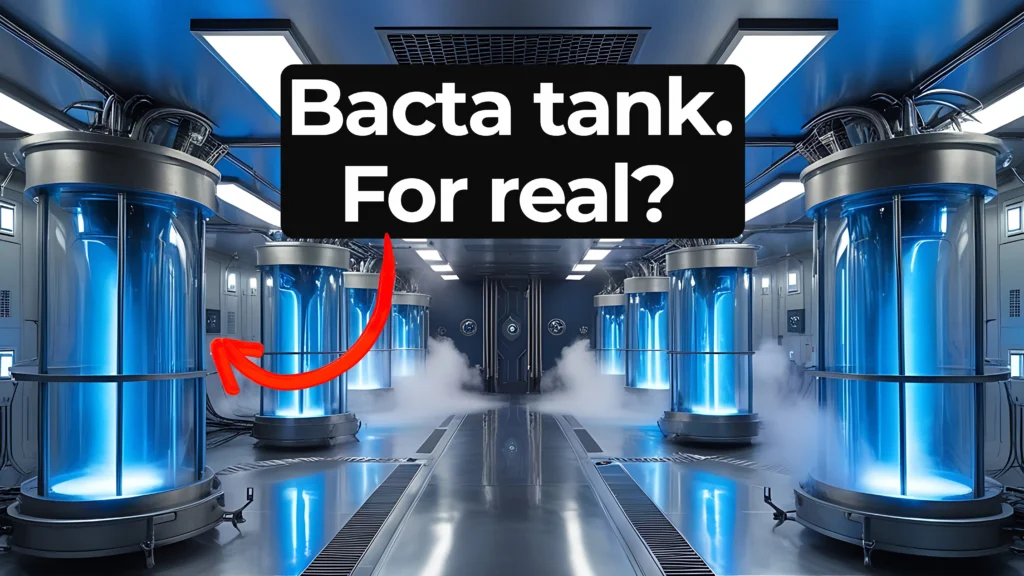
Ariana Wilson and Mark Drlik take inspiration from a scene in The Empire Strikes Back to talk about real-world parallels to the Star Wars bacta tank.
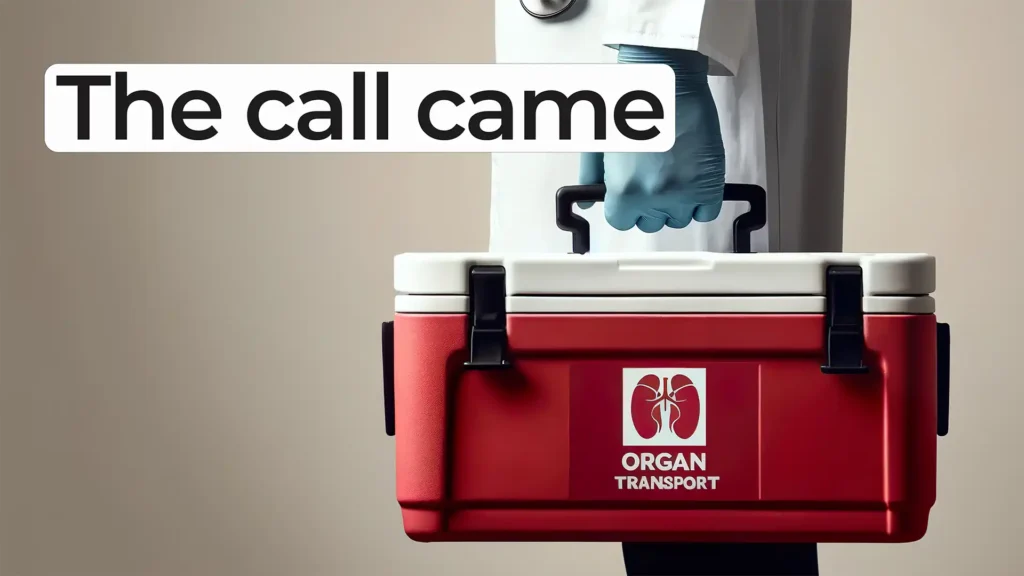
In this Before the Build episode, Eric Olson and Paul Charlebois dive into the importance of organ transplant logistics when designing effective medical devices.
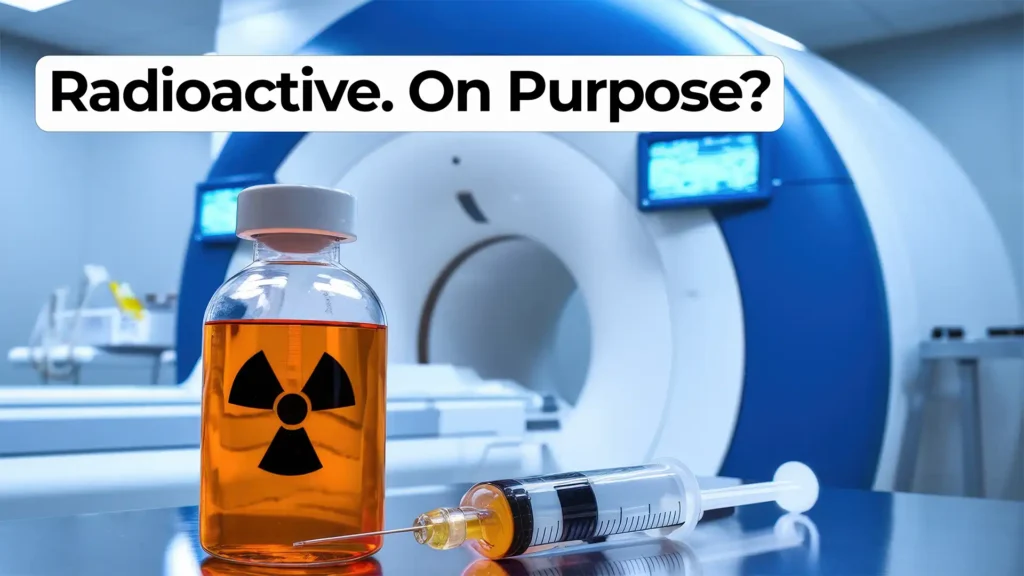
Radiopharmaceutical device development is gaining momentum as medical teams explore new frontiers in diagnostic imaging and cancer treatment.
Ready to explore how New Product Introduction / NPI services can enhance your product development?