Health Canada Interim Order: Our Experience
Prime Minister Trudeau announced StarFish Medical’s participation in the NGEN Canadian Emergency Ventilators project on March 31, 2020, as part of Canada’s Plan to Mobilize Industry to Fight COVID-19 and Health Canada Interim Order. StarFish Medical was asked to help supply ventilators for the Canadian healthcare system and to develop them rapidly so that they would be available for use should current supplies be insufficient.
We were very keen to participate in such a worthwhile endeavour and jumped straight into it.
Health Canada Interim Order – Introduction & Ventilator-Specific Guidance
Our design would be submitted utilizing the “Interim order respecting the importation and sale of medical devices for use in relation to COVID-19” published by Health Canada on March 18th, 2020.
The Health Canada Interim Order provided the key information for what would be needed to be included in our submission.
In addition, on March 25th, 2020, Health Canada published “Notice: Importation or sale of ventilators – use of US FDA guidance and Canadian requirements for authorization under the Interim Order” which was subsequently updated on April 21st, 2020. This laid out their expectations specifically for a ventilator submission. The guidance provided more detail on each section of the submission and what information should be provided.
Clear communication with Health Canada throughout to ensure expectations are set
We knew that the key to ensuring a smooth submission process would be to align our plans with the expectations from Health Canada Interim Order submissions.
We took the opportunity to communicate with Health Canada several times during the project. Each time, we presented the current status of the project and our plans for the documentation that we were going to produce. This also allowed us to clarify specific details about relevant points.
We ensured that our technical team was involved in these discussions with the regulators, as well as members of the QA/RA team, so that all involved in the project were aware of what was going to be an acceptable submission package.
Health Canada Interim Order is minimal, but need to support final documents required with inputs
The Interim Order and associated guidance for ventilators required only a short list of information to be provided directly as part of the submission. However, we would need a full Design History File (DHF) to provide evidence for each of those requirements in sufficient detail for Health Canada reviewers to have confidence in our design.
The submission was forefront throughout the development of all the key DHF documents. We developed the summary submission documents as soon as the relevant information was available from the DHF documents. We also endeavoured to minimize repetition of work between the DHF documents and the submission documents. Health Canada agreed that they would accept our DHF document directly as evidence. This was facilitated by the Interim Order allowing for the submission to be provided “in any format” rather than a normal submission format.
Understanding the sequence of sharing of information
One of the key understandings needed to ensure an efficient run up to the submission was the order that information needed to flow through the different documents. This dictated the order in which the documents could be created / updated. That allowed us to plan out when documents would be finalized, who would be doing that finalization, and to notify reviewers and approvers of these plans to enable them to approve documents without delay.
For example:
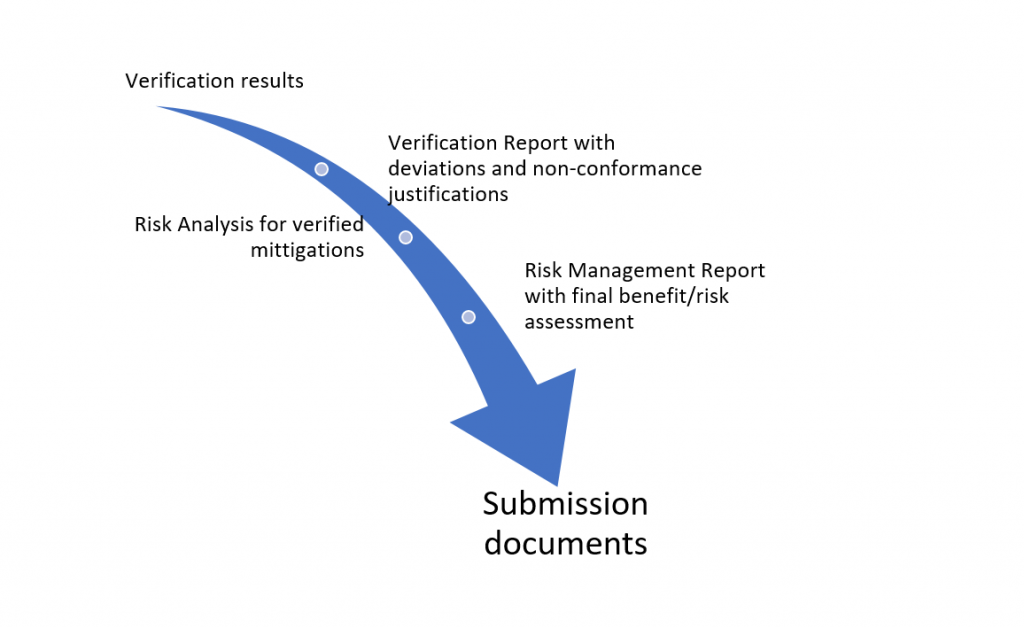
Setting up efficient methods for processing results
Because the verification data was needed for several submission documents, it was particularly important that we efficiently managed and processed results as soon as they were received. With over 300 individual specifications to test, we would be handling a large number of results and we would need careful planning.
