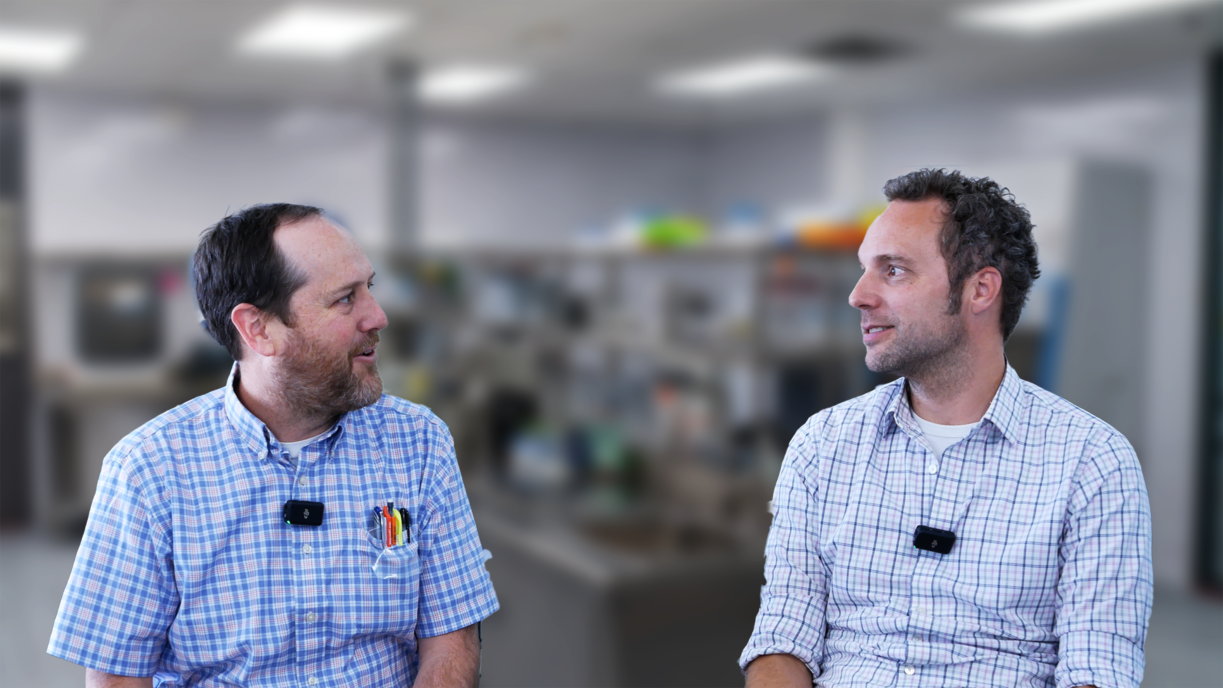
Bio Break: Why the Design History File (DHF) Matters in Medtech
When developing a medical device, documentation isn’t just a regulatory checkbox, it’s a fundamental tool for ensuring safety, traceability, and successful market entry. At the center of this documentation is an important file, the Design History File (DHF).
In this episode of Bio Break, Nick and Joris break down what a DHF is, why it’s required, and how it plays a vital role throughout the development lifecycle. A DHF includes all design documents created during development, such as product requirements, risk assessments, and verification reports. It’s the formal record that regulatory bodies like the FDA review to ensure a device was designed according to sound engineering practices and quality system procedures within the Design History File framework.
The conversation dives into why clients sometimes view DHFs as a burden, especially in the early stages of innovation where rapid iteration is key. To address this, StarFish Medical takes a two-phase approach. Initially, they prioritize flexibility and creative ideation. Small teams use light tools to explore feasibility, test concepts, and gain confidence before formal documentation begins. At this stage, they start gathering elements crucial to a comprehensive Design History File.
This approach helps teams avoid premature overhead while still aligning with regulatory expectations. It also ensures that once a device is ready for submission, the documentation is accurate, thorough, and aligned with the product’s risk profile and intended use, ultimately contributing to a successful completion of the Design History File.
Whether you’re a startup innovator or part of a large MedTech team, this episode offers a clear explanation of how design documentation supports both development and regulatory success, without derailing early creativity, and highlights the importance of the Design History File.