We grouped the specifications into areas which made sense to test together; for example all the alarms, all the core parameters related to each ventilation mode (volume control, pressure control, pressure support), etc. We assigned each area a verification team member who wrote a protocol which covered the specifications in that area in either a single test or in a group of related tests. We gave each protocol an identifier in the form VeP123 in order to track results each time the protocol was run. Naming the results VeR123 and the associated test date, made searching and matching of results to protocols much easier.
As part of developing these protocols, we took the opportunity to create protocol-specific results forms to aid in the capture of the key information during the testing of more complex protocols. The results could be combined with data analysis and processing from automated data sources (e.g. taking csv data files of readings and converting them into the average or high/low limit parameters defined in the specification).
We called upon a wide team to carry out the verification testing and run as many tests as possible in parallel. StarFish Medical worked with many partners. Verification help included staff from ViVitro and Forest Technology Systems (FTS). Our Verification Team Lead had the unenviable task of scheduling test equipment, people and protocols as and when each became available.
To expedite getting results into documentation:
- Write test results in relevant forms
- Have a dedicated QA team member review forms for quality control (QC) (e.g. all references correct, page numbers, signatures, all data entered, etc.) and enter them into the document control system
- Pass the forms onto the Verification Team Lead for review and confirmation of the pass/fail judgement. Discuss any deviations, non-conformances or omitted tests
- Enter the results into the summary report
- Review deviations and non-conformance justifications with the Regulatory Affairs lead to confirm acceptability from a regulatory perspective
Each person worked on an aspect of the process while the next set of results were being generated. At the completion of the report, the majority of the content had already been reviewed and accepted.
Accommodating last minute adjustments
No matter how good the planning, there were always last minute adjustments and late arriving results to be accommodated. Close communication between team members during daily huddles and via Microsoft Teams, allowed us to keep on top of the status of each of the documents.
Continual planning and mitigation of project risk to allow the submission to happen
All the documentation came together at a point just prior to the submission. The QA/RA team joined the project team and the submission package was divided up so everyone knew their role and document responsibilities. The relationship of the documents to each other was communicated within the team on a regular basis in order to plan who would be working on what, and in which order.
Taking the time to rigorously check as it is easy to lose focus when running fast
With so many verification results and so many documents to prepare for the submission, it could have been easy to make mistakes. It really was a “right first time” approach. Hence, we made sure to include plenty of time for review of technical content and QC for basic information consistency of references, terminology, formatting, etc.
We also looked at other potential risks in preparing the submission, such as key staff not being available, IT issues, or information not be provided when needed. Plans were put in place to mitigate these project risks. Submission preparation was a mini-project within the main ventilator project.
Three days after the final tests were complete, the submission came together and was sent over to Health Canada for review as planned.
The QA/RA team look forward to hearing from others about their experiences with Health Canada Interim Order submissions. Contact us to learn how we can apply these lessons learned to your medical device submissions.
Image: StarFish Medical
Helen Simons is a Senior Quality Assurance and Regulatory Affairs at StarFish Medical. Helen’s education is in Mechanical engineering, with a background of product development and QMS development across multiple industries with consumer and industrial products to medical devices, IVD and combination devices.