Learn more about StarFish Medical.
Related Resources
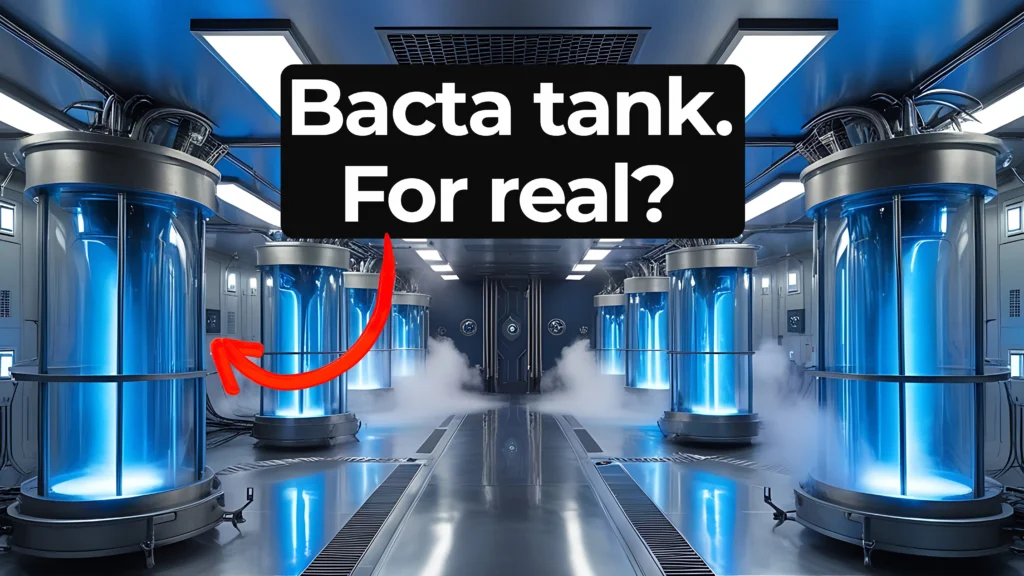
Ariana Wilson and Mark Drlik take inspiration from a scene in The Empire Strikes Back to talk about real-world parallels to the Star Wars bacta tank.
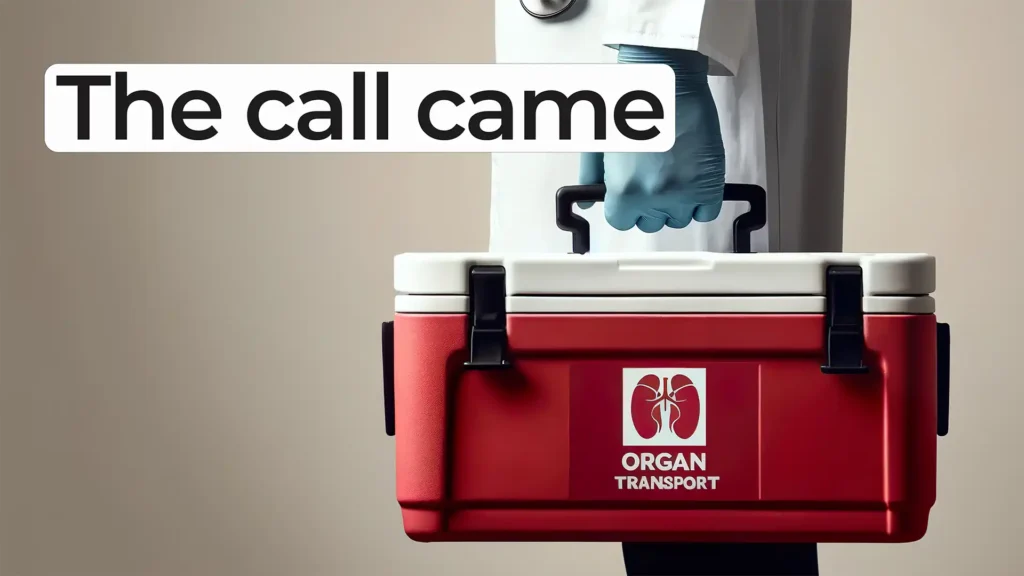
In this Before the Build episode, Eric Olson and Paul Charlebois dive into the importance of organ transplant logistics when designing effective medical devices.
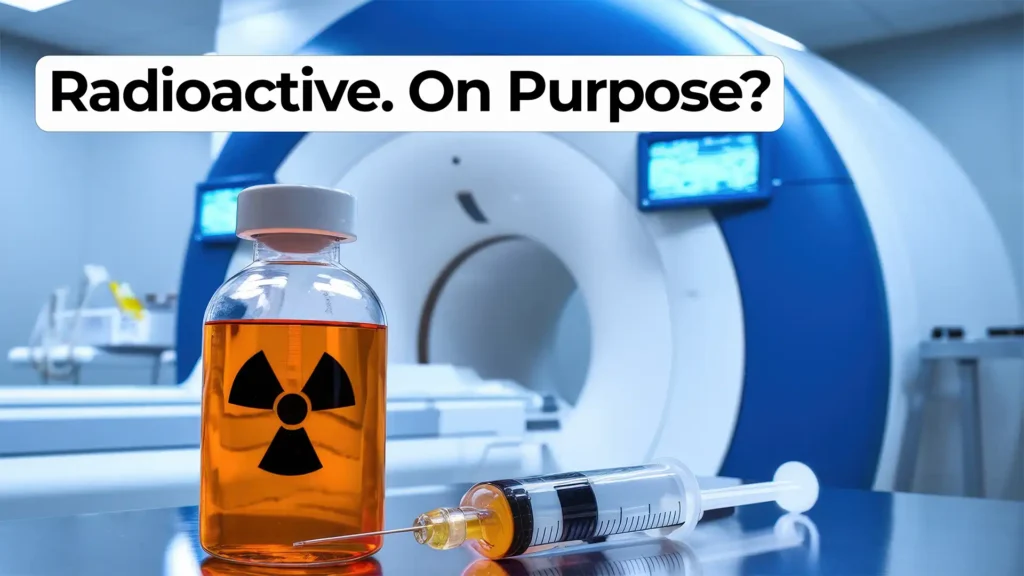
Radiopharmaceutical device development is gaining momentum as medical teams explore new frontiers in diagnostic imaging and cancer treatment.
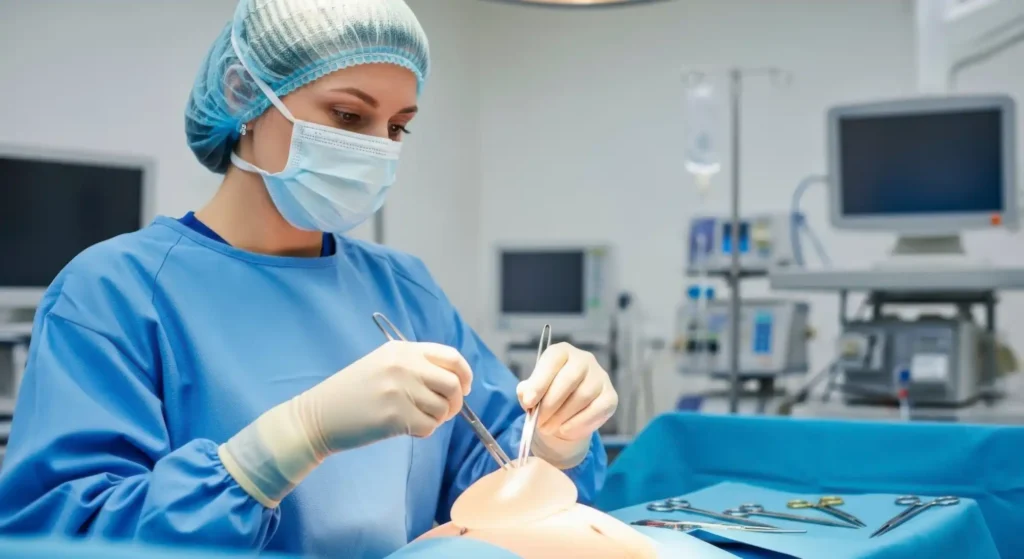
The simplest and least expensive way to train users of medical devices is to ask them study the Instructions for Use (IFU) beforehand.